Bismuth alloys are promising alternative to cement for plugging and abandonment of wells in oil and gas fields. This study reveals that the Bismuth-tin plugs cured under pressure result in fine microstructure and can withstand higher hydraulic pressure.
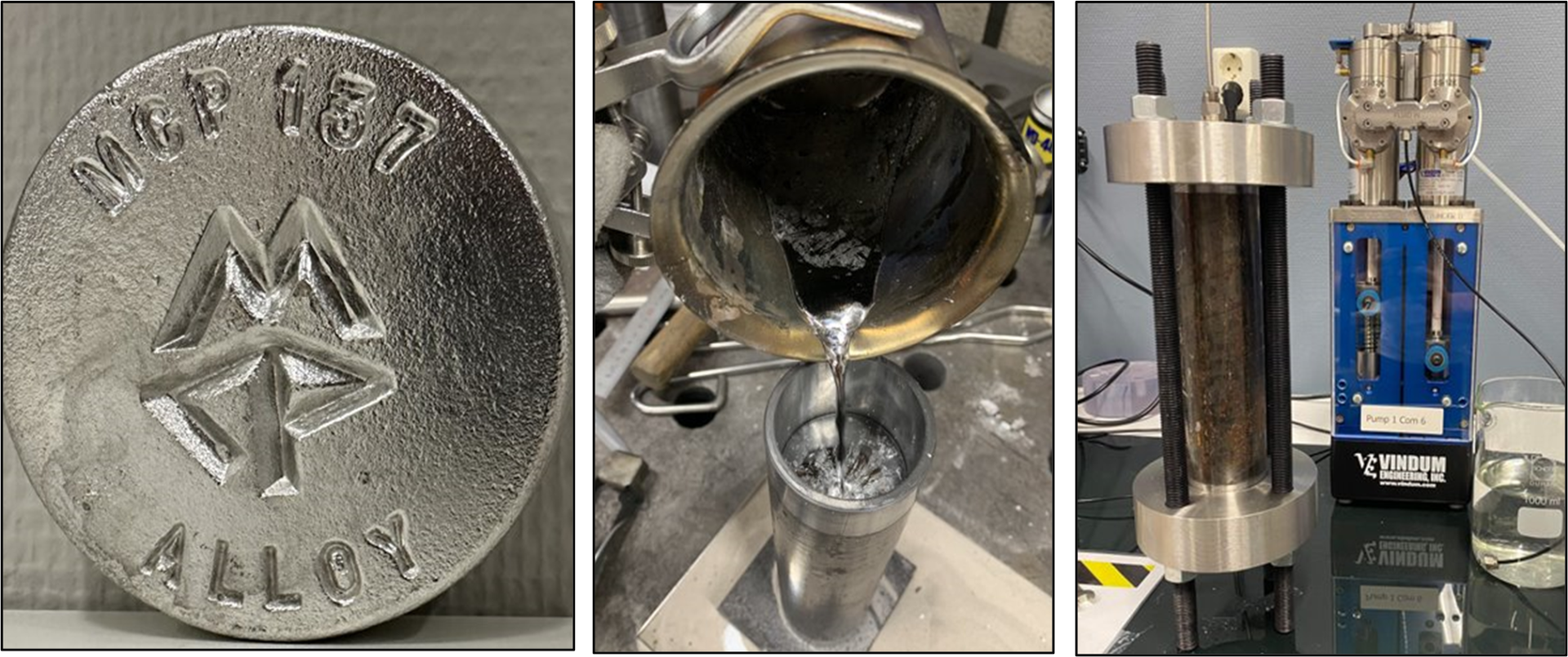
It is essential to underline the need for a reliable well-barrier material for plugging and abandoning wells in oil and gas fields. As a well approaches the end of its operational life, permanent plugging and abandonment become imperative tasks, requiring effective well-barrier materials to prevent potential leaks of hazardous fluids into the environment. Cement plugs have been the primary choice for this purpose. However, due to various drawbacks observed over time regarding its long-term integrity, there’s a growing demand within the industry for exploring alternatives to cement.
While numerous studies have recognized bismuth alloys as promising alternatives to cement, offering potential improvements in well-plugging performance, it’s worth noting that this area of research remains relatively recent and ongoing. SFI SWIPA is a center for research-based innovation (SFI) appointed by The Research Council of Norway for 2020-2028. SWIPA has engaged researchers, PhDs and PostDocs to work for this specific area of well barrier materials, focusing among others, to bismuth-based alloys. The Bismuth-tin alloy (BiSn) is the most common one used in ongoing studies and has already been used in shallow depth wells.
How does a BiSn plug, used as a well barrier material, mechanically behave under pressure? Does pressure affect the microstructure of the BiSn alloy?
This blog discusses our recent findings published in the paper “A Sealability Study on Bismuth-Tin Alloys for Plugging and Abandonment of Wells” in the SPE journal. While the paper provides an in-depth analysis of the alloy’s sealability, this blog will focus primarily on the microstructural aspects of the study, which reveals that the BiSn plug set under 40 bar pressure had finer grains, resulting in a better mechanical behavior than a similar plug set under atmospheric pressure.
The outcomes of the hydraulic pressure tests are indeed consistent with the microstructural characterization results, which clearly explain the difference of the hydraulic pressure between the two samples.
This study demonstrates how pressure can influence the microstructure, which subsequently impacts the overall mechanical behavior of a material. By understanding the microstructure of materials, we can achieve improved performance in practical applications.
Which BiSn alloy was used for this study?
The MCP 137 alloy with 58% Bi and 42% Sn was the eutectic BiSn alloy investigated in the current study, provided in blocks by the 5N Plus company. BiSn is a metal alloy with a melting point of 138oC and properties listed in the table below:
Property | Eutectic bismuth-tin alloy (Bi58-Sn42) |
Density | 8.56~8.73 g/cm^3 |
Young’s modulus | 42.72~43 GPa |
Poisson’s ratio | 0.3426 |
Yield strength | 50~70 MPa |
Ultimate strength | 70~80 MPa |
Melting point | 135~139 °C |
Coefficient of thermal expansion | 15~17 μm/(m⋅°C) @ 20~90°C |
Table 1: Properties of the eutectic BiSn alloy
How were the samples prepared?
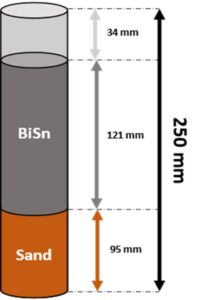
The preparation was as followed: after the BiSn was melted at 200 °C, it was cast into two steel X-52 pipes, over a compacted sand foundation, simulating the mechanical bridge plug practically used in oil and gas industry. The plug length is 121 mm and a gap of 34 mm from the top was left for experimental purposes. See figure 1 for the BiSn plug- steel pipe setup.
Two bismuth alloy plugs were prepared; the one left to solidify and cure for 48 hours at standard conditions, whereas the second was left to solidify and cure for the same period of time, under 40 bars of pressure, at room temperature. (The preparation of the second sample is described in detail by Hmadeh et al.
What kind of tests and analyses were performed?
Microstructural analysis was performed in order to explain the results of the mechanical tests, since the mechanical behavior of a material is directly affected by its microstructure.
One small specimen from each plug was prepared with the standard grinding and polishing techniques, in order to be analyzed by Scanning Electron Microscopy. A SEM-Hitatchi SU-6600 was used and operated at 25kV and electron micrographs were collected in the BSE (Backscattered Electron) mode (See figure 4).
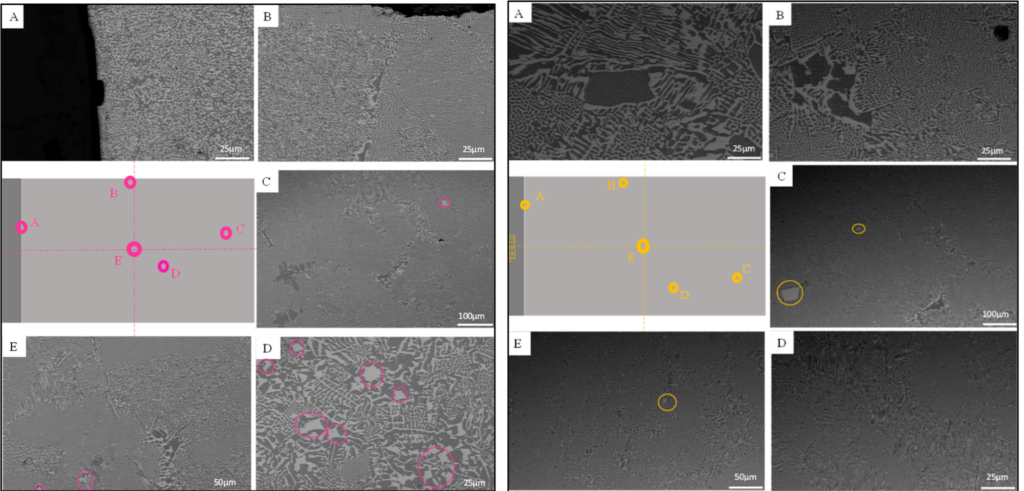
The coordinates of SEM images taken from the first sample are nearly identical to those taken from the second sample. In each image, the darker contrast represents the tin and the brighter corresponds to bismuth phases. (The eutectic BiSn alloy, which we focused on, has been extensively studied and detailed in prior research).
A summary of our findings:
- Sample 1 (Figure 4-left) shows both fine and coarse patterns, with the coarser patterns (circled in pink) dominating its microstructure.
- Sample 2 (Figure 4-right) exhibits a finer microstructure with more densely packed arrangements and only with just a few brittle Bi crystals (circled in yellow).
These findings can be explained by solidification theory and the effect of the grain size on materials’ mechanical properties. A material with finer grain size has more grain boundaries which in turn enhances resistance to dislocation, the unrestricted movement of atoms within a material that causes plastic deformation. Consequently, materials with finer grains exhibit greater hardness and higher yield strength compared to those with coarser grains. Additionally, another consideration is the presence of numerous coarsened Bi-rich phases in the first sample! Bi crystals are generally brittle in nature, and they can result in poor mechanical properties.
Both of the above observations conclude that sample 2, which was solidified and cured under 40 bar pressure, is the most suitable candidate for better mechanical properties.
Do the hydraulic push-out results align with this conclusion?
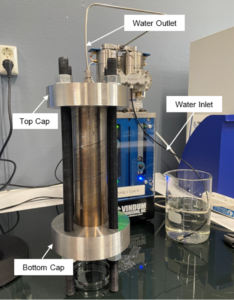
Ηydraulic push out tests were conducted, in order to indicate the hydraulic shear bond strength of the plug samples, using the experimental set up shown in Figure 2. The hydraulic bond strength is the pressure that the plug can resist before the leakage of the injection fluid starts, which in our study was water, or the plug detaches from the casing steel pipe. (The results of the tests depicted in the Figure 3).
The curves above indicate that the sample 2 which was cured under 40 bars pressure, can withstand higher hydraulic pressure than the sample 1 in atmospheric pressure. The sample 1 failed at 67 bar, whereas the sample 2 failed at 106 bar.
In simple words, the general conclusion of the current study is that the BiSn plug cured under 40 bars pressure, resulted in a finer microstructure, and therefore could withstand higher hydraulic pressure compared to the BiSn plug cured at atmospheric pressure.
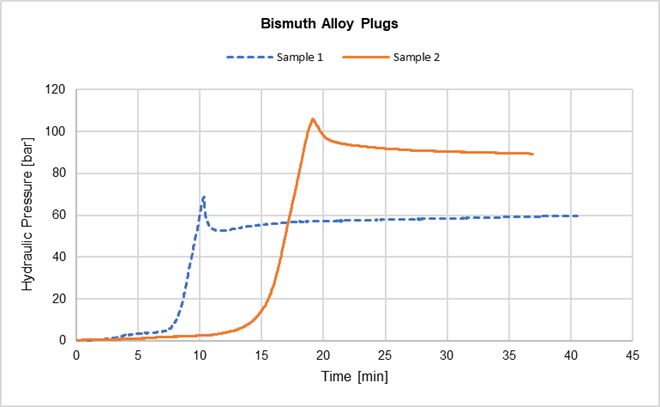
Read the full version of the article:
Read more on the investigation of bismuth-based plugs as alternative well barrier materials:
Manataki, A, Kontis, P, & Sangesland, S. “Investigation of the Microstructure of Bismuth Alloy and its Interaction With Cement and Steel Casing.” Proceedings of the ASME 2023 42nd International Conference on Ocean, Offshore and Arctic Engineering. Volume 9: Offshore Geotechnics; Petroleum Technology. Melbourne, Australia. June 11–16, 2023. V009T11A012. ASME. https://doi.org/10.1115/OMAE2023-103843
Hmadeh, L., Elahifar, B., Sangesland, S., Abrahamsen, A. E., 2023. A full laboratory study on the physical and mechanical properties of a bismuth plug. In: SPE/IADC International Drilling Conference and Exhibition. https://doi.org/10.2118/212561-MS
Hmadeh, L, Elahifar, B, Sangesland, S., 2023. The sealing behavior of bismuth-based metal plugs. In: Proceedings of the ASME 2023 42nd International Conference on Ocean, Offshore and Arctic Engineering. https://doi.org/10.1115/OMAE2023-104309
References
- L. Hmadeh, A. Manataki, M. A. Jaculli, B. Elahifar and S. Sangesland, “A Sealability Study on Bismuth-Tin Alloys for Plugging and Abandonment of Wells,” SPE Journal, 5 April 2024.
- M. Khalifeh and A. Saasen, Introduction to Permanent Plug and Abandonment of Wells, vol. 12, Stavanger: Springer Open, 2020, p. 273.
- L. Hmadeh, M. A. Jaculli, B. Elahifar and S. Sangesland, “Development of bismuth-based solutions for well plugging and abandonment: A review.,” PetroleumResearch, 2024.
- E. Thorstensen, K. Vadset, M. K. Straume, L. Delabroy, G. Abdelal, P. Carragher, J. Fulks and D. L. Mason, “Bismuth Plugs Used to Cap All Wells During the Final Phase of the Valhall DP Abandonment Campaign, Offshore Norway,” in Offshore Technology Conference, Houston, 2022.
- A. Manataki, P. Kontis and S. Sangesland, “Investigation of the microstructure of bismuth alloy and its interaction with cement and steel casing,” in International Conference on Ocean, Offshore and Arctic Engineering, Melbourne, 2023.
- L. Hmadeh, B. Elahifar and S. Sangesland, “The Sealing Behavior of Bismuth-Based Metal Plugs,” in ASME 2023 42nd International Conference on Ocean, Offshore and Arctic Engineering, Melbourne, Australia, 2023.
- “https://www.5nplus.com/en/,” 5N Plus, 07 2012. [Online]. Available: https://www.5nplus.com/media/uploads/products/product/product_sheet/balloy_137_tech_data_sheet_2016-07-22-15-34.pdf.
- B. L. Silva, G. Reinhart, H. Nguyen-Thi , N. Mangelinck-Noël , A. Garcia and J. E. Spinelli , “Microstructural development and mechanical properties of a near-eutectic directionally solidified Sn–Bi solder alloy,” Materials Characterization, vol. 107, pp. 43-53, September 2015.
0 comments on “Under Pressure: How BiSn Alloy Stands Up as well barrier material”