An essential aspect of pipeline design is avoid running ductile fracture (RDF), which is when a pipeline defect develops into a fracture under pressure forces from the escaping fluid.
Inadequate methods?
The prediction of RDFs is crucial for ensuring the safety and efficacy of pipelines, especially for the transportation of CO2. However, current design methods, such as the Battelle two-curve method (BTCM), which were developed in the 1970s for natural gas pipelines, have been found to be inadequate for CO2 pipelines.
The BTCM method compares the speed of crack propagation to the rate of fluid decompression to determine whether a crack will propagate along the pipe with a steady fluid pressure at the crack tip. Although the method appears to separate the fluid and material properties, the material properties are based on correlations derived from full-scale tests where fluid and material properties are strongly coupled. Therefore, it is reasonable to assume that the description of material properties should change when replacing natural gas with CO2.
New fluid, new curves
In a recent work, together with my colleagues at SINTEF and NTNU we examined the BTCM in the context of available RDF experiments with CO2-rich mixtures and presented an improved material curve that accounts for the change in fluid properties. This new curve provides a much better separation of the arrest and propagate regions, as shown in Figure 1. By improving our understanding of the behavior of CO2 in pipelines, we can better ensure the safety and efficacy of CO2 transportation.
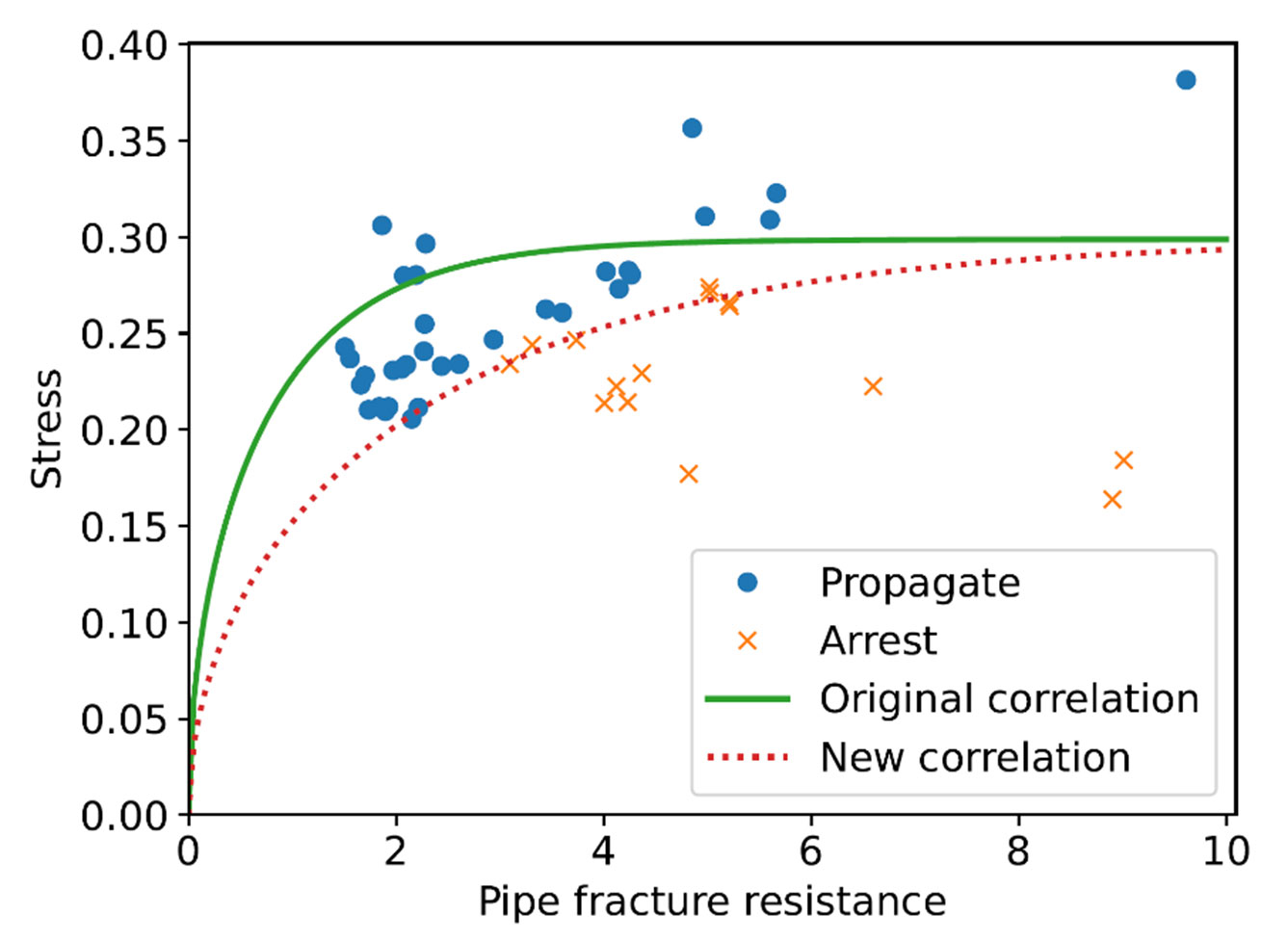
Estimating the crack-tip pressure is a crucial aspect of predicting RDFs. The standard method is to assume that liquid CO2 boils at the liquid saturation pressure. In reality, the rapid depressurization forces the liquid out of equilibrium, resulting in boiling pressures that are lower than the saturation pressure. To address this issue, we have developed an improved method for calculating the crack-tip pressure for CO2-rich mixtures called the delayed homogeneous equilibrium model (D-HEM). By accounting for the non-equilibrium thermodynamics that occur due to the rapid depressurization, the D-HEM yields more accurate predictions of the boiling pressure (see Fig. 2). Thus, also the fluid treatment in the BTCM for CO2 is improved.

Improved results
Overall, the adaptation of the material and fluid treatment provides improved results and is a step towards a viable engineering tool for predicting running ductile fractures in CO2 pipelines. This has practical implications, as it can avoid expensive overdesign and perhaps worse, overestimation of material strength. By improving our understanding of the behavior of CO2 in pipelines, we can better ensure the safety and efficacy of CCS as a means of reducing CO2 emissions.
This work was performed in the Norwegian CCS Research Centre (NCCS), supported by industry and the Research Council of Norway.
Comments
No comments yet. Be the first to comment!