(with contributions on membrane technology from Thijs Peters)
Carbon capture and storage looks set to take-off after decades of research. Francesco Finotti examines the latest technological initiatives and developing value chain (originally published in New Energy World magazine, published by the Energy Institute on 5 October 2022).
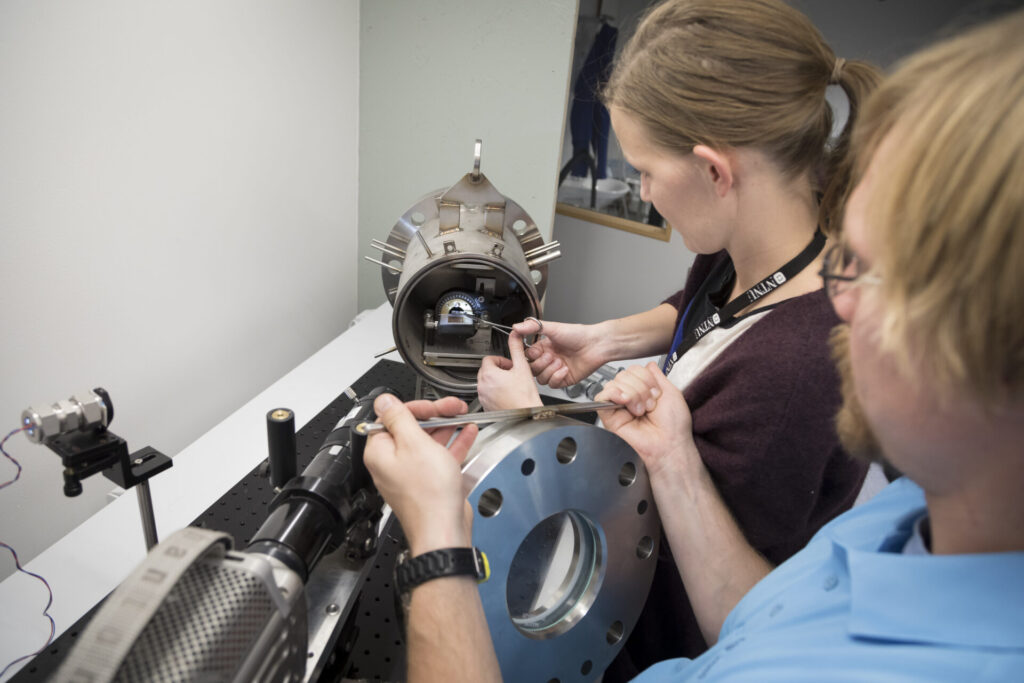
After more than two decades of research and development, and a few false starts, the Carbon Capture and Storage (CCS) market is set to blossom. Sustained governmental support and the foresight of the research community and key industrial actors have put Norway at the forefront of this development.
Since the introduction of the CO2 tax in 1991, Norway has been a pioneer in the field of CCS. It has more than 20 years of experience in CO2 storage in the Sleipner and Snøhvit enhanced oil recovery projects on the Norwegian Continental Shelf, in addition to an extensive public funding program, CLIMIT, managed by the Research Council of Norway (R&D) and Gassnova on pilot projects.
The most evident result of the effort to implement CCS is the development of the world’s first open-source CO2 transport and storage infrastructure, Northern Lights, as a step toward deploying CCS on a commercial scale. Phase one of Northern Lights is due to be completed in mid-2024, with a storage capacity of about 1.5 million tonnes of CO2 per year. However, this is a drop in the ocean compared to the IEA Sustainable Development Scenario, which requires almost one billion tonnes of CO2 to be stored underground per year by 2030.
Fortunately, the winds of change for CCS aren’t just blowing in the far north. In the US, at least three major industrial hubs located next to the Gulf of Mexico are developing CO2 storage hubs. The Central Louisiana Regional Carbon Storage Hub is the largest one, with a total storage capacity of 1 billion metric tonnes of CO2.
The UK is also focused on CCS, having started the race to carbon neutrality in 2019, when the government set an ambitious emissions reduction target. Concrete examples of this commitment can be found in the HyNet North West cluster, which plans to be active by the middle of the decade. The project aims to capture up to 30% of the CO2 emitted from hard-to-abate sectors (such as the cement, fertiliser, and petrochemical industries) in the area of Liverpool, and sequestrate it in an offshore reservoir managed by ENI, 30 kilometres from the Liverpool bay. Repurposing existing assets is an essential component of this undertaking.
In addition, the Zero Carbon Humber cluster aims to build the world’s first net-zero industrial region, and store between 12 and 17 million tonnes of CO2 per year from heavy emitters such as British Steel.
These developments come from the understanding that CCS will play a significant role in hard-to-abate industry sectors. An especially promising application is in industries such as cement or aluminium. According to the IEA, CCS has the potential to be retrofitted to existing power plants that could otherwise emit 600 billion tonnes of CO2, thereby storing almost two decades of emissions.
The CCS chain
To enable CCS at scale, however, will still require considerable effort. The CCS chain can be divided into capture, transport, and storage. Prosaically, it means that the CO2 must first be captured and transported before being injected into a deep underground formation. The whole process cost estimates range between USD 80-150 per tonne of sequestered CO2.
New technologies
Capture technology, although widely considered commercially available due to innovative companies such as Aker Carbon Capture and Saipem, is the most expensive part of the chain. New and more cost-effective second-generation capture technologies, such as innovative membranes, are on the way.
In this respect, Hydrogen Mem-Tech AS has recently received an investment of 170 million NOK for the commercialisation of high-temperature membrane technology for hydrogen production with integrated CO2 capture.
Another example is CO2 liquefaction, which is a process designed by SINTEF that uses low-temperature liquefaction and phase separation for the purification and transport conditioning of the CO₂, making it more cost-effective to purify and ship.
Carbon capture on vessels is also being developed, led by Wärtsilä. There is a suggestion that large ships equipped with CO2 capture units are unlikely to deviate from their routes to CO2 collection hubs. Instead, a fleet of smaller vessels may provide this service while the ships are anchored, loading or offloading their payload.

New transport chains
Large transport chains need to be developed to ensure a sustained flow of CO2 to the storage sites. The CO2 will travel from smaller point sources to collection hubs. Small emitters will be able to transport CO2 via trains and trucks, larger ones may do so via barges or ships (if in the proximity of waterways). The hubs can be connected to the injection facilities via pipelines or large-capacity ships.
Transportation of CO2 via pipelines is not a new application. However, there are still technological areas that users and developers are focusing on. For example, Saipem is building a complete set of tools to predict and assess thermodynamics, system integrity and related safety aspects.
Transport of liquefied CO2 by ship started over thirty years ago, with the first CO2 tanker starting operation in 1988 in Norway. So far, the largest CO2 transport vessels can only transport up to 4,000 cubic meters of CO2, enough to meet the small needs of the existing CO2 market but not enough for future CCS projects. This is being addressed through innovative, large-scale ship designs from companies such as Moss Maritime, Wärtsilä and Larvik Shipping.
In addition, work is underway to develop optimised logistic tools, which will help shipping companies optimise their routes, and help storage companies understand where to strategically position the hubs in order to best serve the CCS value chain.
Cross-border agreement
The world’s first ground-breaking agreement on cross-border CO2 transport and storage, signed in September 2022 between Yara and the Northern Lights, did not come easily. In addition to an extensive industrial effort, large research centres supported by visionary partners and the government have helped mature the capacity and competencies needed to realize such an endeavour.
The Norwegian CCS Research Centre (NCCS), with a budget of over €50 million over eight years and more than 20 industrial partners, is the world’s largest research centre on CCS. It focuses on technologies and processes to ensure the safe and cost-effective implementation of CCS in Norway and Europe, and around the world.
Thanks to these cooperative centres, even more, ambitious CCS implementation plans are underway. The NCCS spin-off project LINCCS, aims to enable more than 100 million tonnes of CO2 to be stored on the Norwegian Continental Shelf per year by 2030, twice the current Norwegian CO2 emissions. Its partners include Aker Solutions, Equinor, Wartsila, Lundin, TotalEnergies, Wintershall DEA, Vår Energi, and the research institute SINTEF.
ACCSESS is another NCCS spin-off project, with the goal of making large-scale CCS implementation more accessible as a tool for decarbonising European industry and cities. The ACCSESS consortium consists of 18 partners from eight countries, which together represent four industrial sectors with the potential to drastically reduce their CO2 emissions. Its first project for CO2 capture, using Saipem’s CO2 Solutions technology on Hafslund Oslo Celsio’s mobile CO2 capture plant, has already started. At the end of the year, this technology will be moved to Technology Centre Mongstad for another testing campaign, with the addition of a rotating packed bed (RPB) absorber from PROSPIN.
Knowledge gaps that exist regarding the polymer materials that can be safely and effectively used in CO2 transport infrastructure (e.g. elastomeric seals, gaskets, pipe liners etc. as leakage seals and protective barriers), are being addressed in the CO2-EPOC project, financed by Equinor, TotalEnergies, Gassco and SAIPEM.
Finally… a big challenge
A key challenge for the future of CCS is to connect risk capital to innovators and opportunities to businesses in a timely manner. Decades of research with CCS have advanced promising technologies to the demonstration stage. Now that CCS is becoming an industrial reality, there is a strong need to bridge the technological “valley of death” that characterizes innovation – in other words, the gap between pilot testing and commercial deployment.
The process is not risk-free – a large amount of capital is required to propel these technologies to the commercial stage. The complex situation we live in calls for extraordinary cooperative efforts by a constellation of small- to large-scale actors.
Nevertheless, it will be highly remunerative to the ones brave enough to take the risk: in Virgilio’s words, fortune favours the bold.
0 comments on “Innovations in CCS and the development of large-scale, cost-effective offshore CO2 storage”