In the face of the most recent and drastic climate report of the UN, the reduction of our fossil fuel consumption is a “must” in order to limit the impact of global warming. However, many industrial processes require fossil fuel in order to supply process heat and without a substitution for this supply chain it will be unlikely that we will reach the climate targets. Fortunately, SINTEF Energy Research has developed a prototype high temperature heat pump in the HeatUp project, and the results are very promising.
Heat pumps don’t match current industrial requirements
Current heat pump solutions are mostly limited to heat supply of around 70°C to 80°C, while industry process are quite often designed for heat supply temperature of around 100°C to 110°C. From an R&D point of view the challenge was therefore to demonstrate that the supply temperature can be increased by 30 °C to 40 °C.
SINTEFs researchers have now developed a prototype heat pump that pushes the current temperature limitations and can be universally used in order to supply process heat of up to 115°C. Considering the climate aspect of fossil fuel it seems illogical to use a valuable energy source like oil or gas in order to produce something as simple as heat around 100°C. Nevertheless, every year around 170 TWh of process heat (Equal to 1,5 times the consumption of all electricity in Norway), especially in the food industry, are produced in the EU28 by exactly this, burning fossil fuels, mostly to supply hot water.
Read this blog from when we installed the heat pump:
Experimenting with working medias for high temperature heat pumps
In order to reach the high temperature target, different working medias were investigated for their capability in a heat pump with respect to energy, climate impact and cost efficiency. “In the end, we concluded that Butane in the top cycle would fulfil our requirements and in order make the heat pump practically applicable we suggested Propane in the bottom cycle” explains PhD student Opeyemi Bamigbetan. Butane is a natural refrigerant with near zero global warming potential. Together with the team from SINTEF and NTNU a prototype heat pump was designed and installed in the laboratory.
Christian Schlemminger, research scientist at SINTEF, clarifies: “Our aim is not only to find good and efficient solutions, but also to demonstrate that these solutions are actually applicable in real life. Therefore, it was extra exciting to see how we can solve this challenge in theory and in practice”.
After more than 2 years of building and testing in the lab the results are very promising. This work demonstrated that it is possible with more or less standard refrigeration components to reach heat supply temperatures of up to 120°C. But it doesn’t stop there!
Potential Add-on
One of the main inhibitors for industrial implementation of high temperature heat pumps is the system integration, which normally generates dependencies between heat sink and a heat source. Therefore, two universal concepts for the heat pump system were investigated. In the first concept the heat pump not only provides process heat, but also process chilling in the form of ice water. In many industrial sites, in which process heating is required, there are also processes which require cooling. The second concept is in principal an Add-on to existing refrigeration units, which are currently wasting its excess heat.
Safety in focus
The heart of the heat pump is a compressor prototype which was designed in cooperation with an Italian manufacturer. In fact, the compressor is the only component in the heat pump which was custom made and is not off-the-shelf. Since Butane is a flammable working media special focus was on safety and process control in order to give not only optimal working conditions but also a high level of safety.
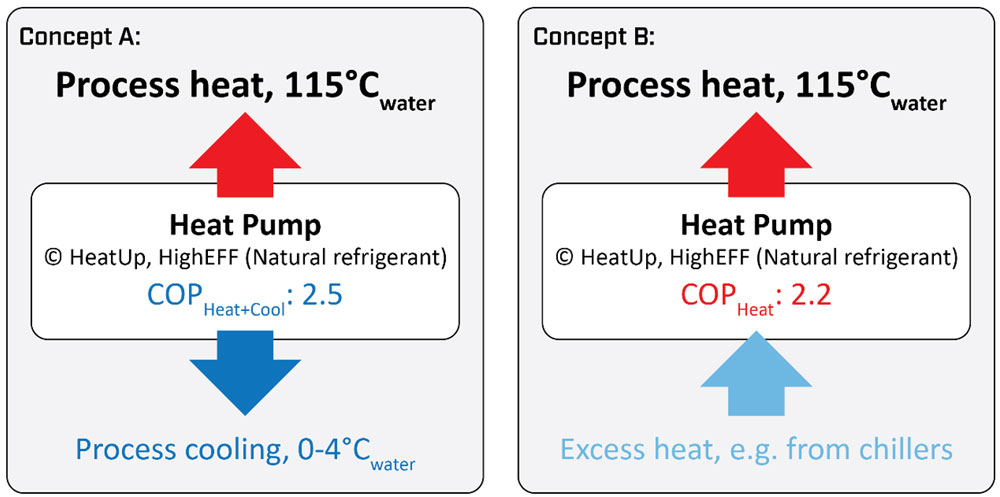
Both concepts were tested by SINTEF in their prototype installation and the Coefficient of Performance (COP) was 2.5 for concept A and 2.2 for concept B. This means that for every kilowatt of supplied electric energy 2.5 or 2.2 kilowatt of “useful” thermal energy was supplied. Compared with the COP of 0.9 – 0.95 of fossil fuelbased boilers, this were really competitive result. “Or in other words: Our prototype installation is 2.5 times as efficient as current boilers and can operate in principal everywhere between 0 °C and 120 °C”, says Christian Schlemminger and adds “We feel that our solution is quite complementary to the existing heat pump technology and we expect a high market potential for both concepts”.
At the same time the emission of climate gases is reduce for every kilowatt-hour of thermal energy which is supplied by the heat pump, depending on how the electricity is produced. In the next years the work will focus on cooperation with an interested heat pump manufacturer in order to develop a market ready solution at industrial scale.
Announcement
Do you want to know more? PhD student Opeyemi Bamgibetan will defend his thesis on the development and verification of the novel heat pump concept on Tuesday 18 December 2018 at the Gløshaugen campus in Trondheim.

We have made a mini-series on natural refrigerants and heat pumps. First episode below:
Facts:
What is a heat pump?
A heat pump is a technical installation which transfers heat from a colder area to a hotter area by using mechanical energy. The most know application is surely household refrigeration, in which the inside of the refrigerator is kept cold while the back of the refrigerator is getting warm. In order to transfer this heat a working fluid called refrigerant is needed. The refrigerant is evaporated in the cold part of the heat pump, hereby removing energy from a system (=chilling). The refrigerant is then compressed and transported by a compressor (=mechanical energy) to the warm side where the energy during condensation of the refrigerant is given to another system (=heating). The cold and warm systems are separated and therefore heat is “pumped” from cold to warm. The temperature level of the cold and warm area is a result of different evaporation and condensation pressures in the system.
In most heat pump systems, the mechanical energy needed for the compressor is supply by an electric motor. It is the characteristic of a heat pump that the electricity consumption is lower than the transferred energy. This is expressed by the Coefficient of Performance (COP) which states how much useful heating or cooling is provided compared to the work supplied. The COP of a heat pump is commonly getting lower as higher the temperature difference between cold and warm area is.
Need for natural refrigerants:
Natural refrigerants (like CO2, ammonia, hydrocarbons) were the first generation of refrigerants and used until 1930, when the second generation of refrigerants was introduced under the aspect of “safety and reliability” [1]. However, their negative influence on the ozone layer forced the industry to introduce the third generation of refrigerants (HFCs e.g. R134a) through the Kyoto protocol. HFCs then showed a high global warming potential (GWP) and will be phased out due to the Kigali protocol and the F-Gas regulation. For industrial application from 2020 the installation of new refrigeration equipment and heat pumps containing refrigerants with high GWP (e.g. R134a, R404A, R407C, R410a, R507A) will be forbidden. The service of existing units can only be conducted by applying recirculated refrigerants causing price increase for maintenance. The units need to be phase out until 2030. The industry now promised that the fourth generations of refrigerants (HFOs) will solve also this problem, however already now there are indications that also these refrigerants could cause problems, e.g. in the drinking water[2]. Consequently, there is an ongoing search for the “right” refrigerant and the trend goes back to the first generation of natural refrigerants which will cause no environmental impact. In other words; if a natural refrigerant can be applied in in a heat pump this should be the favourable solution, since they can be handed safe, are cheap, environmentally friendly and will not be subject to future regulations.
- [1] https://www.energy.gov/sites/prod/files/2014/12/f19/Refrigerants%20Roadmap%20Final%20Report%202014.pdf
- [2] German Environment Agency: https://www.umweltbundesamt.de/themen/auf-umweltfreundliche-kaeltemittel-umsteigen published 10.07.2018
Comments
This breakthrough in high-temperature heat pumps by SINTEF Energy Research is a significant step toward reducing industrial reliance on fossil fuels. By achieving process heat up to 120°C using butane and propane, the HeatUp project demonstrates a viable, energy-efficient alternative for industries like food processing. The integration of process chilling and add-on capabilities enhances its practical application. With safety at the forefront, this innovation paves the way for more sustainable industrial heating solutions.
This breakthrough in high-temperature heat pump technology is a game-changer for industrial energy efficiency. By pushing temperature limits while maintaining high COP, SINTEF’s innovation offers a sustainable alternative to fossil fuel-based heating. Kudos to the team for their dedication to real-world applications! Looking forward to seeing this technology scale up. Thank you!
SINTEF’s development of a novel high-temperature heat pump marks a significant step toward phasing out fossil fuels. By providing efficient industrial heating solutions, it reduces reliance on carbon-intensive energy sources. This innovation supports sustainability goals, enhances energy efficiency, and accelerates the transition to a greener future.
Great article! SINTEF’s development of a high-temperature heat pump is a crucial step toward the phase-out of fossil fuels. Innovations like this can significantly improve industrial energy efficiency and accelerate the transition to sustainable heating solutions. Looking forward to seeing how this technology scales in real-world applications
This article provides a compelling look at SINTEF’s groundbreaking high-temperature heat pump technology, which has the potential to revolutionize industrial heating while reducing fossil fuel dependence. The detailed insights into efficiency, safety, and real-world applications make this an exciting development. Thanks for sharing such an important step toward sustainable energy solutions!
This article highlights significant advancements in high-temperature heat pump technology using natural refrigerants like Butane and Propane. The promising results demonstrate a potential leap in energy efficiency and environmental impact. Thank you for sharing these insights and the exciting developments in sustainable HVAC solutions!
Great article! You said very well. In most heat pump systems, the mechanical energy needed for the compressor is supply by an electric motor. Thanks for sharing
Hey MICHAEL! You had posted such a great blog on internet, no other article can beat the information this article contains.