In LowEmission research centre, there are many undergoing research tasks on reducing the cost of electrification (SP3). Understanding the longevity of power cables is essential to support increased electrification efforts, as it allows for a stable and efficient supply of electricity to offshore facilities. Water treeing is a major aging mechanism in power cables. While progress has been made in understanding water tree growth, the initiation mechanism remains uncertain. Improved insights are crucial for developing efficient cables and supporting electrification on the NCS.
A little glimpse on cable history.
Since the 60s, extruded cross-linked polyethylene (XLPE) has been widely used in HV cables laid in wet environments [1]. Few years later, high failure rate was reported, which after further investigation found that the insulation breakdown was associated with the growth a tree-like water structure. The water structures were observed close to the breakdown channel, which suggested causality [2]. This was due to water diffusion into the insulation since XLPE is not water tight, which make water ingress into the insulation inevitable.
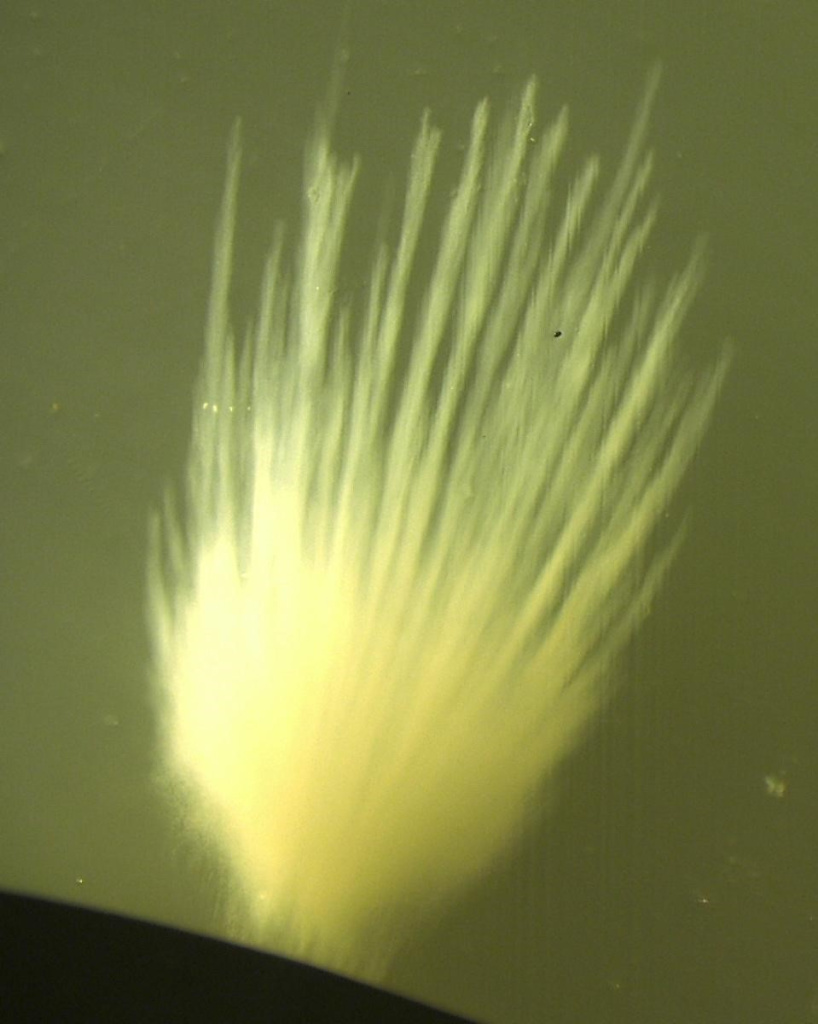
Numerous research work was conducted since the late 80s, which aimed to answer critical questions regarding this mechanism of cable degradation. A possible solution to limit this ageing was to introduce an additional layer of water barrier around the insulation system (commonly made of lead) to protect the insulation system from water. This is referred to as ‘Dry’ cable design. The downside of such a design is the additional weight and costs.
Deploying cables without a water barrier (wet design) in comparison to dry design provides: i) Lighter ii) Cheaper iii) Potentially less environmental constraints (in case lead is banned in the future). However, the absence of water barriers make the cable more susceptible to water treeing.
The water treeing initiation and growth mechanism are complex. In fact, it is difficult to categorize different operation factors if their contribution is either on water tree initiation or growth. Specially, when different factors can coincide. In this blog, we briefly go through two of the predominant theories concerning the initiation of water trees.
Water tree initiation mechanism
The exact path from having water presence within the insulation to the formation of tree-like structures is still vague. There are plenty of theories proposed of which, two are predominant: 1) Mechanical Damage Theory and 2) Stress Induced Electrochemical Degradation theory.
Mechanical damage theory explain that the inception of a water tree is due to having mechanically overstressed zones. It is presumed that mechanical and electric stresses can cause to the formation of voids and micro-cracks within the polymeric insulation. This damage can develop further into crazing as the water condenses within the voids and microcracks. The situation can be worsened with the presence of high electric field, which can enhance the diffusion of water and as a result increase the water content within crazing zones [4]. Furthermore, inhomogeneous field around crazes can occur due to the water having a much higher permittivity. This induces additional Maxwell stresses around the tip, which will facilitate further expansion of the crazed zones (see the figure 1 below).
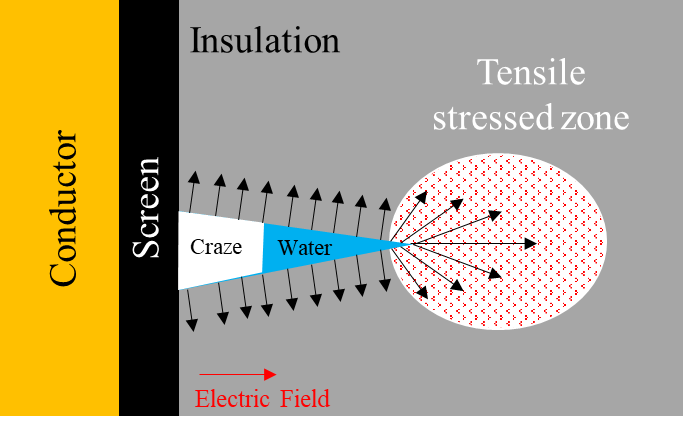
Stress Induced Electrochemical Degradation theory (SIED) is currently the predominant theory in the electrochemical school of thought for Al conductors. This is because the theory is entirely built around the corrosion of Al conductor being responsible for introducing potential inception sites within the conductor screen, leading to the growth of vented water trees from the inner conductor.
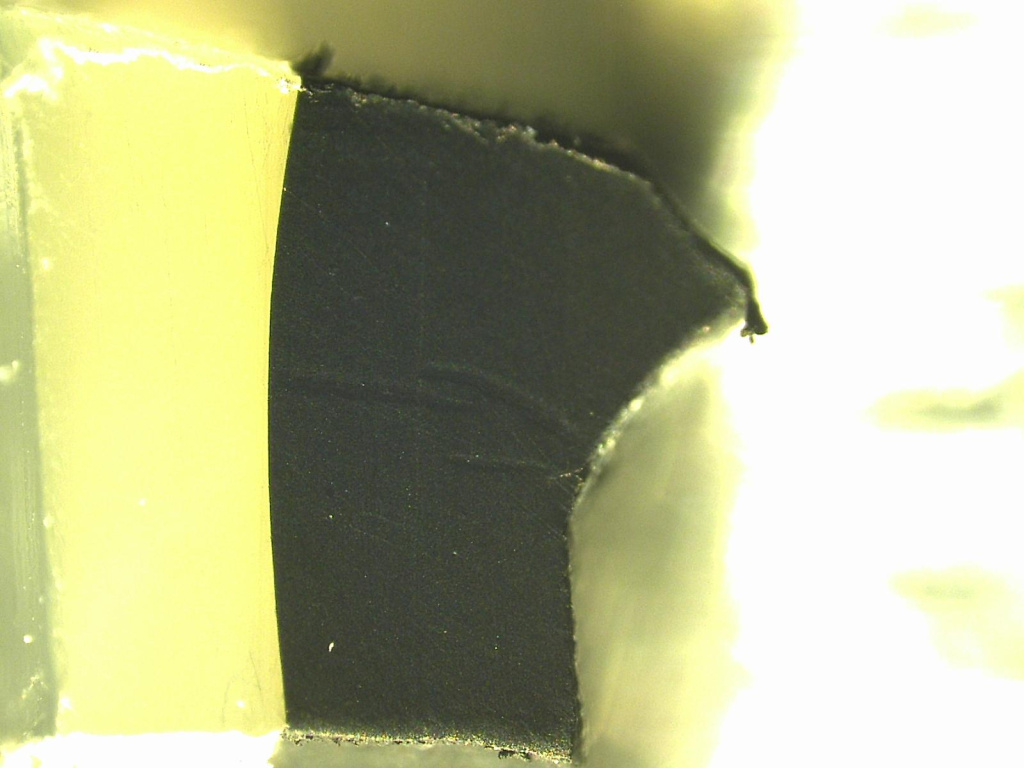
This phenomenon was first reported after observing structural changes near the root of vented water trees grown within accelerated aged test samples [5][6]. In follow-up study, the authors hypothesized that the presence of water will lead to a formation of a galvanic cell between the aluminum (anode) and the screen (cathode), which facilitate the corrosion of the aluminum conductor [7]. This phenomenon was named “Stress Induced Electrochemical Degradation”. In later work, it was reported that the growth of these structure is a consequence of a mechanical damage caused by the hydrogen gas pressure build up upon the oxidation of aluminum [8]. Up to this point, all the previous studies produced this phenomenon in the laboratory, and it was not reported in service.
The first time this phenomenon was reported on service aged cables in 2009 [9]. Cables were pulled out of service due to failure and high density of vented water trees were observed after the removal of the outer screen. An interesting observation was the vented water trees ‘following’ certain of conductor strands.
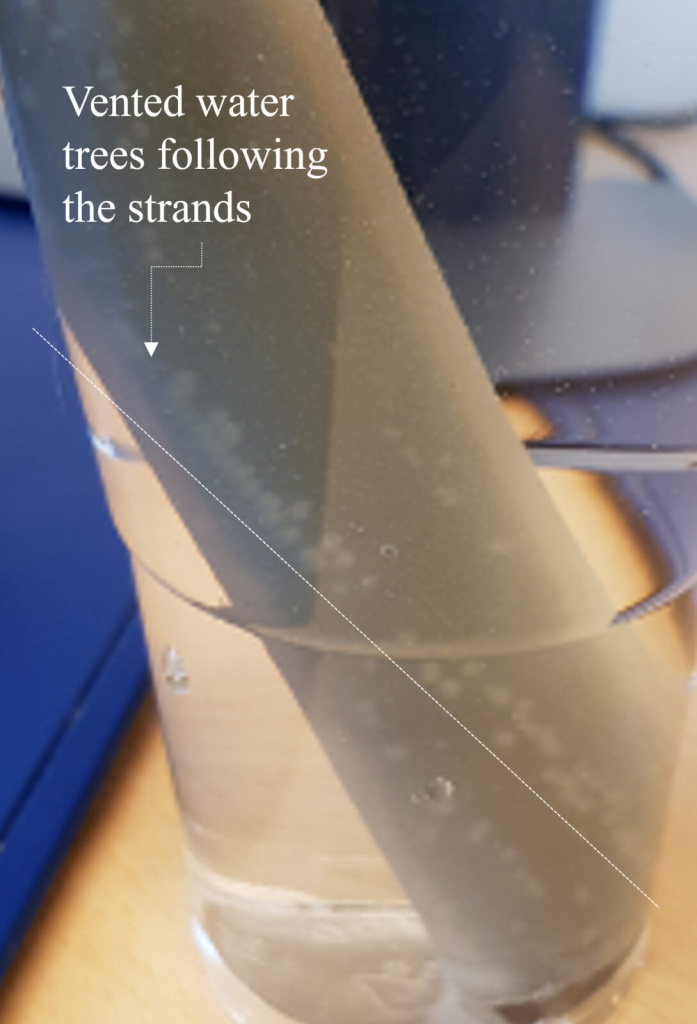
In [9], it was argued that damage due to hydrogen gas pressure build-up is less likely to occur. This argument was on the basis of the significance molecular weight of hydrogen gas has making it difficult to obtain sufficient pressure to mechanically damage to the polymeric insulation. Instead, the formation of microcracks initiated by environmental stress cracking (ESC) was suggested after observation of fibrils bridges via SEM, which is commonly occurs in ESC.
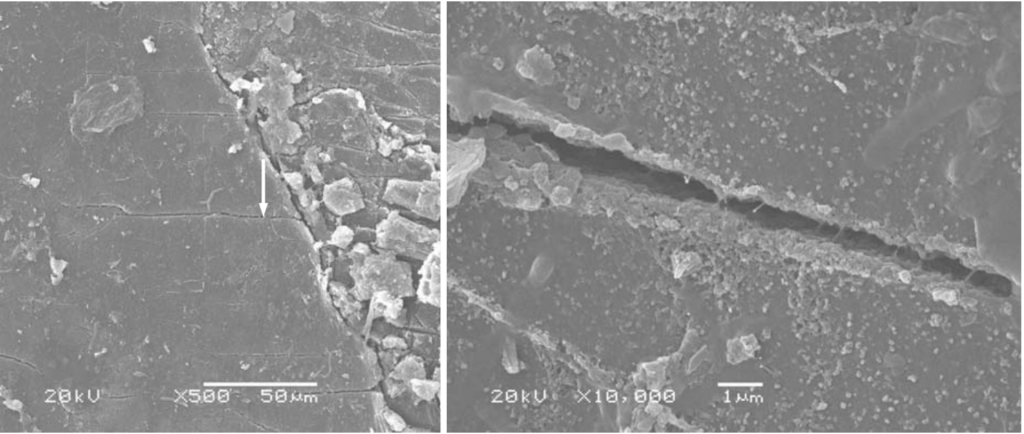
Whilst the previous work suggested that ESC is the main mechanism of growth of porous channels, yet the initiation mechanism is not well explained.
In this blog, we went briefly through a summary of the research done in regards to the initation mechanisms of water treeing, which is a major critical aging mechanism for power cables. Whilst there was much work done in the past, some pieces to the puzzle are still missing. With better understanding, a more efficient cables can be developed, and electrification can be facilitated. Thus, there is an emerging need of utilizing more material characterization methods to reveal more information about the initiation of water trees.
Read:
Abideen, Amar; Mauseth, Frank; Hestad, Øystein Leif Gurandsrud; Faremo, Hallvard. (2022) Review of Water Treeing in Polymeric Insulated Cables. Proceedings of the Nordic Insulation Symposium. volum 27 (1).
References:
[1] E. Steennis and F. Kreuger, ”Water treeing in polyethylene cables,” IEEE Transactions on Electrical Insulation, vol. 25, no. 5, pp. 989-1028, 1990.
[2] T. Miyashita, ”Deterioration of Water-immersed Polyethylene Coated Wire by Treeing,” in Proceedings 1969 IEEE-NEMA Electrical Insulation Conference, Boston, 1969.
[3] S. Hvidsten, ‘Wet cable designs’, Trondheim, 2020
[4] J. Sletbak, ”The mechanical damage theory of water treeing – A status report,” in Proceedings of the 3rd International Conference on Properties and Applications of Dielectric Materials, Tokyo, 1991.
[5] W. Kalkner, U. M ̈uller, E. F. Peschke, H.-J. Henkel and R. v. Olshausen, ”Water treeing in PE- und VPE-isolierten,” Mittel- und Hochspannungskabeln Elektrizit ̈atswirtschaft, no. 26, pp. 911-922, 1982.
[6] D. Meurer, D. Kaubisch and W. G ̈olz, ”Zum Langzeitverhalten von Isoliersystemen f ̈ur VPE-isolierte,” Mittelspannungskabel Elektrizit ̈atswirtschaft, vol. 89, no. 26, pp. 911- 922, 1990.
[7] K. Steinfeld and W. Kalkner, ”Stress Induced Electrochemical Degradation of the inner Semicon Layer of extruded Cable Insulation,” in I.C.D.I., Budapest, 1997.
[8] M. Bruggerman, W. Kalkner, A. Campus and A. Smedberg, ”Electrochemical effects at the conductor/dielectric interface – a description of the mechanism,” in Proceedings of the 2004 IEEE International Conference on Solid Dielectrics, Toulouse, 2004.
[9] S. Hvidsten, S. Kvande, A. Ryen and P. B. Larsen, ”Severe degradation of the conductor screen of service and laboratory aged medium voltage XLPE insulated cables,” in IEEE Transactions on Dielectrics and Electrical Insulation, vol. 16, no. 1, pp. 155-161, February 2009, doi: 10.1109/TDEI.2009.4784563.
Comments
Interesting blog. Two main doubts:
1) The 1st figure caption states “Example of a vented water tree growing from the outer screen found in a service aged cable”: due to the slight downward curvature of the semicon, isn’t it the inner screen instead?
2) “Figure 2: Example of SIED structures found on a service aged cable near the root of a vented water tree”. I can see neither the SIED structures, nor the (root of a) vented water tree in this Figure.