This surge is driving the digital transformation of battery manufacturing, aligning with Industry 4.0 to enhance efficiency and reduce energy consumption.
In this context, the BATMACHINE project, where SINTEF is a partner, emerges as a key contributor, creating intelligent machinery to innovate and improve battery production.
The main challenges faced by battery manufacturers include the need for process optimisation to meet increasing demand and quality control to ensure safety. The integration of real-time data is crucial to address these challenges, allowing for immediate feedback, efficient process adjustments, and proactive maintenance, leading to higher quality and safer battery products. In addition, new battery materials are developed requiring an agile production management and fast production ramp-up. We aim to create an optimised battery manufacturing hub, to address these challenges.
Components of the Hub:
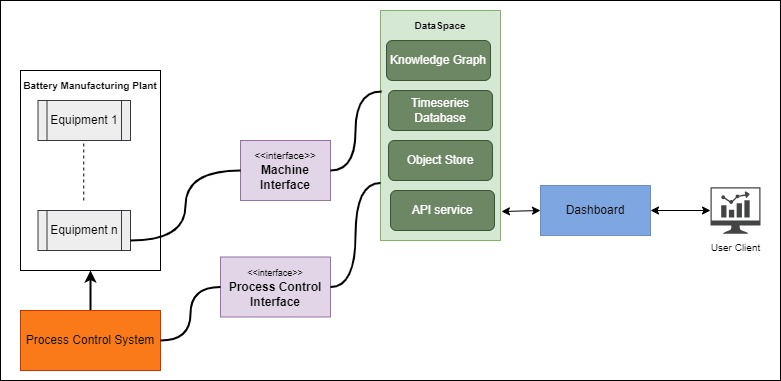
A dataspace is a collaborative and FAIR (Findable, Accessible, Interoperable, Reusable) data repository that stores all the time-series data collected from machinery used in the battery production line. The core knowledge related to the machinery is stored in a knowledge graph, while the machine-generated data is stored in a time-series database. Data models and other files of this machine-specific data are stored in the object store. Once the data is secured in the dataspace, various interfaces/services enable access and interaction to use this data into the realm of process control to optimise the manufacturing process. Additionally, an API is provided to simplify data access. The predefined interfaces are specifically designed for process control or other customer-specific needs, offering ready-to-use solutions. In contrast, the API offers flexibility, allowing users to query data as needed and seamlessly integrate it into their existing systems for more efficient use.
To facilitate efficient communication and data sharing, we will implement digital interfaces that efficiently connect various battery manufacturing equipment, process control systems, and engineers. These interfaces will lay the foundation for improved collaboration and secure data exchange.
The process control interface facilitates process optimisation by connecting the dataspace directly with manufacturing machines. It provides essential information from the previous manufacturing steps to increase adaptability and production efficiency . This data, which may encompass various parts of the process, can be easily combined and utilized using semantics.
All data from the machines, as well as the inputs to the process control, are documented, with an ontology serving as a common vocabulary. This ensures that the data is processed efficiently. The process control system then sends real-time feedback and control commands to the machines, allowing them to adjust operations based on analysed data and manual instructions. This creates a feedback loop that ensures the machines operate at peak efficiency, address issues swiftly, and adapt to the dynamic conditions of the manufacturing environment.
The machine interface will register manufacturing equipment and automatically populate the dataspace with equipment details and specifications.
A dashboard (graphical user interface) will also be provided, displaying key production data the user/engineers can monitor. It includes a time-series visualiser, that displays the data evolution from machines, which can be used to understand the performance and state of the machines.
Two additional components are included for offline analysis. A query builder or search, which will help in generating sophisticated queries to track relationships within battery manufacturing processes. And a knowledge graph explorer which will visualise semantic relations and filters the knowledge graph to present only the relevant information. It allows users to focus on the parts of the graph that are pertinent to their needs, making it easier to identify patterns, connections, and insights related to battery manufacturing processes.
All the above components will be bundled together as a customisable deployment package, designed for on-site implementation within battery production facilities. This approach is critical, particularly because numerous pieces of industrial machinery may restrict cloud-based interactions due to security concerns. Hence by integrating manufacturing elements, and effectively utilising the collected/generated data, we can enhance process control and system monitoring and enable better decision making and support the transition towards sustainability.
Comments
No comments yet. Be the first to comment!