Today, ammonia is perhaps best known as a foul-smelling chemical used in cleaning products. In the future, it might also be widely used as a maritime fuel! At SINTEF, researchers are working towards this to happen through a wide variety of projects.
What is ammonia?
Ammonia is the second most traded chemical product globally, and is primarily used as fertilizer in the agriculture industry. It is also used in the production of various industrial chemicals and in refrigeration systems, for example, on board fishing boats.
The ammonia industry has over a century of experience in producing, storing, handling, and transporting ammonia.
Chemically, ammonia (NH3) consists of three hydrogen (H) atoms and one nitrogen (N) atom. Since ammonia does not contain carbon, it cannot produce carbon dioxide (CO2). Given the current need for decarbonisation, this makes ammonia a very interesting potential fuel source.
Ammonia and hydrogen
Ammonia is produced from hydrogen in two steps. First, hydrogen is produced from either fossil or renewable sources. The hydrogen is then combined with nitrogen, which is extracted from the air, to form ammonia.
However, ammonia is not always the best fuel to use, and it is sometimes better to convert part of it back to hydrogen. Why? Because ammonia is much easier to transport and store, while hydrogen has better fuel properties. In other words, ammonia can be used as either a primary fuel or as an energy carrier for hydrogen, and is therefore an important contributor to the hydrogen value chain and economy.
Both hydrogen and ammonia are focuses of HYDROGENi: an environment-friendly energy research centre led by SINTEF, dedicated to meeting the 2030 and 2050 goals of the Norwegian hydrogen roadmap.
What is the difference between grey, blue and green ammonia?
Both hydrogen and ammonia are often described as grey, blue or green; this has nothing to do with the colour of the product, but instead indicates the climate friendliness of the production process.
Today, almost all hydrogen is generated from fossil fuels, mostly natural gas. This grey production is made in a process called steam reforming, where natural gas and heated water (steam) is combined to form hydrogen and CO2. Ammonia is then formed using the “Haber-Bosch process”, which is a catalytic reaction of hydrogen and nitrogen at a high pressure and temperatures up to 500°C. Both steps are very energy intense, but most of the energy usage, and practically all of the direct CO2 emissions, are related to hydrogen production. Therefore, there are a lot of incentives to find more sustainable production processes – the blue and green ones.
In blue production, hydrogen is produced from natural gas using the same process as grey hydrogen. However, the resulting CO2 emissions are captured and not released into the atmosphere. This carbon capture and storage (CCS) technology is also relevant for many other industrial processes, and Norway is at the forefront of its development, for example, through the Norwegian CCS Research Centre, spearheaded by SINTEF.
In green production, only renewable energy sources are used to produce hydrogen. Green hydrogen is produced through electrolysis, wherein renewable electricity (such as wind or solar power) is used to convert water – instead of natural gas – into hydrogen and oxygen. The energy required for converting the green hydrogen into green ammonia must of course also be renewable.

Ammonia producers have recently started work to replace grey ammonia. For example, Yara has recently established the Yara Clean Ammonia unit, which is working to produce both green and blue ammonia. Blue ammonia can be produced in their existing facilities, if complemented with CCS. To produce green ammonia large electrolysers are needed, as can be seen at the 24 MW pilot installation at Herøya, requiring significant investments. A successful ammonia and hydrogen transition therefore relies on blue production in the short- to medium-term, with green production as a long-term goal.
Can ammonia be produced without hydrogen?
There are some innovative green methods under development for producing ammonia without hydrogen, including “electrochemical cell” technology, which converts renewable electricity, water and air directly into ammonia without needing a separate hydrogen electrolysis process. These technologies are currently too slow and energy intensive, but they could be promising in a longer perspective.
Why ammonia as maritime fuel?
Even though its use for energy generation is currently limited, ammonia has a “fuel history”. In 1933, Norsk Hydro launched their Ammonia Truck. During World War II, some countries used ammonia to keep public transportation in operation, as there was a shortage of oil fuels. In 1962, NASA used it as fuel in their X-15 rocket. However, despite this history, limited research has been conducted on ammonia as a fuel.
Recently, ammonia has gained a lot of interest from the shipping industry as a replacement for conventional diesel oils. Today, many ships are being built to use liquefied natural gas (LNG) as fuel, which reduces carbon emissions by approximately 20% compared to diesel. However, if we are to reach our climate targets, zero-carbon fuels must be established. Several alternative fuels are on the agenda, including ammonia and hydrogen.
Ammonia is easier to store on board a ship
All alternative fuel solutions will take up more space on board compared to diesel. This means that there will be less space available for cargo and/or passengers. Even though approximately twice as much space is required for storing ammonia compared to diesel, it has a higher volumetric energy density than most other zero-carbon fuels. This makes it especially interesting for long distance shipping, which requires large quantities of fuel to be stored onboard.
A gas requires far more storage space than a liquid, which is why a maritime fuel is stored in liquid form even though it is used as in gas form. Liquid hydrogen and LNG are stored in cryogenic conditions at -253 °C and -160 °C respectively. The thermal management of such a storage system is very demanding. However, storing ammonia is much easier. It can either be stored at ambient pressure at -33 °C (so called refrigerated storage) or at ambient temperature in a pressurised tank at 10 bar.
Furthermore, even though one cubic meter of ammonia weighs more than hydrogen, ammonia arguably does a better job of storing hydrogen than hydrogen itself; one cubic meter of liquid ammonia contains fifty per cent more energy than the same volume of liquid hydrogen.
Is ammonia an environmentally friendly fuel?
Ammonia is an environmentally friendly fuel if it has been produced in an environmentally friendly way. A conventional marine diesel engine emits large amounts of CO2 as well as harmful air polluters like sulphur oxides, nitrogen oxides and particles. Using ammonia not only eliminates CO2 emissions, but also sulphur oxides and particles emissions.
One concern often raised is the increased nitrogen compounds emitted. While this is not a real issue for fuel cells, it can be problematic for ammonia-fuelled engines. If the combustion process isn’t well managed, it can release large amounts of nitric oxides (NOx) and nitrous oxide (N2O), which is a much stronger greenhouse gas than CO2. Therefore, if ammonia is to be an environmentally friendly fuel, the engine technologies must be able to minimise the formation of undesired combustion products, and the existing exhaust gas treatment technologies must be capable of handling the leftover amounts of nitric oxides and nitrous oxide.
Is ammonia expensive?
Since the transition from grey ammonia has just started, the costs of green and blue ammonia are relatively high. Nevertheless, green ammonia is considered by many to be the cheapest fuel in decarbonising EU-related shipping towards 2050, with the production cost being likely to decrease in the future.
What about ammonia as fuel in other sectors?
Ammonia can also play an important role as fuel in other sectors For example, ammonia as a fuel can contribute to the decarbonisation of the offshore oil and gas industry. Operating an offshore platform is very energy demanding. Today, most of this energy is generated by gas turbines fuelled by natural gas. However, not to all these platforms can be electrified, due to cost and other constraints. In the research centre LowEmission, we work on finding other carbon-free alternatives for offshore installations. This includes fuel cells operating with hydrogen and/or ammonia, as well as new concepts for using hydrogen- and ammonia-fired gas turbines. In 2023, SINTEF will start another project on this topic: Decomposed ammonia for carbon-free power generation (DECAMMP).
How can ammonia be used as a maritime fuel?
Right now, no ship is fuelled by ammonia. But this can soon change.
There are two principle technologies for using ammonia as fuel: either burning it in a combustion engine (or gas turbine), or converting it directly to electricity in a fuel cell. None of these technologies are commercially available for ammonia yet, but a lot of R&D work is currently underway. The first commercial marine ammonia-fuelled engines are reported to become available in 2024, initially as flexible multi-fuel engines but pure ammonia engines are also expected to be developed in the future. The same year, a 2-MW ammonia fuel cell system will be demonstrated on board a Norwegian offshore vessel. Both solutions come with their pros and cons.
Another “choice” to be made is whether to use pure ammonia fuel, or use it together with another fuel (for example hydrogen), or use it as an energy carrier, i.e., cracking it back to hydrogen fuel.
Ammonia for combustion engines
Compared to other combustion fuels, such as LNG and hydrogen, ammonia is hard to ignite, and burns slowly. From a safety perspective, this is positive, as it reduces the risk of fire and explosions. However, the poor combustion properties make using ammonia as the sole fuel source challenging. Several manufacturers are working on various solutions to obtain a stable and efficient ammonia-fuel operation. The most common approach is to use it together with another fuel.
Engines that aim to operate primarily on ammonia still require diesel as a “pilot fuel” to ignite the main charge. Flexible, multi-fuel engines are also being developed, such as in the AMAZE project, which aims to both use carbon-free ammonia as the primary fuel and be able to switch seamlessly from ammonia to diesel or biofuels.
Another solution could be to add some hydrogen to the ammonia fuel, simply because it is much easier to burn. This can be done by partially cracking the ammonia into hydrogen and nitrogen just before it enters the engine. If we can achieve a mixture with combustion properties very close to those of standard fuels, then we would be able to retrofit existing engines as well as install new ones. SINTEF is developing and using advanced numerical models to make detailed simulations of the combustion process. This will help engine producers to design engines that are more efficient and with lower emissions.

Onboard cracking requires heat. All combustion engines produce excess heat through the exhaust gases that could be utilised for this purpose. However, for certain ships, the excess heat is required for other purposes on board. An alternative approach could then be to increase the reactivity of the ammonia combustion process by utilising oxygen-enriched air instead of normal air. In the project NanoIgnite, NTNU and SINTEF are working with an innovative solution for igniting ammonia, removing the need for a pilot fuel. In addition, the Green Platform project, LINCCS, considers the potential for chemical ignition of ammonia using hydrogen peroxide.
Ammonia for fuel cells
Fuel cells is another area of expertise at SINTEF, and one of the most efficient technologies for converting a fuel into electricity. They produce less noise and require less space than combustion engines but are currently more expensive. Using ammonia in fuel cells also presents challenges.
The most promising fuel cell types for the maritime sector are low-temperature proton exchange membrane (PEM) fuel cells and high-temperature solid oxide fuel cells (SOFC).
Hydrogen-fuelled PEMs are already used for heavy-duty road transport. Maritime application is still limited to some demonstration installations, but more and more manufacturers are launching systems specifically designed for the maritime sector.
Ammonia cannot be used directly in PEM fuel cells – it has to be converted back to hydrogen. Since the tolerance for ammonia in current PEM technology is extremely low, highly efficient crackers, or other separation processes, must be developed.
Ammonia can be used directly as fuel in an SOFC. While the ammonia must still be cracked to hydrogen, this can be done inside the fuel cell due to its high operating temperature. This high operating temperature also means that the SOFC generates a high-quality heat, which can be utilised for heating purposes on board. One challenge with the high temperature is the fuel cell degradation, which results in uncertainties about their long-term durability. SINTEF are performing experimental tests in our new NH3 lab in order to gain more knowledge on how ammonia influences the degradation mechanism.
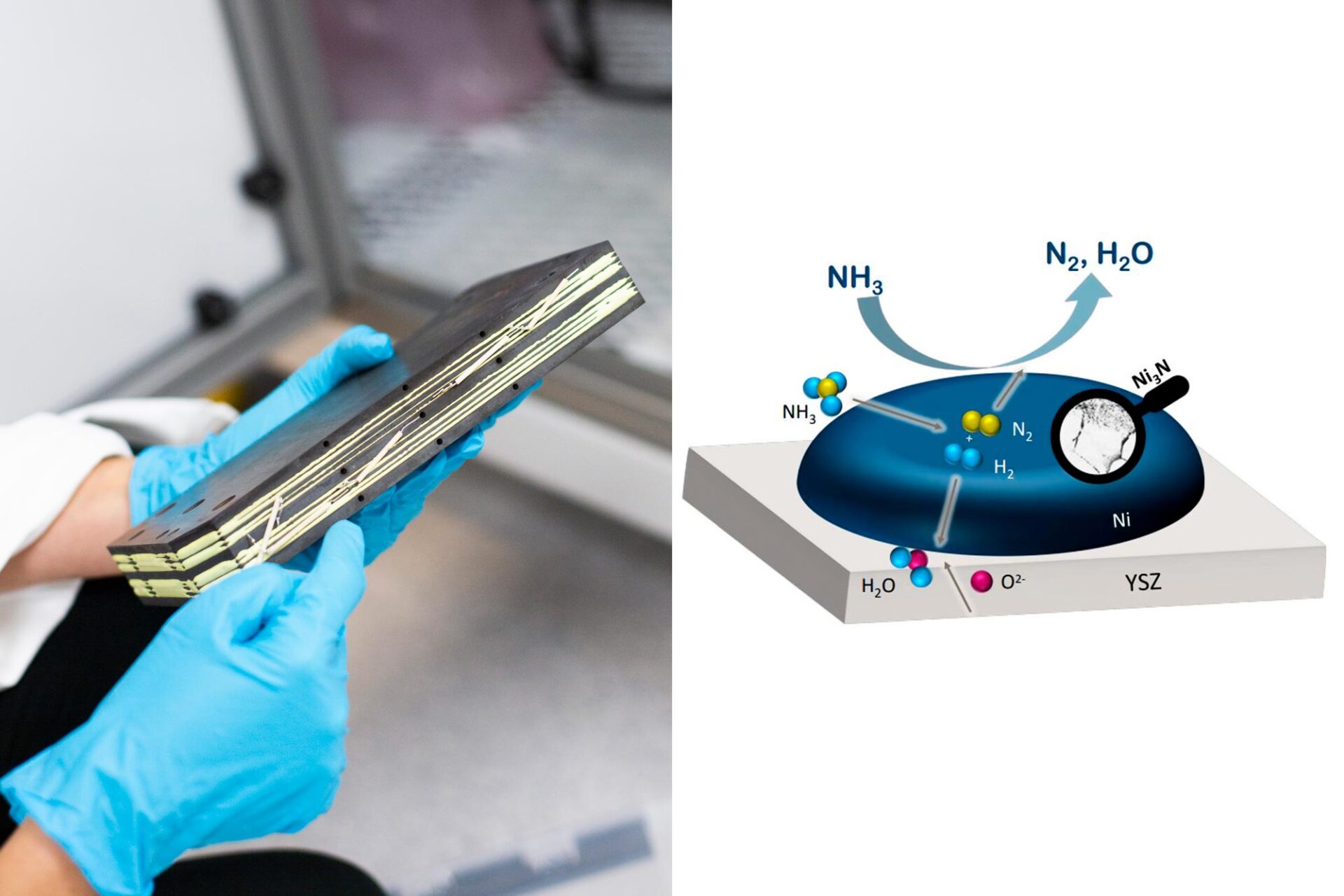
The project Aegir evaluates a concept that combines the two fuel cell technologies. First, ammonia is split into hydrogen and nitrogen in the high-temperature SOFC. The hydrogen is then separated using an advanced membrane that only lets hydrogen molecules through. This results in a very clean hydrogen fuel that can be used in a PEM fuel cell.
How is it distributed and delivered to the ship?
Ammonia can be transported by road, railway, ship or pipelines. Since it is a widely traded product, supply chains have already been established in the proximity of ports, and over 120 ports around the world have facilities to import and export ammonia. This existing port infrastructure is a good starting point for ammonia’s use as a fuel, but it is not enough. More flexible solutions are required in the transition period while only a limited number of ships are using ammonia.
One option is to build small ammonia tanker ships that act as ship-to-ship bunkering vessels, like the ones that already exist for LNG. This means that the bunkering does not have to happen in port. Yet another option is already being developed in the Ammonia Fuel Bunkering Network project, which is constructing a flexible barge capable of receiving ammonia in various forms from storage tanks, trucks, ships and trains. Azane Fuel Solution is responsible for developing the barge, while Yara will supply green or blue hydrogen. HYEX Safety will ensure that this is all done in a safe way, while Ocean Hyway Cluster will help spread the news. The first demonstration is planned to take place at Saga Fjordbase in 2024.
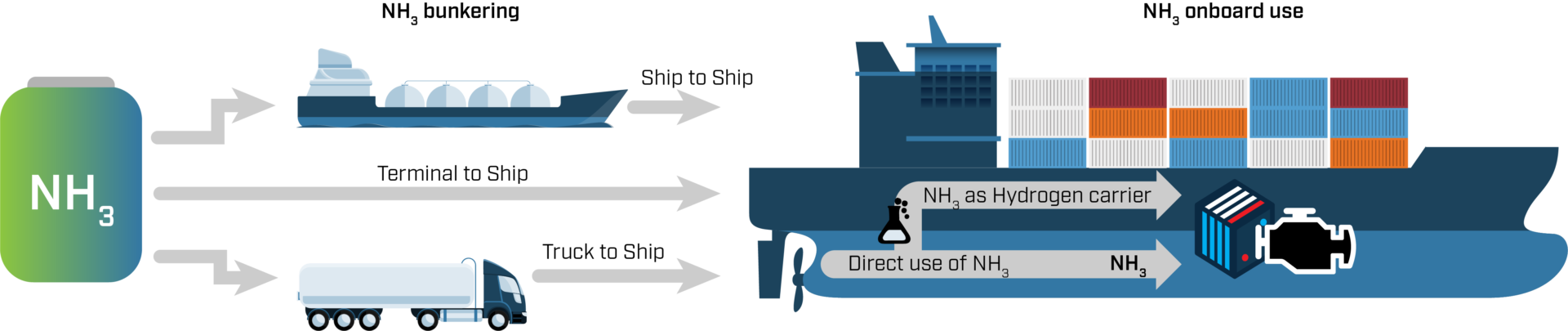
Is ammonia dangerous?
As most other fuels, ammonia can be dangerous if not handled correctly. Ammonia is classified as toxic and flammable. However, we already have some experience of handling ammonia on board ships, both as cargo on ammonia tankers, and as refrigerants in reefers and fishing vessels for keeping the cargo cold.
Ammonia is less flammable than hydrogen and LNG
When discussing the risks associated with fire or explosions, the following three fuel properties are important:
- Flammability range, which is the concentration range of a fuel-and-air mixture that can burn. For hydrogen, this is between 4-74%, which is far greater than for ammonia and LNG (natural gas). Ammonia can only burn if the gas concentration is between 15-28%, while natural gas can start to burn at a lower concentration: 5-15%.
- Autoignition temperature, which is the lowest temperature at which a flammable fuel mixture can spontaneously ignite without an external flame or spark. Therefore, a high autoignition temperature means a lower risk. For ammonia, this is 650°C, while for natural gas and hydrogen, it is 540°C and 500°
- Flame velocity, which indicates how fast it burns. Ammonia burns around 50 times slower than hydrogen, and 7 times slower than natural gas.
All this means that using ammonia comes with a significantly lower risk of fire and explosions than both hydrogen and natural gas. However, the risk is not negligible.
Ammonia is toxic
The odour of ammonia is easily detected at very low concentrations in air (5-20 ppm). This is often considered to be the main barrier for public acceptance, as people find even small leakages unpleasant. However, for the ship’s crew, it acts as an early warning of a leak, which can be handled before it becomes dangerous. Severe irritation occurs above 400 ppm, and above 2000 ppm may be fatal. In comparison, ammonia does not become flammable until 150,000 ppm, and hydrogen presents a fire/explosion risk at 40,000 ppm. This means that the toxicity presents an additional challenge, since any leak must be prevented at lower concentrations than would be needed before it became a fire risk.
The introduction of ammonia as a maritime fuel is considered to be more suitable for ships with no passengers. It is expected that the first use of ammonia as fuel will be on cargo ships, where the crew has solid experience with handling dangerous products. As we gain more experience and evidence of ammonia being a safe fuel, the market will be able to expand, which is what happened when LNG was introduced as maritime fuel. In the beginning, it was solely used on gas tankers carrying LNG as cargo. Today it is used on cruise ships carrying thousands of passengers.
What happens if liquid ammonia is spilled?
An accidental or controlled release of a flammable and/or toxic substance is always associated with risk to both personnel, equipment and environment. Preventing theses hazards requires a sound understanding of how the substance behaves upon a leakage. The boiling point of ammonia is -33°C, and as soon as liquid ammonia is released, it will start to boil, forming ammonia gas. Generally, it can be said that a leakage from refrigerated ammonia (at ambient pressure) are associated with lower risks compared to a leakage of “warm” ammonia (at high pressure).
Since ammonia gas is lighter than air, vapor from a liquid pool will rise in the atmosphere. Wind and buoyancy are the main factors determining the spread of the toxic gas. When cold ammonia gas meets humid air, it leads to fog formation. Since ammonia is very hygroscopic, meaning it readily binds to water, the fog droplets may contain a mixture of water and ammonia. The possible effect that this can have on how ammonia disperses in air, is still an open research topic.

Ammonia dissolves easily in water. Although spilling ammonia into water may in some cases be preferable from a safety point of view, it will have a negative impact on the environment, as ammonia dissolved in water is highly toxic to aquatic life. Spilling liquid ammonia on water will lead to a significant portion of it evaporating at a rapid rate (typically 30%), which can pose a larger safety risk than other ways of handling the potential spill.
Are there any regulations in place?
The International Maritime Organisation (IMO) maintains the regulatory framework for safety, security and environmental performance of international shipping. Classifications societies, such as Det Norske Veritas (DNV), also play an important role in developing both technical requirements and guidelines.
Even though ammonia is far less flammable than LNG and hydrogen, it is still considered a flammable fuel. The current IMO regulation covering flammable maritime fuels was developed for LNG. Regulations are in place for ammonia as cargo, but not for its use as a fuel.
How can we address the safety challenges related to ammonia?
All of these challenges can technically be solved. We have a lot of knowledge related to LNG spills, some of which can also be applied to ammonia. But ammonia behaves differently, particularly in a Nordic climate, and releases must be controlled at much lower concentrations. At SINTEF we develop comprehensive numerical models to simulate what happens during a leak, such as how quickly a liquid spill evaporates, and how the dispersion is affected by wind, temperature, and humidity. An important aspect is how the ammonia water droplets are formed in air, which we have previously investigated for other substances than ammonia.
These improved models will provide us with a better understanding of the conditions where a spill can pose a large/low risk. They also enable us to give advice on safety distances and effective spill handling measures for preventing hazardous situations and odour.
Developing a new regulation takes time
New IMO regulations are often developed alongside, and after, pioneer industry projects. When LNG was introduced as a maritime fuel, Norway was the pioneer. The IMO regulation followed many years after, based on experience from Norway. For pioneers who want to use novel technologies that are not yet covered by existing regulations, IMO offers a risk-based approval process called “Alternative Design Process”. Classification societies can help by giving pioneering technology an “Approval in Principle” (AIP). This is an independent assessment of a concept, which confirms that no obstacles would prevent the concept from being realised. The pioneering barge from the Ammonia Fuel Bunkering Network project has received such an AIP from DNV. This means that research and innovation projects can contribute to the development of new regulations.
How can we accelerate the use of ammonia as maritime fuel?
Ammonia can contribute significantly to the decarbonisation of the maritime sector as either a fuel or an energy-carrier for hydrogen-based fuels. However, in order for this potential to be fulfilled, there are several barriers that must be overcome. This presents as a classic “chicken-and-egg” dilemma:
- It is impossible to use new fuels without new ship technologies (engines, fuel cells) and infrastructure.
- However, technology for bunkering ammonia and using it on board will not be developed before ship owners place orders.
- Ship owners will remain sceptical until regulations are developed to address ammonia flammability and toxicity.
- Regulations will not be developed until ships and bunkering solutions are designed.
Therefore, a complete value chain for ammonia has to be established.
What will the future ammonia value chain look like?
A value chain includes all stages from production to end use. The present value chain for ammonia is strongly linked to its predominant use as a fertilizer. With the increased use of ammonia as a maritime fuel, new possibilities and bottlenecks in the value chain will likely arise. At SINTEF, we develop models for analysing and optimising emissions and costs in different types of energy value chains. For example, in CleanExport, models are built to exploit Norway’s potential for clean energy export, focusing on renewable electric power, hydrogen, and natural gas with CCS.
Since all development essentially needs to take place at the same time, corporation and coordination is essential for minimising risks and costs. The government-funded Green Platform Initiative aims to support these types of large collaboration projects by providing funding to enable enterprises and research initiatives to stimulate larger and more rapid investments in sustainable energy solutions. SINTEF takes part in several such projects, such as ZeroKyst, which is working to facilitate the use of hydrogen fuel by coastal fishing boats, and the above-mentioned LINCCS and Ammonia Fuel Bunkering Network.
The MaritimeNH3 project, led by SINTEF and associated with the Ammonia Fuel Bunkering Network project, focuses on the value chain for ammonia as maritime fuel in Norway. The project aims to fill knowledge gaps related to climate-friendly production, distribution, end-use technologies such as engines and fuel cells, and safety issues. If we are to fairly compare ammonia with other maritime fuels (hydrogen, biofuels, batteries), we must consider the whole value chain – alternatively expressed as “well-to-wake”. This is exactly what has been suggested in the new EU Maritime Fuel Initiative, which means that fuels will be assessed by its well-to-wake emissions.
ChemAnalyst Japan provides detailed price indexing and research on Ammonia: https://www.analystjapan.com/Pricing-data/ammonia-43