A SHIP system provides renewable solar heat to an industrial process by converting solar heat directly into usable heat. Earlier this year, SINTEF Energy Research joined the EU-funded project FRIENDSHIP to break down some of the major barriers to wider SHIP implementation. The aim is to develop more cost-effective solutions for industrial sectors including textiles, plastics, wood, metals, and chemistry, and to increase awareness of the benefits.
The problems with industrial heating processes today
Heating systems in industrial processes, transport and buildings are extraordinarily carbon-intensive and highly polluting. Fossil fuels account for by far the largest share of the heat generation, covering 85% of the heat demand in 2017. In the same year, only 5% of the total heat production came from renewable sources such as geothermal, solar heat, and biofuels.
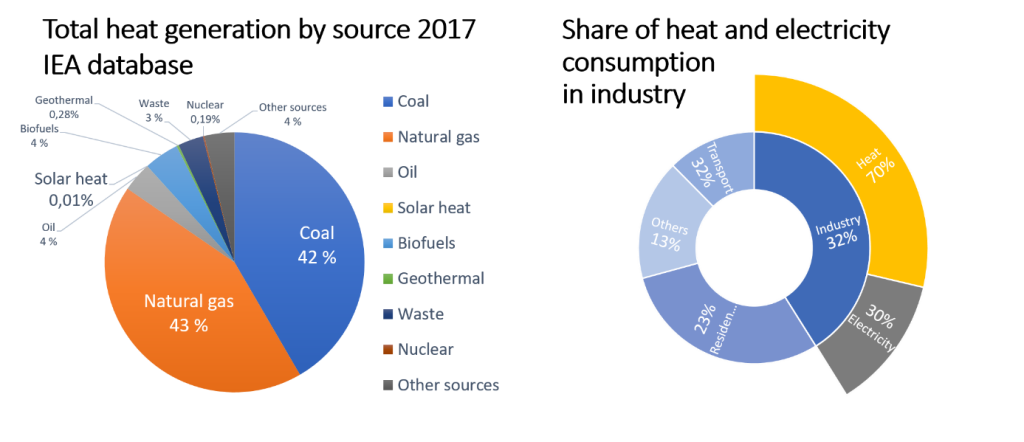
Industrial energy consumption covers a significant fraction (about 30%) of the total energy demand in the world. Heating accounts for about ¾ of this energy consumption, consequently much of fossil fuels consumption for heating is caused by industry.
To achieve the goals set in the Paris agreement and fight global warming, we need to decarbonize our industries quickly. This demands for heat supply that is both efficient and environmentally friendly.
Heating based on renewable solar energy is a promising alternative to fossil fuel heating. However, solar heat is still a largely untapped resource in industry. In fact, on a world basis solar heating accounts for close to zero percent of the renewable heat generation6. On the other hand, electricity generation using solar photovoltaic (PV) panels (“crystalline Si cells”) is much more common and accounts for a significant fraction of renewable electricity supply7. PV panels can in principle be used to provide process heating, but solar energy can be converted much more efficiently into usable heat with solar collectors (roughly 15-20 % efficiency using PV panels for process heating2 vs. about 70-80 % efficiency using solar collectors for process heating3).
What is SHIP and the role of solar collectors?
SHIP is an acronym for Solar Heat for Industrial Processes. A SHIP system provides renewable solar heat to an industrial process by converting solar heat directly into usable heat. SHIP is an up-and-coming solution, though for the moment it still represents a small part of the sales in the solar heat sector in Europe. Most of the solar heat systems in use today are related to low-temperature demand in building to provide hot water and space heating.
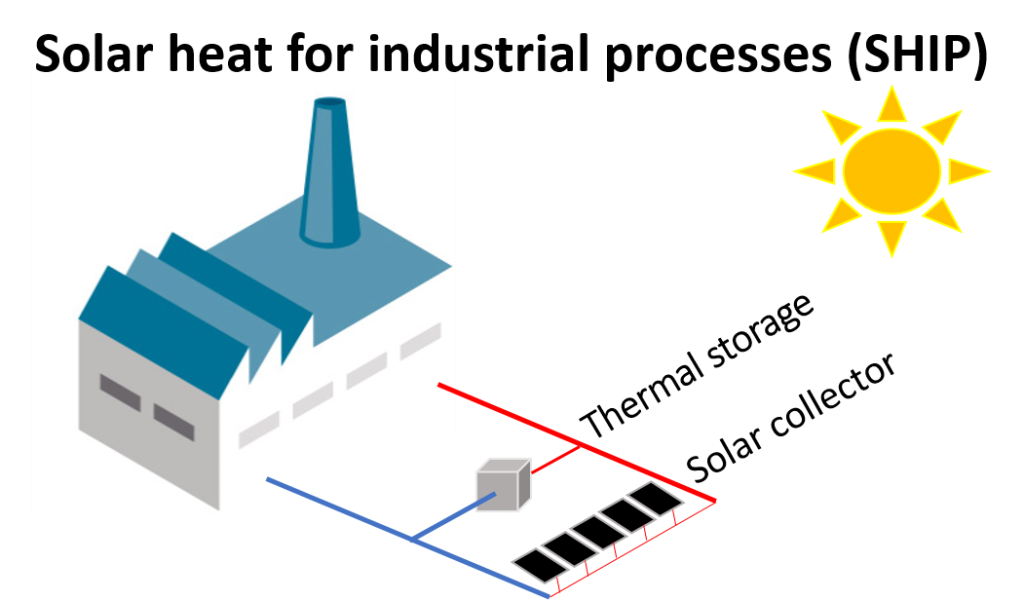
The basic principle of SHIP solutions is as follows (see Figure 2): i) solar radiation is collected with a solar collector, ii) the collected heat is transferred to a heat-transfer fluid and iii) the heated fluid is used to transfer energy to an industrial production process. A heat storage unit could be included to store heat in periods of surplus energy and use the energy when solar radiation is low.
Most of the solar-heat systems implemented today supply relatively low-temperature heat to buildings, providing hot water heating and/or building heating. As mentioned, solar heat is rarely used for industrial processes heating, but one area where solar heat has started to become relevant is the Agro-Food industry. In this industry, solar heat is used for drying or sterilization and supplies heat up to 140°C. In fact, such installations have already demonstrated that SHIP technologies can be competitive. Thus, SHIP solutions can likely be competitive also for other industrial processes that require medium temperature heating (140-400oC), such as in the textile, chemical, wood, and metal industries. However, we need to develop new SHIP solutions for efficient and reliable heat supply up to and above 200oC, which is currently limited.
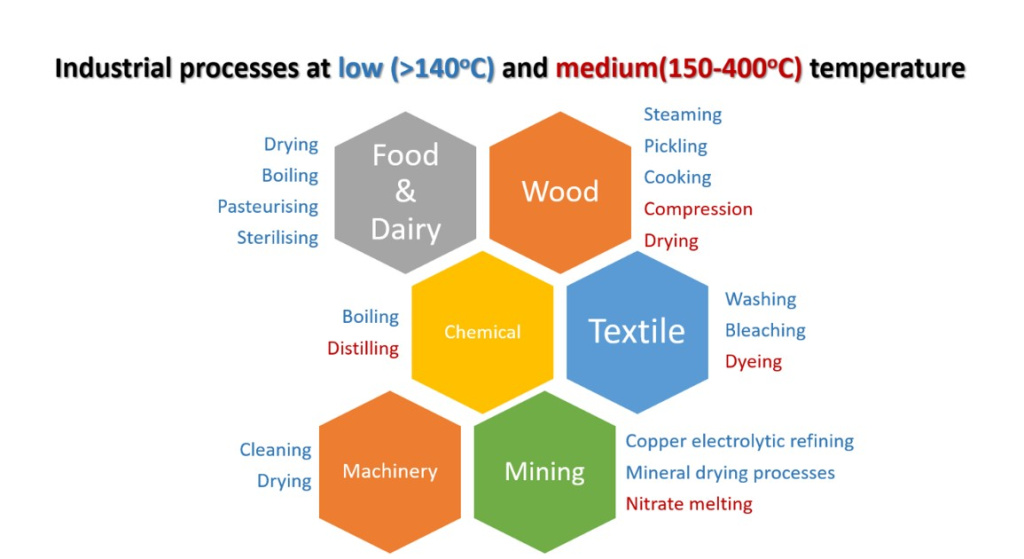
Heat at low temperature can be provided by commercially available systems, such as flat plate collectors (FPC) and evacuated-tube collectors (ETC). For medium-temperature processes, solar concentrators like parabolic-trough collectors (PTC) and linear Fresnel collectors (LFC) can generate temperatures up to 250oC.4
The largest barriers to the development and use of solar heat in industrial processes are the high upfront investment and low awareness of the SHIP technology. 70% of the SHIP suppliers agree that SHIP is already competitive in many markets, but it is not well known to costumers.5
”The acute lack of awareness about how solar heat can be a reliable and economically feasible option for high-temperature supply can be addressed by pioneering efforts and showcase projects” — Bhoovarhan Thirumala, CEO of Aspiration Energy, India1
In addition, higher acceptance and deployment of SHIP technologies will rely on these four pillars:
FRIENDSHIP, what is unique in our system?
Since May 2020, SINTEF Energy Research has been part of a project funded by Horizon 2020 called FRIENDSHIP (Forthcoming Research and Industry for European and National Development of SHIP).
The FRIENDSHIP project will attempt to break down some of the major barriers to SHIP implementation. Firstly, by developing more cost effective and reliable SHIP solutions to meet the heat requirements in industrial sectors like textile, plastics, wood, metal, and chemistry. And secondly by increasing awareness through active communication to the research community and potentiaxl customers.
FRIENDSHIP will not only perform theoretical research, but also develop a lab demonstrator of a SHIP system that pushes the boundary of current state-of-the-art solutions. FRIENDSHIP will aim at superior performance by incorporating several new improvements and functions to the standards SHIP solution, including:
- Low-cost solar collectors combined with selective coatings that improve absorbance of the heat radiation and nanoparticles that improve heat transfer properties of the heat-transfer fluid.
- An advanced high-temperature heat pump that enables continuous and stable heat supply targeting temperatures between 180 and 250o.
- A high-density thermal storage that allows, in a single component, storage of heat from the solar collector as well as production- and storage of steam for process use, yielding a better process integrability.
- A “cooler” that enables cold production from the residual high-temperature heat, either by using an absorption- or ejector chiller. In this way, the SHIP system can provide both heating and cooling loads required by the industry.
- Advanced control management supported by reliability studies at engineering and process level, which will allow the enhancement of the quality and availability of the expected heat to match the process demand.
FRIENDSHIP partners strongly believe that these developments will contribute towards increasing the share of renewables in industry by enabling a system that is more reliable, energy- and cost efficient than conventional SHIP solutions. At SINTEF, we focus ondeveloping new technologies:
Heat pump for continuous, stable, and high-temperature heating
Our main task in FRIENDSHIP is to develop heat pump solutions that increase the temperature, availability and stability of the supplied heat. Without a heat pump, the temperature of the delivered heat would primarily be determined by the intensity of the solar radiation, which does not always enable high enough heating temperatures. With the integration of a heat pump, on the other hand, we achieve a much higher flexibility in the supplied heating temperature, thereby eliminating the need for backup heating solutions based on non-renewable energy. The heat pump also assists the thermal energy storage in increasing the availability of the heat, enabling round-the-clock heat delivery, even at times when there is no solar radiation.
In addition to theoretical research, we will develop a new, state-of-the art steam heat-pump compressor that enables efficient heat delivery at temperatures of about 180-200°C. Steam is a viable refrigerant for high temperature heat pumps, in addition to being non-toxic, non-flammable, environmentally friendly and basically free of charge. SINTEF will continue the research on turbo compressors, frequently used in the automotive industry, as they are generally more compact and cost effective, but require retrofitting and research to meet the project goals.
The compressors will be tested in our laboratories to demonstrate successful operation and performance under relevant conditions. As of now, no one has developed steam compressors with such high delivery temperatures, and our efforts are therefore essential in the development of solar energy solutions that can deliver stable and high-temperature heating.
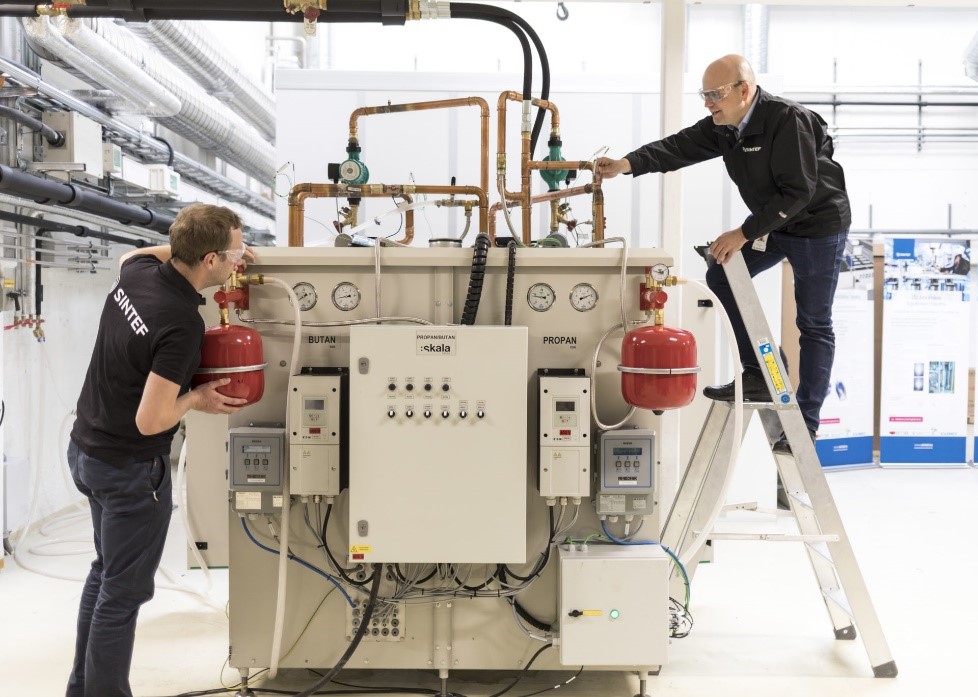
Nanofluids to improve heat transfer properties
By adding nanoparticles to heat-transfer fluids, one may achieve a significant improvement of the heat-transfer properties. This has been the topic of several previous activities at SINTEF, including NanoHX and FerroCool. The effect on heat transfer properties is mainly due to increased volumetric heat capacity and heat conduction of metallic particles dispersed throughout the base heat-transfer fluid. In addition, nanoparticles may be used to improve the heat absorption in the collector part. Combined, it is hoped that we may achieve an improvement to the heat-transfer properties of between 10-40%.
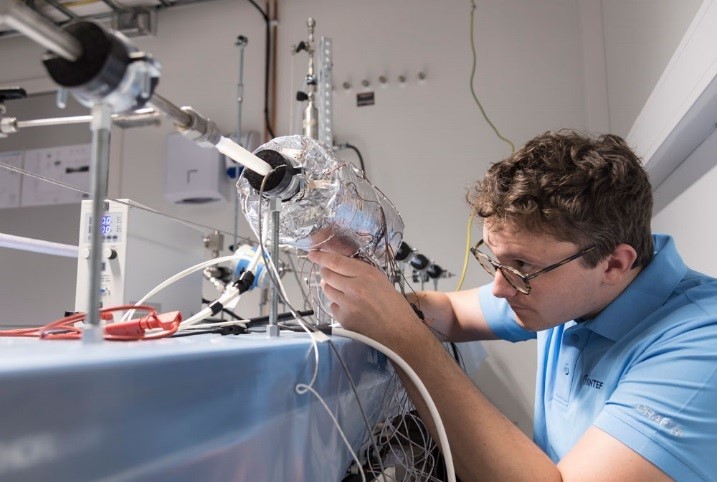
Efficient ‘cooler’ integrated into the system
Many people do not realise it is possible to use high-temperature solar heat to provide process cooling below 0°C. By implementing cooling technologies into our SHIP system, the system will be able to meet both heating and cooling demands at industrial plants.
The available technologies on the market for thermally driven cooling systems are absorption and adsorption chillers, solid and liquid desiccant cooling systems, and ejector refrigeration cycles. Of these, absorption chillers are considered as the most desirable method for harnessing solar thermal energy due to their relative maturity, reliability, and higher efficiency. In addition, absorption chillers will take advantage of economies of scale in large equipment to obtain a relatively good levelized cost of cooling as compared to other thermally driven systems.
The French research organization CEA will develop an absorption chiller for cold production in the SHIP system. CEA has more than ten-year’ experience in developing absorption chiller using NH3/H2O as working fluid. The thermodynamic cycle of NH3/H2O machines will work at high pressure, preventing air penetration. This is also favourable to the optimization of the internal transfers of heat and mass, to the reduction of the quantity of fluid, to the limitation of the hydraulic pressure drops and in fine to a design of a compact machine. The refrigerant, here NH3, enables the negative cold production since it freezes at -77,7°C. For FRIENDSHIP, to boost the performance, a new technology of absorption chiller will be developed based on GAX (Generator Absorber heat eXchange) cycle. A prototype will be tested in laboratory test rig; and later integrated into the system of FRIENDSHIP’s demonstrator.
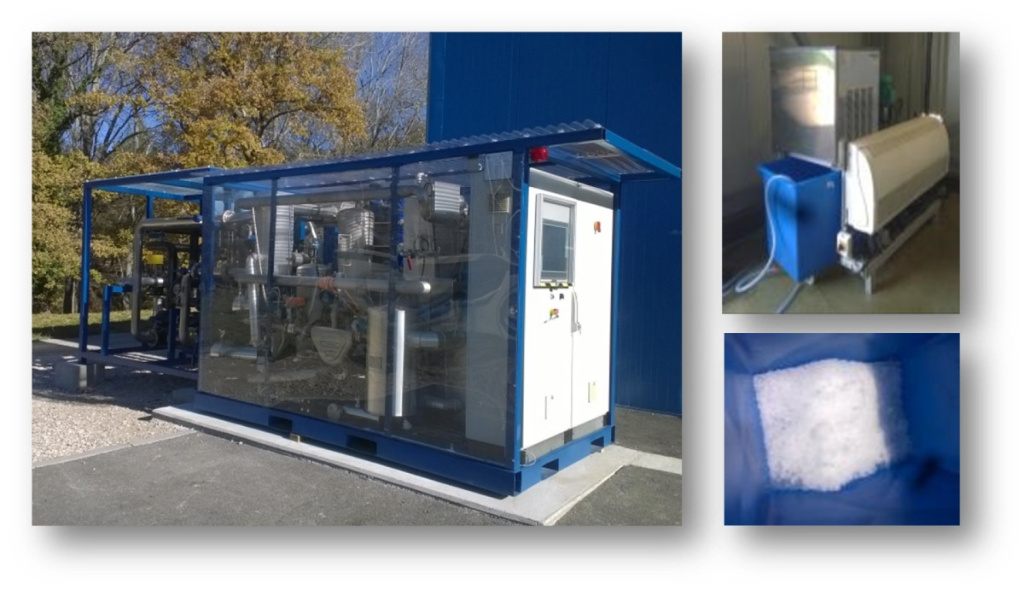
The FRIENDSHIP consortium is composed of several different participants to contribute to each step of the value chain of the SHIP technology. AMIRES is the coordinator support and dissemination leader. ABSOLICON and INDUSTRIAL SOLAR are the solar collector technological providers. National Institute of Chemistry, CEA (project coordinator) and SINTEF will contribute to conceptual and lab facility developments. CLARIANT and SONAEMC will be the potential end user for the technologies that FRIENDSHIP will develop. INES is charge of the training, promotion and stakeholder’s involvement. RINA will study how to better integrate and promote the integration of FRIENDSHIP solutions in industry from a technical/economical/regulatory point.
This project has received funding from the European Union’s Horizon 2020 research and innovation programme under grant agreement No 884213.
Authors: Elvia Chavez (SINTEF), Monika Nikolaisen (SINTEF), Karl Yngve Lervåg (SINTEF), Hai Phan (CEA, France)
Reviewers: Francesco Finotti (SINTEF), Espen Halvorsen Verpe (SINTEF), Fabrizio Perrota (AMIRES), Valery VUILLERME (CEA, France)
References
- Aspiration Energy. https://aspirationenergy.com/.
- Best Research-Cell Efficiency Chart. https://www.nrel.gov/pv/cell-efficiency.html.
- Alghoul, M. A., Sulaiman, M. Y., Azmi, B. Z. & Wahab, M. abd. Review of materials for solar thermal collectors. Anti-Corrosion Methods Mater. 52, 199–206 (2005).
- IEA-ETSAP & IRENA. Solar heat for industrial processes -Technology Brief. 37 (2015).
- Solar Payback project. https://www.solar-payback.com/.
- https://www.iea.org/data-and-statistics?country=WORLD&fuel=Renewables%20and%20waste&indicator=Heat%20generation%20from%20renewables%20and%20waste%20by%20source
- https://www.iea.org/data-and-statistics?country=WORLD&fuel=Energy%20supply&indicator=Renewable%20electricity%20generation%20by%20source%20(non-combustible)
Comments
Thank you for advocating for cleaner, more efficient technologies and for promoting eco-friendly practices in industries. Your blog is a source of inspiration for businesses looking to embrace solar solutions for a better and more sustainable future.
Yes, using solar power has many advantages over using electricity: it’s a renewable source, and the extraction of this type of energy has less impact on the environment. Thank you for sharing such an informative article!