Control optimisation can save up to 30% of the system’s energy consumption. This indicates the importance of this research field. In addition, the control logic tracks and maintains diverse parameters depending on the thermal application type. For example, in the food refrigeration sector, the control logic increases the supply chain’s security. When heating and cooling different buildings, control logic maintains thermal comfort and indoor air quality.
The Modelica programming language, or as I like to call it, the engineer’s programming language, can model cyber-physical systems with high credibility. While utilising the control description language (CDL), Modelica can mimic real-world control. For thermal systems, applying Modelica language requires strong control and a background in mechanical engineering fundamentals (heat transfer, fluid mechanics thermodynamics), as well as programming skills.
PCM STORE: developing the integrated thermal dynamic models of a heat pump and TES system integrated with the control logic that allows for charging/discharging the PCM HX based on storage status and the district cooling thermal demands, respectively,
ZEESA: ongoing modelling work of a district heating system utilising industrial surplus heat in the Arctic
SeaZero: ongoing modelling and design of both different thermal zones (“cabinets and other facilities”) and the overall thermal system of a zero-emission fossil fuel ship
ITchES: ongoing modelling work of a thermochemical storage system, which will support the utilisation of sources of industrial surplus heat at a higher efficiency, compared to the convenient water and phase-change materials (PCM) thermal storage systems.
These aforementioned projects are relevant to for industry, and many clients have shown interest in our integrated dynamic models.
Both the general dynamic modelling and the specific control logic utilised by the Modelica language are gaining more and more credibility among clients in Norway and around the world. Our clients usually ask SINTEF Energy Research for customised control logics integrated into a detailed model. This model, with its relatively low costs compared to experimental tests, can mimic real-world challenges before reaching the final stage of designing and industrialising the idea. The integrated, detailed and sophisticated model enables testing of components for heat exchangers, compressors, etc., and the examination of an advanced control sequence of operations to maximise the system efficiency.
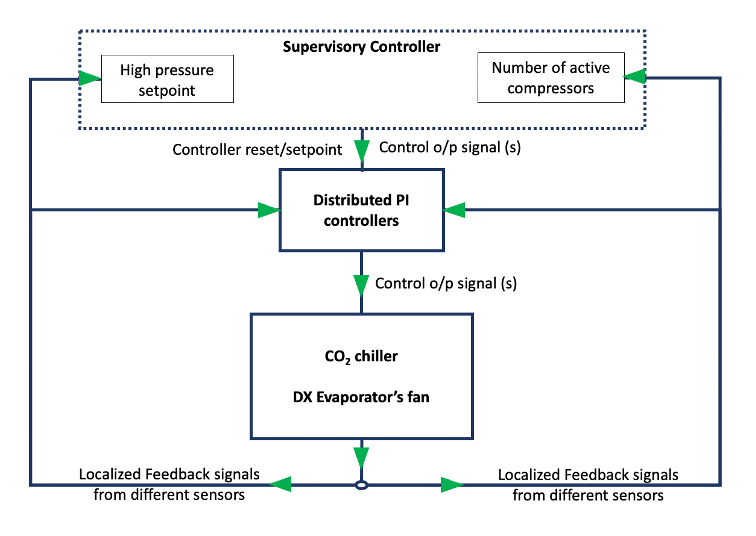
The main objectives of the controller are:
- Tracking and maintaining different design variables;
- Deciding the sequence of operation. For example, in a district heating system, the controller should decide how many compressors should stay in action at a heat pump, or how many circulating pumps should be switched OFF or ON.; and
- Detecting faults and predictive symptoms for maintenance purposes.
The detailed integrated models can capture the smallest physical phenomena, which will open the door for researchers and industrial partners to conduct more reasonable and scientific validations of innovative solutions. In addition it will explain and highlight the client’s current system’s shortcomings or malfunctions and the reason behind it.
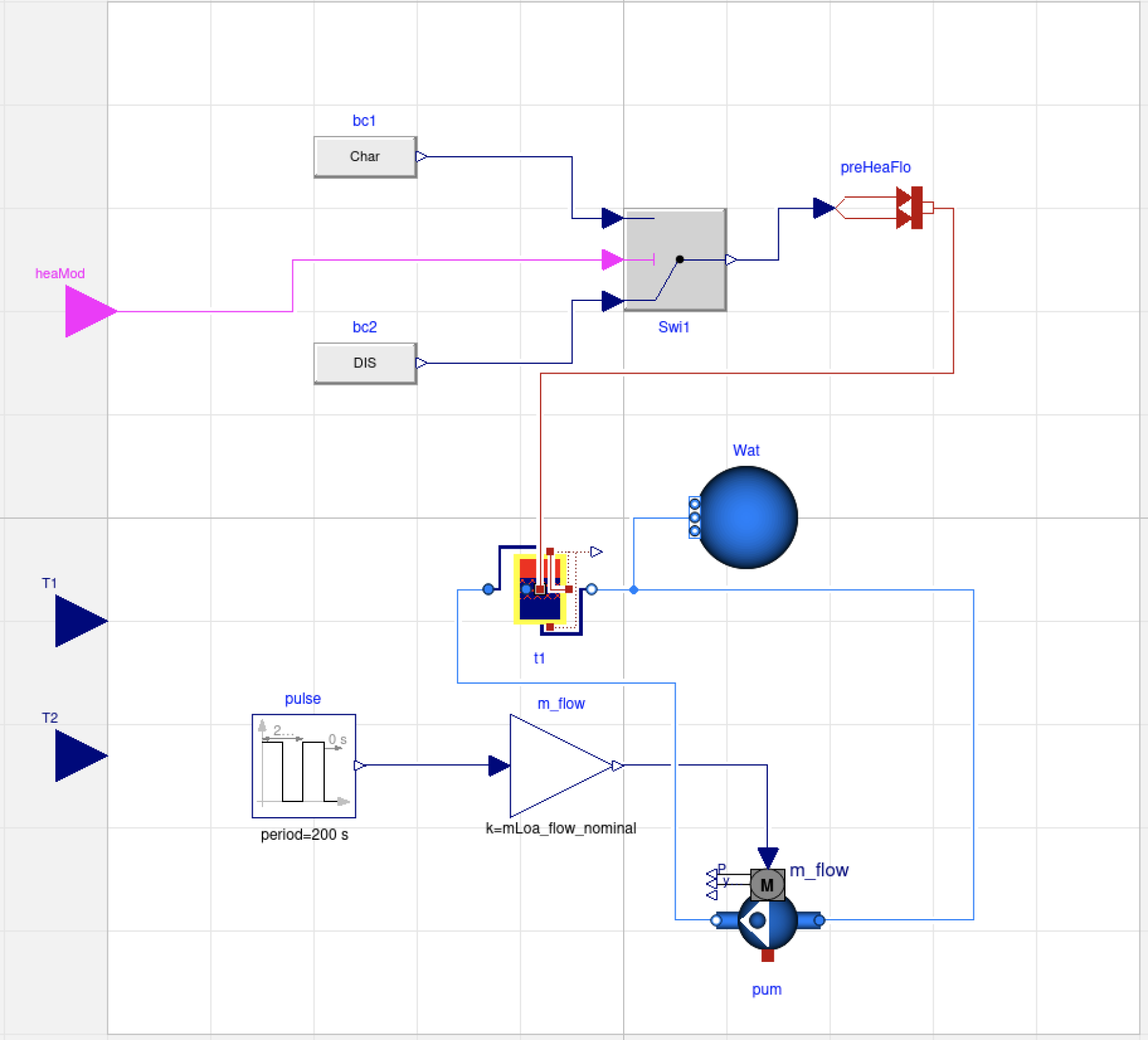
The customised integrated modelling solution developed in each case study gives the industrial client a technological advantage.
Modelling is relatively inexpensive compared to experimental solutions, which makes it a tempting alternative for both low and high-budget projects.
Comments
No comments yet. Be the first to comment!