If we are to design and operate CO2 capture, transport and storage (CCS) systems efficiently and safely, we need to know more about CO2’s choked flow – that is, its maximum flow rate through valves, holes or other restrictions. This has been the subject of a new paper: Experiments and modelling of choked flow of CO2 in orifices and nozzles.
What is choked flow?
In the ‘old days’ when I was a boy, cars had a ‘choke’ lever. It was employed to limit the air flow and give a ‘fatter’ petrol mixture so the motor could run while heating up (yes, in those days you had to operate machines via levers instead of touch screens.) In CO2 transportation systems, we also have choked flow, although the mechanism is different. We say that the CO2 flow becomes ‘choked’ when there is a large pressure difference, e.g., when a valve is opened from a pressurised tank.
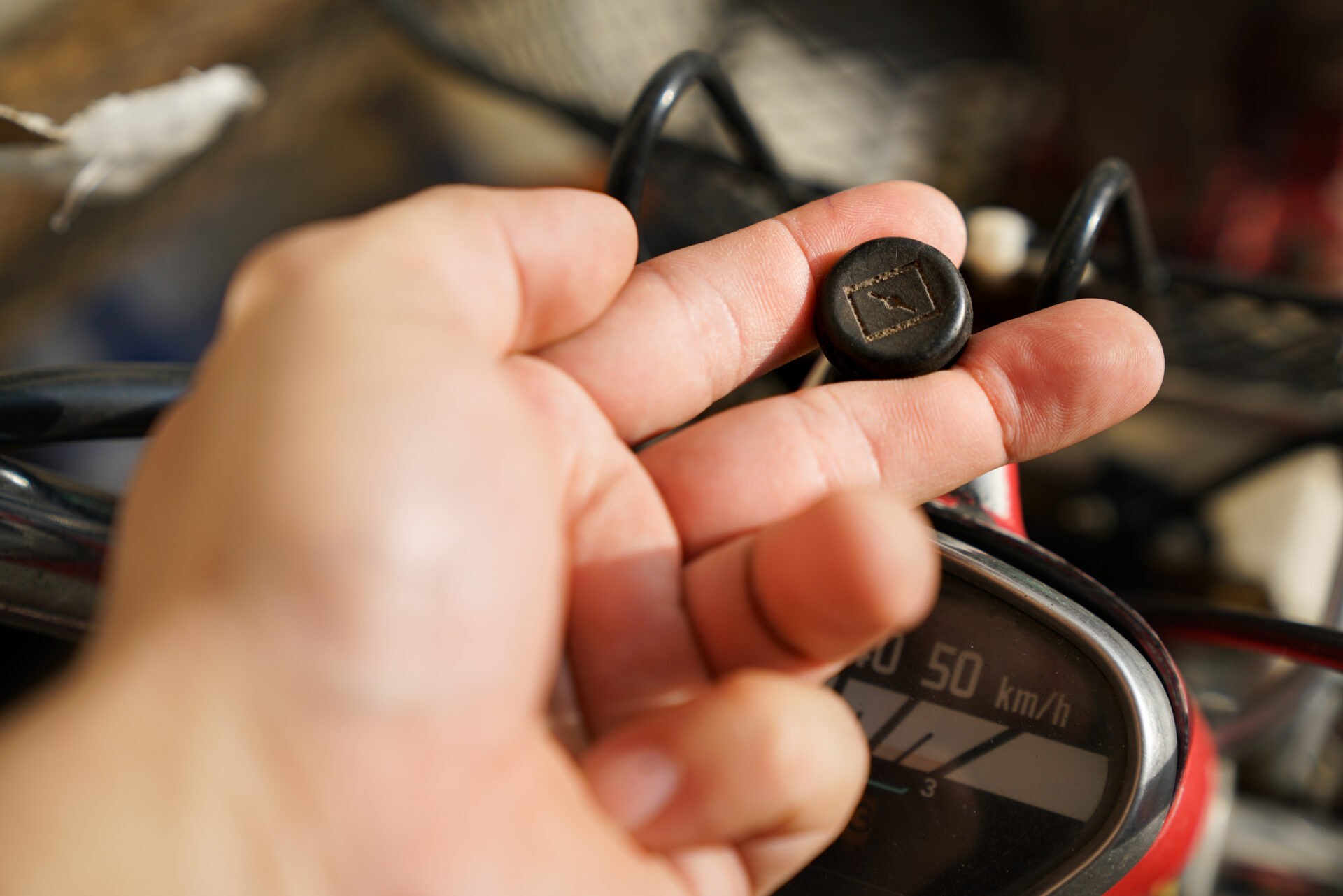
Fluids flow when subjected to a force, and in our case, that force is generated by pressure differences: the larger the pressure difference, the faster the flow. However, this only works up to a certain level. At an uncertain point, the flow velocity will become equal to the local speed of sound. This means that pressure waves cannot move against the flow, and the flow cannot accelerate more. This is called ‘choked flow’. For instance, when a valve reaches its maximum throughput, it means the flow is choked inside it – the fluid cannot flow any faster.
We care about this because we want to design and operate CO2 capture, transportation and storage (CCS) systems in an efficient and safe way. As such, we need to know how much CO2 will flow through valves or other restrictions, and what the resulting pressures and temperatures will be.
No cookbook for CO2 behaviour under pressure
Some of you will know that a ‘Cv’ value is often used to calculate the flow rate through a valve.
However, Cv values are commonly found for water, which is incompressible and behaves just too differently from CO2. Therefore, we need to be able to calculate how the CO2 behaves when the pressure is reduced from the initial state to the choke point. It turns out there is no ‘cookbook’ on how to do this. So, my colleagues Morten Hammer, Han Deng and Anders Austegard at SINTEF, PhD candidate Alexandra Metallinou Log at NTNU and I were happy to delve into the details. You can read about our findings in our recently published paper “Experiments and modelling of choked flow of CO2 in orifices and nozzles”. There are also data files to be downloaded together with the article.
In the study, we performed experiments in the ECCSEL Depressurisation Facility, where we have a tube specked with pressure and temperature sensors, which can be filled with CO2 at high pressures. At the end of the tube there is a rupture disk that bursts at a certain pressure, and then we can measure what happens to the CO2 inside the tube. In this study we checked the effect of restrictions using different sizes of nozzles and orifices.

The last word has not been said on this subject, but we were pleased that our not-too-complicated `delayed homogeneous equilibrium model’ (D-HEM) was reasonably accurate. We would like to continue working on it, to make it work for a larger temperature range.
This work was carried out in the Norwegian CCS Research Centre (NCCS), funded by industry and the Research Council of Norway.
Interesting
Interesing