Co-authors: Ragnhild Jensen (Elkem) and Ingeborg Solheim –
Silicon production involves releasing CO₂ in the atmosphere – about 5 tonnes of it for every tonne of silicon. CO₂ capture is a solution being explored to remove these emissions, but the CO₂ concentration in furnace exhaust gasses is often too low to make CO₂ capture possible cost-effectively. One possible solution to this problem is to increase the CO₂ concentration by recirculating the exhaust gas. Silicon manufacturer Elkem tested this in a pilot project, together with NTNU and SINTEF.

Ambitions for a carbon-neutral production
Silicon production is an important industry for Norway. Silicon is used in electronics, solar panels, silicone, and as an alloying element in casting alloys. Silicon production is done by carbothermal reduction of quartz, and results in relatively large CO₂ emissions.
Elkem strives to achieve carbon-neutral metal production, and has launched several initiatives to reduce its climate footprint. Energy recovery, increased use of biocarbon materials and improved material yield are included in this work.
In addition to these measures, solutions must be found to enable CO₂ capture from the furnaces. Elkem conducted an initial carbon capture study, with support from the CLIMIT program. To different capture technologies were examined, in collaboration with Aker Carbon Capture and Saipem, respectively. Norsk Energi contributed to assessing optimal solutions for energy supply and recovery. One of the challenges of CO₂ capture from melting furnaces is that the CO₂ concentration in the exhaust gas is low, typically just a couple of percent. This makes setting up an integrated carbon capture plant both costly and technically challenging.
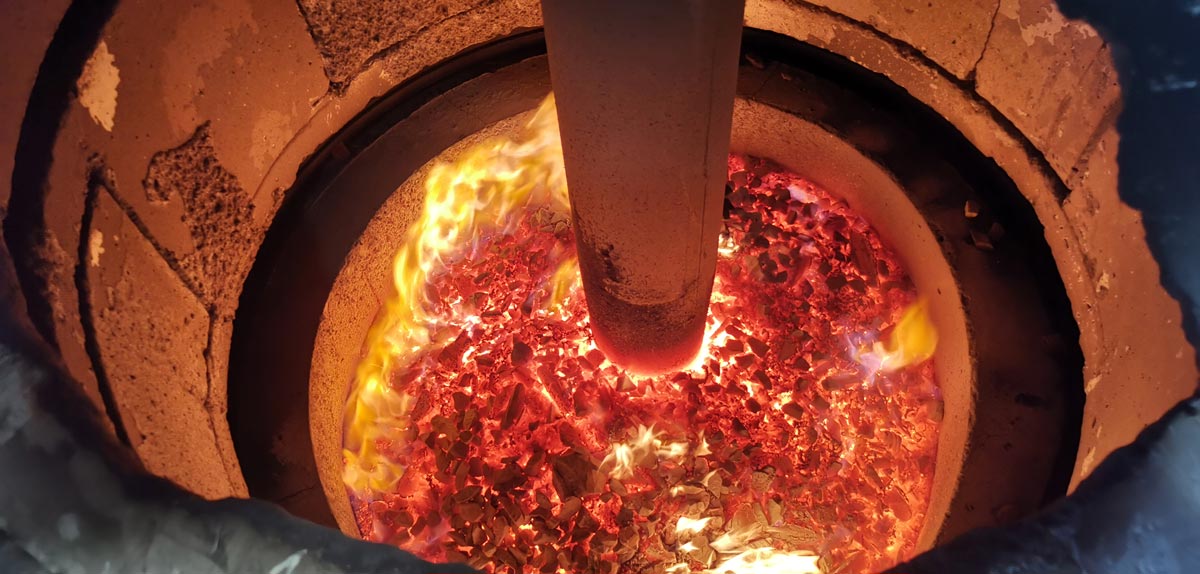
As a possible solution to increase the CO₂ concentration in the exhaust gas, Elkem – together with the research community at NTNU and SINTEF – is looking at recirculating exhaust gas. By replacing a portion of the fresh air that is normally added to the furnace with recirculated exhaust gas, cleaned of particles and cooled down, the CO₂ concentration of the exhaust gas will be increased. This is a well-known technology for NOx reduction in incinerators, but the method remains to be tested in practice for silicon melting furnaces.
The pilot project
To map the effects on the smelting process of such off-gas recirculation, a pilot scale experiment was carried out at NTNU and SINTEF’s pilot laboratories at Gløshaugen, in Trondheim. There, research scientists built a unique recirculating plant around an existing 160 kW single-phase melting furnace. To obtain as much information as possible on the effects of recirculation, the furnace was equipped with instruments and analysis equipment. These would help gathering knowledge about the impact of recirculation on other products and emissions from the furnace.
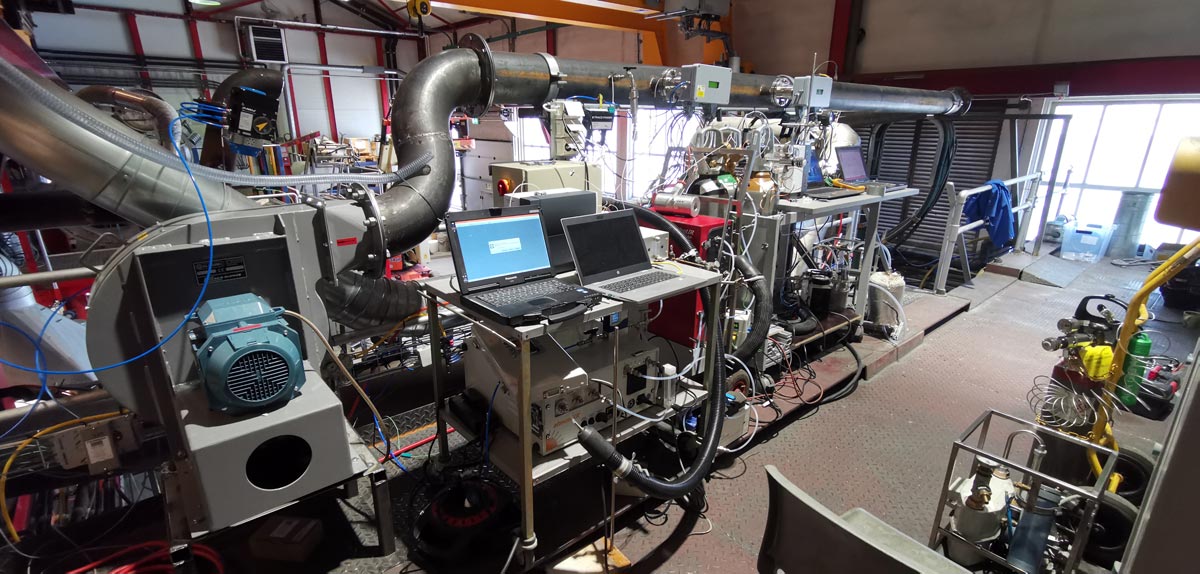
The pilot project was achieved through a broad and very good collaboration between the Elkem projects Elkem CCS and Elkem Sinoco2, as well as FME HighEFF and SFI Metal Production. During an 80-hour test run, different recirculation rates were tested and mapped. Elkem provided skilled operators from Elkem Thamshavn, as well as raw materials, while SINTEF and NTNU were responsible for controlling the furnace and performing the measurements. By increasing the proportion of recirculated gas, CO₂ concentrations above 20% were achieved. A lower NOx production was also observed as the recirculation proportion increased.
A lot of data analysis remains to be done to interpret these results, but the experiment shows that recirculation has a lot of potential to reduce NOx emissions and make CO₂ capture easier for the silicon production process. The unique infrastructure built in Trondheim will be very valuable for future experiments and projects aiming at making metal production more sustainable in Norway and around the world.
0 comments on “Recirculating exhaust gas in silicon production”