Accurate and traceable CO₂ measurements are required for fiscal and operational purposes across the CCS value chain. Fiscal metering is crucial for verifying compliance with the Emission Trading System and associated regulations while generating confidence in trading. Ultrasonic flow measurement technology has strong potential for use in large-scale fiscal metering systems for carbon capture and storage (CCS) due to its ability to handle large flow rates at virtually no added pressure drop.
Read more: What we need to understand about fiscal metering for trading CO2
The velocity at which a sound wave travels through a fluid, i.e., speed of sound, is key for developing models for characterising fluids, and designing and controlling transport and metering systems.
The speed of sound is also paramount in fiscal metering, as ultrasonic meters (USM) correlate the speed of sound through a given fluid with the fluid’s velocity. For this, USM use transducers that emit and receive sound waves across a pipeline cross section. The time it takes for the ultrasonic signal to travel between opposing transducers is dependent on the velocity of the fluid.
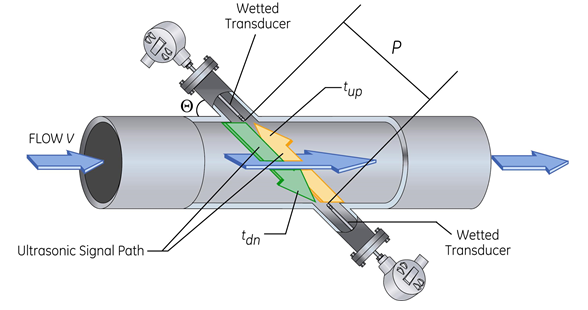
Sound attenuation and speed of sound of CO2
Sound attenuation and the speed of sound are intrinsically related to the design and operation of USM. Although attenuation is not unique to CO2, it poses a particular challenge to existing metering technologies.
High sound attenuation at frequencies at which the ultrasonic meters operate yields noisy signals. This can decrease the measurement accuracy and, at times, even completely impair the measurement if signals cannot be detected across the pipeline. Sound attenuation peaks for gaseous CO2 in the frequency range typically used in flowmeters, with attenuation coefficients of CO2 able to reach up to six times that of natural gas at 80 kHz. Therefore, thorough characterisation of the attenuation of CO2 at conditions relevant to CCS is beneficial for developing fiscal metering technology.
On the other hand, speed of sound data for liquid CO2 at pressures of interest for CCS (15-200 bara) are exceptionally sparce. The original work from Novikov and Trenlin, which was used to develop the Span-Wager Equation of State (EOS), comprised the only dataset encompassing pressure and temperature conditions relevant to liquid CO2 transport for CCS at the time. However, the authors did not provide a reasonable uncertainty estimation.
More recently, efforts have been made by the Thermophysics group at ICL to improve the sound speed data situation. Given the highly attenuative character of CO2, small amounts of propane had to be mixed with the CO2 to detect the sound signal through the medium. ICL experimental results show the most significant deviations from the reference EOS at pressures relevant for CCS transport, between 80 and 150 bara. This differs from the Wagner-Span and GERG-2008 EOS by 1% and 1.5%, respectively.
In recent years, SINTEF has performed bench tests on an ultrasonic flowmeter using liquid and dense CO2. The tests were conducted under static conditions, wherein the meter was used as a test chamber, and the speed of sound measurements were compared to EOS predictions. The experimental results have helped us to better understand the acoustic behaviour of liquid CO2, and aided the industrial partner in determining the operational boundaries of the meter for CCS applications.
Yet, the method does not allow us to perform tests over an extended frequency range. Therefore, the natural next step to expand the knowledge on CO2 attenuation is to study the frequency dependency of the sound velocity. A test chamber that particularly targets CCS operational conditions is being built within NCCS. For this, ICL expertise is of great importance.
Speed of sound test capabilities at ICL
ICL has two speed of sound cells: a pulse-echo chamber and a cylindrical resonator. The former has been used for CO2-rich mixture measurements in the past. In the dual pulse-echo cell, the ultrasonic piezoelectric transducer is immersed in the fluid between two communicating chambers of different lengths. Sound is reflected from the ends of the two chambers at different times, which enables the determination of the fluid speed of sound.
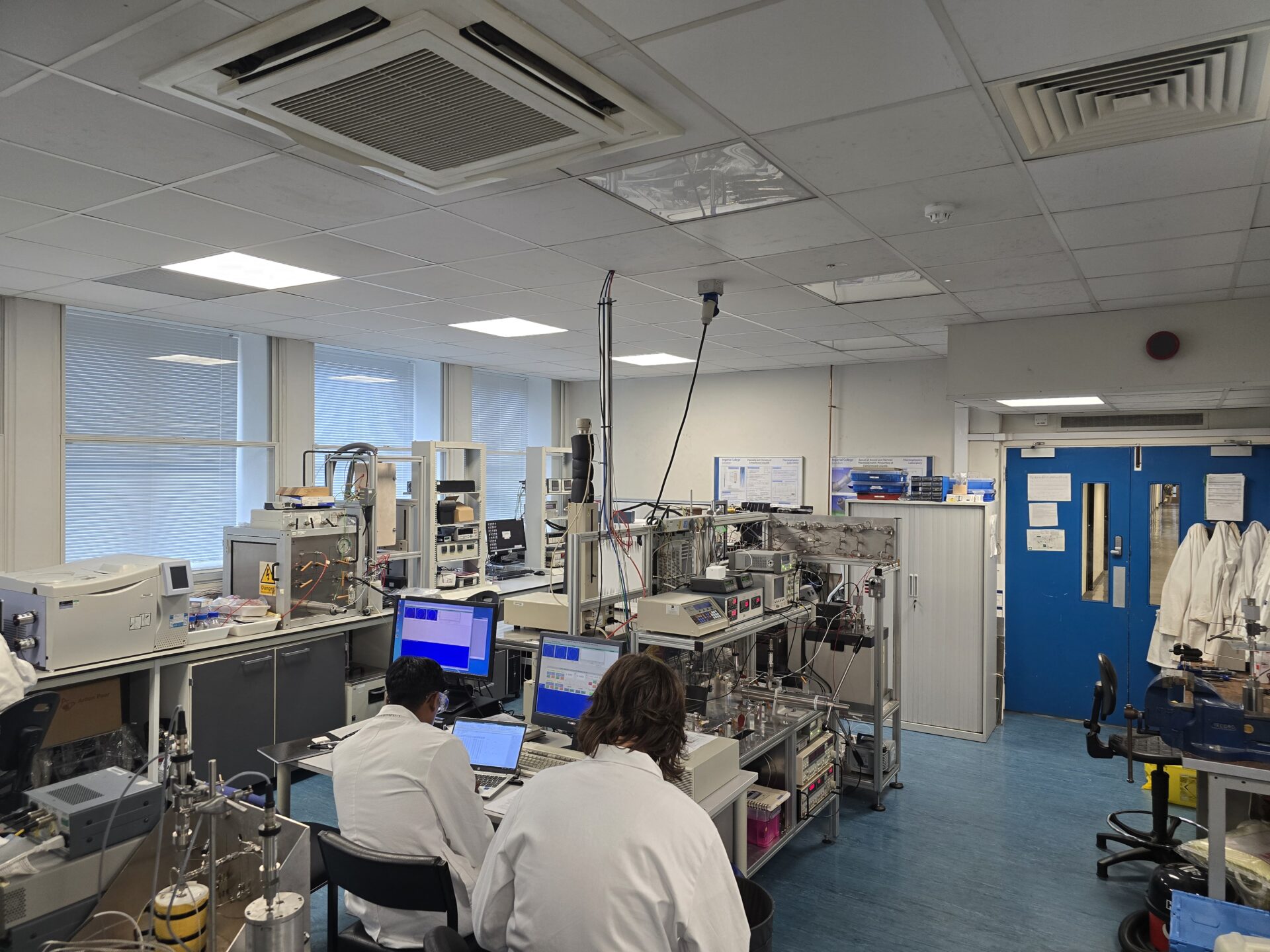
The second and newest cell is a cylindrical resonator. It has two opposing transducers: one acting as an excitation transducer and the other receiving the acoustic pressure wave within the cavity. The resonance frequency is measured by changing the driving frequency at a constant sinusoidal drive voltage. A range of frequencies is scanned to find the resonance frequency, which is then related to the speed of sound.
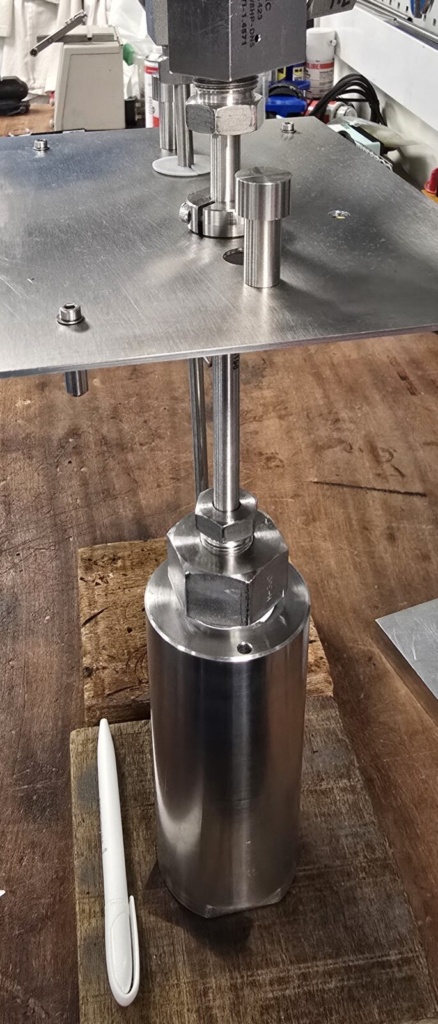
During the stay, the resonant cell was calibrated with Helium, and experimental work to characterise the setup with Nitrogen was initiated. The uncertainty of multiple runs in Helium was consistently below 0.02% when compared to Ortiz-Vega et al.’s EOS as implemented in REFPROP v10. The thermophysics and thermodynamics teams from ICL and SINTEF, respectively, will continue to collaborate in the near future; stay tuned!
The research visit
The visit was a very enriching experience. Besides the valuable experimental work, the highlight of the stay was the in-person knowledge sharing with such valuable collaborators, which will undoubtedly lead to very fruitful common work.
The mobility initiative enabled competence building within ultrasonic flow measurements. In this case, the practical experimental work and insight into the Thermophysics group’s research facilities and activities were particularly appreciated. There is no substitute for being tutored by such a prominent and knowledgeable figure like Professor Trusler, and discussions and direct collaborations with researchers within his group have enriched our research strategies and spawned new ideas.
For more details of the Speed of Sound expertise at ICL and SINTEF, see the references below:
- Arellano, N. J. Mollo, S. W. Løvseth, H. G. J. Stang and G. Bottino, Characterization of an Ultrasonic Flowmeter for Liquid and Dense Phase Carbon Dioxide Under Static Conditions, IEEE Sensors Journal, vol. 22, no. 14, pp. 14601-14609, 15 July15, 2022, DOI: 10.1109/JSEN.2022.3180075
- -W. Lin and J. P. M. Trusler, Speed of Sound in (Carbon Dioxide + Propane) and Derived Sound Speed of Pure Carbon Dioxide at Temperatures between (248 and 373) K and at Pressures up to 200 MPa. Journal of Chemical & Engineering Data 2014 59 (12), 4099-4109 DOI: 10.1021/je5007407
- T-T-G Nguyen, C. Wedler, S. Pohl, D. Penn, R. Span, J.P.M. Trusler, M. Thol, Experimental speed-of-sound data and a fundamental equation of state for normal hydrogen optimized for flow measurements. The Journal of Chemical Thermodynamics, vol 198, 2024, 107341, ISSN 0021-9614, DOI: 10.1016/j.jct.2024.107341.
- C Wedler and J. P.M. Trusler, Speed of Sound Measurements in Helium at Pressures from 15 to 100 MPa and Temperatures from 273 to 373 K, Journal of Chemical & Engineering Data 2023 68 (6), 1305-1312 DOI: 10.1021/acs.jced.3c00083
Comments
No comments yet. Be the first to comment!