Challenging for industries to measure PAH emissions
There are multiple reasons to measure emissions. One is to report correct numbers to authorities. Another is to use measurement data to optimize processes. Sometimes it is possible to use the same measurement methods to achieve both, but different approaches are often needed.
The backdrop to the PAHssion project is the industry’s ambition of zero emissions. To reduce emissions to near zero, it is necessary to know when, where and how the pollutants form. Only then is it possible to adjust the process to hinder the formation. A challenge is that the lower the concentration is, the more difficult is it to measure it correctly.
There are standardised methods to measure PAH in emissions. The motivation for the PAHssion project was however that the industry felt that results from standard measurements could not be used for process optimisation. Even when measurements were carried out in accordance with all available rules and standards, the engineers experienced that the results pointed in all directions at once.
Read more about Metal Production and Processing – SINTEF
More knowledge
In the PAHssion project, 10 industrial partners and 4 research partners collaborate to meet this challenge. The industry has financed the project together with the Norwegian research council. The project has developed new strategies to measure PAH and more knowledge about how the PAH forms in different processes. The project have, among other things, made use of SINTSENSE – a sensor-based equipment developed by SINTEF:
Great variation
An important finding from the project is that the processes that forms PAH varies greatly, over long and short time periods. There can, for example, be fluctuations over minutes, hours, days, weeks, or months. There can also be significant differences between seasons. A way to follow the process variations with respect to emissions is to use sensors for emission monitoring which are able to catch all these fluctuations, even the fast ones. There are, however, no such sensors for PAH today.
Real-time measurements
The work in PAHssion has shown that in some cases, it is possible to use volatile organic compounds (VOC) in the gas as a so-called proxy for PAH. In such cases, a photo-ionisation detector (PID) can be used to monitor how the concentration in the gas varies from second to second. These detectors are commercially available and are used today to measure other organic gases. In PAHssion, we have shown that it is possible to use them also for PAH.
Process monitoring increases digitalisation
With SINTSENSE, we get signals from six different sensors simultaneously and one of these can be a PID. This is extra interesting for following own processes, because real-time signals can show which gas components are formed when. It is also possible to get the signals on a pc-screen and compare the variations of different gases and dust with other control parameters that tells something about the process. In a digitalised, industrial future, the signals from emission sensors will be integrated into the general monitoring and control systems.
Monitoring by proxy
Several industrial measurements were carried out in PAHssion, and they have shown that PAH emissions from most of the industries are dominated by PAH in gas form, known as volatile PAH. The volatile PAH are included in an even larger group of compounds known as volatile organic compounds. They are formed and destroyed in much the same way as PAH in industrial processes. We have seen that it is often possible to use the VOCs as a proxy for PAH. It is not, however, always possible and must not, for example, be done when there is a lot of dust in the gas.
SINTSENSE can improve emission estimates from standard measurements
The standard methods available to measure PAH are relatively expensive and labour intensive. Standard measurements are typically performed only a few (2-6) times a year. When the annual emissions are calculated based on only a few standard samples, it is not necessarily completely representative for processes that vary greatly.
By using a PID as a complement to standard measurements, the industry can design measurement programs (for standard measurements) that better represent the real emissions throughout the year. Thereby, it is possible to improve the annual reports to authorities and simultaneously strive to stop the PAH from forming in the processes at all.
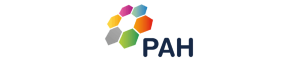
The PAHssion project is financed by the Norwegian research council and the industrial companies Elkem, Wacker, Finnfjord, Eramet, Ferroglobe, Fiven, Washington Mills, Tizir and Nemko Norlab.
R&D partners are SINTEF, NTNU, Norce og Eyde klyngen.
Comments
No comments yet. Be the first to comment!