At this stage, giving a concrete answer to this question is premature. In the ongoing pursuit of safer and more eco-friendly approaches to plugging and abandonment, bismuth-based alloys stand out for their potential to revolutionize wellbore sealing methods making them safer and environmentally friendly. This blog discusses our recently published literature review journal article in which we highlighted the merits of bismuth-based alloys as alternative plugging materials, and conducted a critical analysis of the existing challenges that must be addressed for their successful qualification as barrier materials.
Find out more about SFI SWIPA research center
What are bismuth alloys?
Bismuth (Bi) is a metal with a somewhat white, pinkish, silvery metallic luster. An interesting fact about bismuth is that once it oxidizes, unique rainbow-like colors appear on its surface (see picture below). This fooled alchemists and led them to mistake it for other precious metals like silver or tin. It was not until the 18th century that bismuth was recognized as its own distinct element. Apart from its colors, what makes this metal exceptional is its low melting point and its expansion upon solidification.
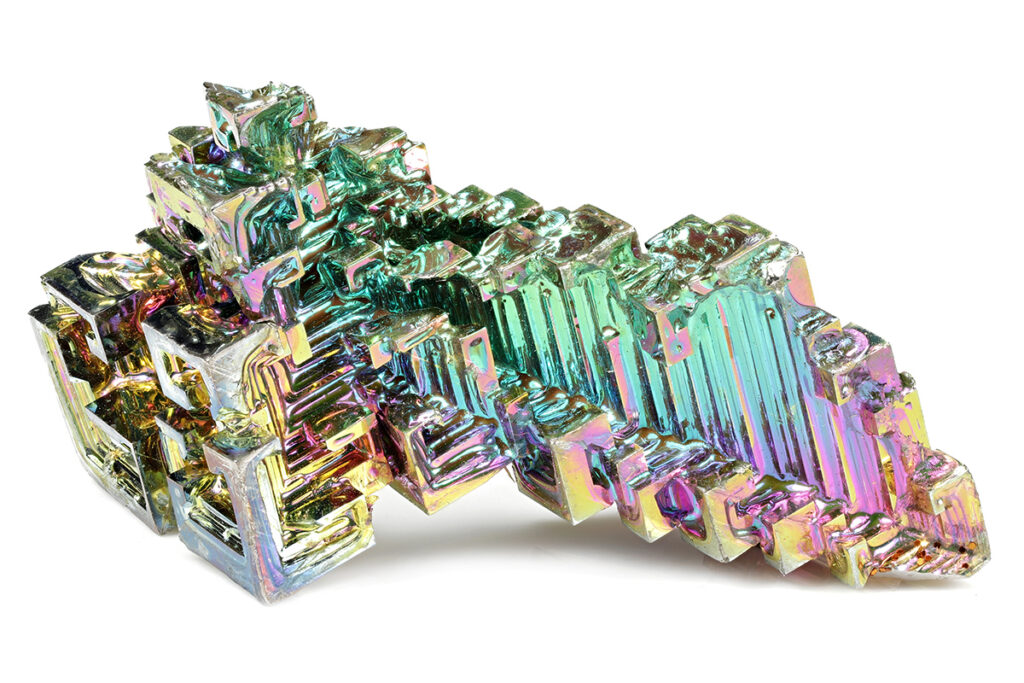
The existing literature and recent experiments indicate that bismuth is a potential alternative to cement due to a set of unique characteristics, such as:
- Relatively low melting point when compared to other metals (273℃)
- Viscosity which is very similar to water when it is in liquid form (melted)
- Very dense with a specific gravity (SG) of 10
- Expands approximately 3% upon solidification (like how water expands when it turns into ice)
- Non-corrosive and resistant to H2S and/or CO2
- Non-toxic (usually used as a substitute for lead in some applications)
- It is a eutectic metal which means that, when it cools below its melting point, it goes almost instantaneously from liquid to solid state bypassing the gel phase.
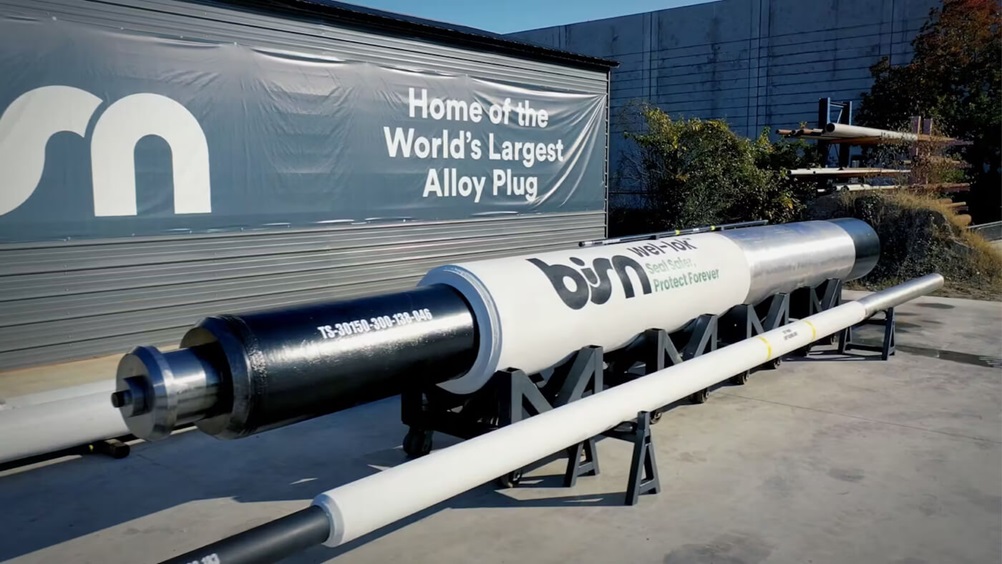
Why bismuth in P&A?
P&A operations may have considerable costs involved, and thus the development of new cost-efficient technologies is of great interest. According to the OEUK Decommissioning Insight Report 2022, well decommissioning accounts for 48% of expenditure, and this expense is forecast to increase dramatically over the upcoming four years, as seen in the figure below. The expectation is an increase of £325mn between 2022 and 2025 compared with the previous three years.
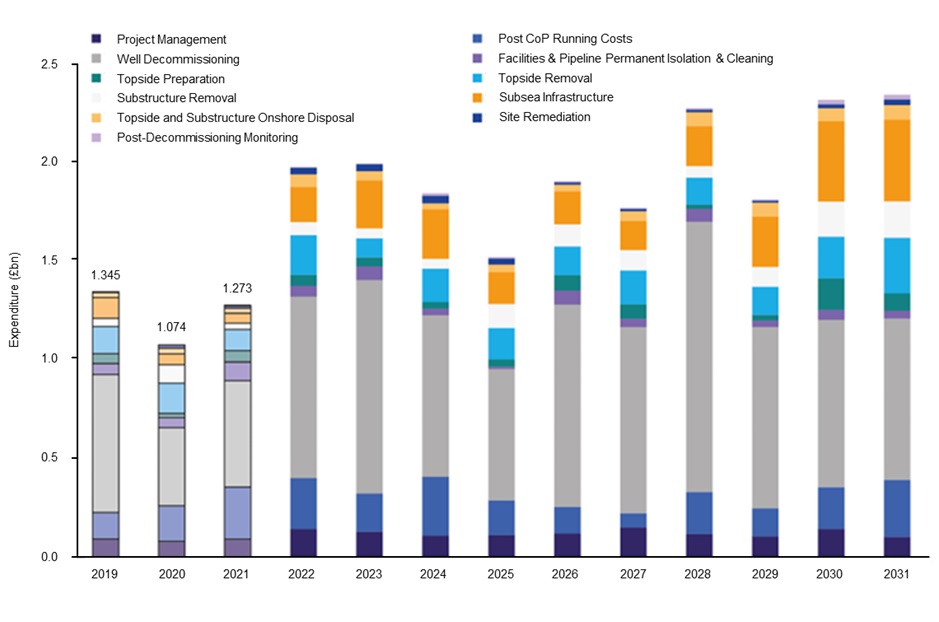
Here lies the interest in using bismuth as an alternative material. Bismuth plugs may provide better isolation with shorter plug lengths than what is required for cement thus favoring cost-effective P&A operations (Zhang et al., 2020). However, for proper usage, bismuth plugs must be qualified as barrier elements according to acceptance criteria described on the NORSOK D-010 (2021) for alternative materials. The plug length of any alternative material must be equal to or greater than what is required from a cement plug in the same scenario, as seen in the next table. Thus, there is interest in qualifying the bismuth plug to reduce these plug length requirements.
Open hole | Cased hole | Open hole to surface plug |
100 m MD (measured depth) with a minimum of 50 m MD above any source of inflow/leakage point.
A plug placed in the transition from open hole to casing should extend at least 50 m MD above and below the casing shoe. | 50 m MD if set on a mechanical/cement plug as fundament, otherwise 100 m MD.
If the qualified annular barrier length is 30 m and set on a mechanical/cement plug as fundament the plug may be 30 m. | 50 m MD if set on a mechanical plug, otherwise 100 m MD. |
Table 1: Minimum cement plug length for different scenarios (NORSOK D-010, 2021).
Potential Applications:
Bismuth-based alloys, especially bismuth-tin, have been tested and employed for several applications (Fulks and Carragher, 2021) such as:
- Single bore isolation
- Single annulus isolation
- Isolation of sustained casing pressure
- Zonal isolation including “squeezing” production perforations
- Multi-annulus isolation
- Water shut off through gravel pack screens
- Sealing leaking DV tools
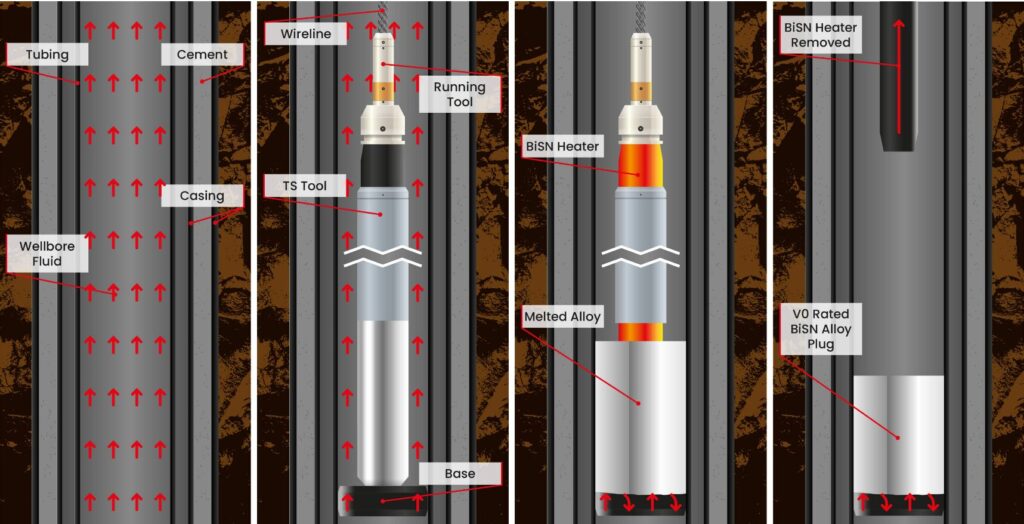
Challenges
Despite the promising advantages of bismuth-based alloys, several challenges remain in fully qualifying them as barrier materials. Our research not only presents these innovative alloys as promising alternatives but also highlights and discusses the need for further investigation into their long-term performance and impact on other well barrier elements. Some of the major challenges highlighted were:
- Thermal Shrinkage
- Thermal Shock
- Effect of its expansion on the annulus cement
- Creep
- Liquid metal embrittlement
- Availability of bismuth and its consequent cost upon higher demand
Advantages | Limitations and disadvantages |
|
|
Table 2: Summary of advantages and disadvantages of using bismuth plugs (adapted from Khalifeh and Saasen, 2020; Rios and Ars, 2021).
As the industry moves towards more sustainable and safer plugging and abandonment practices, bismuth-based alloys offer a glimpse into the future. Their potential to provide reliable, durable, and environmentally friendly sealing solutions positions them as a primary alternative to traditional sealing materials. However, the journey from the laboratory to the field is complex, requiring continuous research and collaboration across the industry. We invite you to read our paper, engage with our findings and keep an eye out for more upcoming publications! Your feedback and recommendations for future work would be greatly valued.
Read the full version of the review article:
Read more from the same author on this topic:
References
NORSOK D-010, 2021. Well Integrity in drilling and well operations, Revision 5. Standards, Norway
Comments
Good work!