Co-autor: Sverre Foslie –
Many industries requiring both cooling and heating currently have separate systems for the tasks. Integrated high temperature heat pumps and thermal storage tanks for combined heating and cooling allow for much better energy efficiency. This results in a corresponding reduction in energy consumption and CO2 emissions in the industry.
Results of a successful integration of high temperature heat pumps
The world’s first dairy with a fully integrated energy system using only natural refrigerants without additional use of fossil fuels or electric heaters was commissioned in 2018 and is located in Bergen, Norway. The integration of high temperature heat pumps and thermal storage tanks allowed for an extensive recovery and exploitation of waste heat, accounting for about 1/3 of the required energy consumption. In comparison to traditional dairy plants, the energy consumption was reduced by almost 40% or in absolute numbers by more than 5 GWh per year, corresponding to the equivalent of more than 250 Norwegian households. Thereby, for the integrated dairy, a CO2 emission reduction of more than 90% is possible (the exact figure depends on the type of energy used – electric heater, natural gas burner or district heating). This will save the equivalent of taking more than 340 petrol cars off the street.
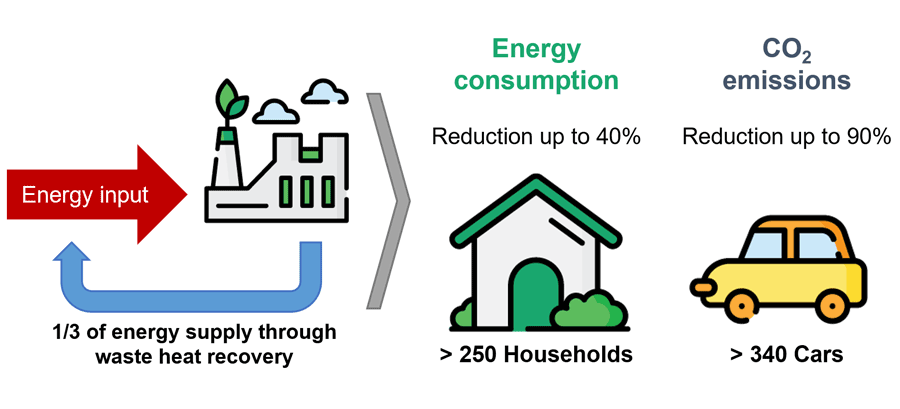
Why is the decarbonisation of industrial processes important?
Decarbonisation of the industrial sector is one of the most important keys to reduce global warming. Many industries are facing increasing energy demands which result in increasing greenhouse gas emissions due to the use of fossil fuels. About 2/3 of the demand is to provide thermal energy for process heating. Additionally, several industrial processes have a thermal demand for heating and cooling at the same time. Many examples can be found in the food processing sector as well as various emerging applications with growing importance, such as the operation of data centres or the production of batteries. Here, waste heat is often available in temperature ranges that do not allow for direct use – or where the demand at the given temperature level is insufficient.

How high temperature heat pumps contribute to the decarbonisation
Heat pumps upgrade heat from a low temperature level (waste heat) to a high temperature level (process heat). This is achieved by applying additional energy, which in most cases is electricity. The usable heat output is usually greater than the electrical input by a factor of 2 to 5, which makes the implementation of heat pumps very effective for the transfer of any type and amount of heat. This ratio of heat output to electrical energy input is known as the coefficient of performance (COP) and is used to describe the efficiency of a heat pump.
How does a heat pump work?
The most common system is the vapor compression cycle, where a refrigerant undergoes various changes of state in a closed circuit. Starting from the low-pressure side in the evaporator, heat is transferred from the source to the refrigerant while the liquid evaporates. Through the compressor, the vapor is then lifted to a higher pressure and temperature level. In the condenser, heat is transferred from the refrigerant to the sink while the vapor condenses back to liquid. Finally, the expansion valve expanse the liquid back to the low pressure and temperature state closing the cycle.
Traditionally, heat pumps have been used almost exclusively for either cooling or heating purposes, transferring heat to or from external sources such as ambient air or groundwater. In terms of higher efficiency and due to the given requirements in many industrial processes, the best way is to use both functions of the heat pump combined. By integrating high temperature heat pumps, waste heat from cooling processes can be upgraded to valuable process heat, reducing significantly the demand for electricity or other primary fuel sources. This both increases the overall energy efficiency and reduces the dependence on external conditions compared to conventional processes against ambient temperature. Consequently, this is one of the most relevant technologies for the utilisation of waste heat, which is likely to experience a growing demand in the near future (linked article in Norwegian).
Ways to integrate high temperature heat pumps in industrial processes
The processing of dairy products requires large amounts of process cooling and heating. Traditional dairies often use stand-alone solutions to supply the various demands. Here, cooling is provided by a refrigeration system that releases surplus heat to the environment. Required process heat is provided by fossil fuel burners or electric heaters, both with efficiencies below 1 (compared to the COP of heat pumps ranging from 2 to 5). By using high temperature heat pumps to integrate the process, the waste heat from the refrigeration system can be upgraded to meet the process heat demand. An installation of several heat pump stages with heat storage tanks can further increase the efficiency in many cases. This is because processes often consist of consumers at different temperature levels and the demands can occur cyclically (in batch operation). An example of such an integrated heat pump system, where both cooling and heating demands are supplied by heat pumps at different temperature levels, can be seen in the figure.

A good integration results in extensive use of the available waste heat and thus a reduced demand for external energy inputs. During the investigation of the initially mentioned dairy, the process achieved a waste heat recovery rate of over 95% with a COP above 4 for the overall dairy plant.
What is important for the future?
With the aim of making industrial processes more efficient and decreasing greenhouse gas emissions, HighEFF – Centre for creating a competitive, energy efficient and environmentally friendly industry for the future is developing, testing and evaluating this and other solutions together with industry partners. The results of the investigated dairy have shown that the integration of high temperature heat pumps offers great potential for the decarbonisation of industry. The demonstration of possible applications and operating data of high temperature heat pumps will help to increase confidence and acceptance among potential users.
[1] https://www.sintef.no/globalassets/sintef-energi/industrial-heat-pump-whitepaper/2020-07-10-whitepaper-ihp-a4.pdf
[2] https://www.sciencedirect.com/science/article/pii/S1359431121001861?via%3Dihub
Pingback: Slik gjør vi datasenter mer miljøvennlig - #SINTEFblogg
Pingback: This is how we reduce data centers’ carbon footprint - #SINTEFblog
Pingback: Making heat pumps hotter to reduce CO2 emissions - NTNU TekNat