Bloggers: Kristin Jordal and Kristina Fleiger (VDZ)
The Horizon 2020 CEMCAP project brings together CCS interests and research expertise from the cement industry with research expertise on CCS for power plants. The CEMCAP project has been designed to strengthen and complements the Norcem and ECRA CCS projects , and will conduct analytical and experimental research on CO2 capture for cement plants.
The primary objective of CEMCAP is to prepare the ground for large-scale implementation of CO2 capture in the European cement industry. For this to be possible and for CEMCAP to be as successful as possible a key element is knowledge transfer between cement industry and CO2 capture expertise acquired over more than a decade of FP6 and FP7 research projects. Therefore, a first CEMCAP/ECRA workshop was held already during the fifth month of the project, on September 16-17 2015. Attendants were members of the ECRA CCS steering committee and CEMCAP project members.
Day 1: Post combustion CO2 capture technologies + transport and storage challenges
The first day, arranged at VDZ in Düsseldorf, Germany, and gathering 40 attendants was dedicated to CCS. The workshop started with a short overview of global warming, and of how Horizon 2020 calls for research projects for a low-carbon economy is one of several EU measures to address the necessary reduction of European CO2 emissions.
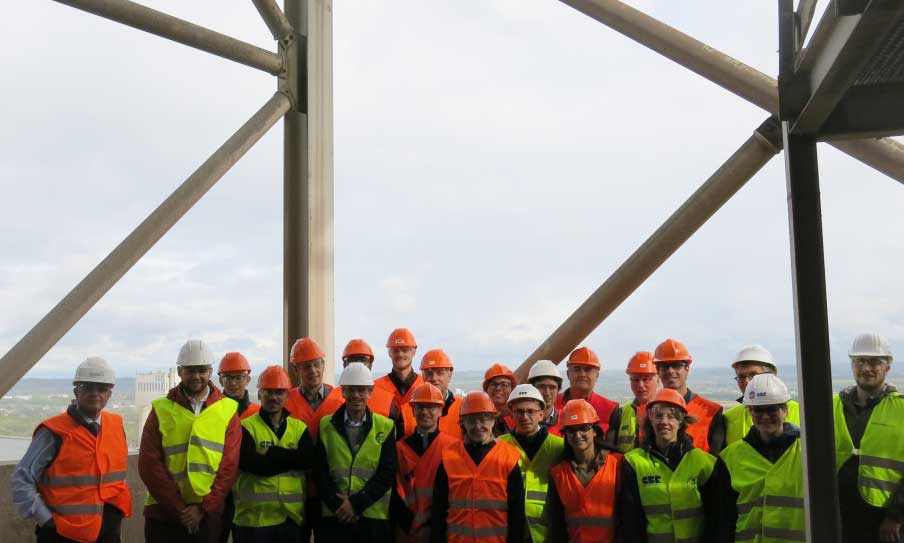
Thereafter, the CEMCAP project members gave insights into CEMCAP post combustion capture technologies (Chilled ammonia, membrane-assisted CO2-liquefaction and calcium looping). Also, a presentation was given on amines as the reference post-combustion capture technology. Furthermore, a most welcome and very interesting overview was provided of the oxy-combustion research carried out by Lafarge-Holcim.
In order to make the picture complete, day one also included a presentation on the research challenges within CO2 transport and storage, with particular focus on how improved knowledge in thermodynamics, fluid mechanics and solid mechanics can enable more accurate CO2 pipeline design and thus reduce transport investment costs. To conclude, a critical view on the prospects for CO2 use (CCU) to contribute to reduce net CO2 emissions to the atmosphere and mitigate global warming was provided.
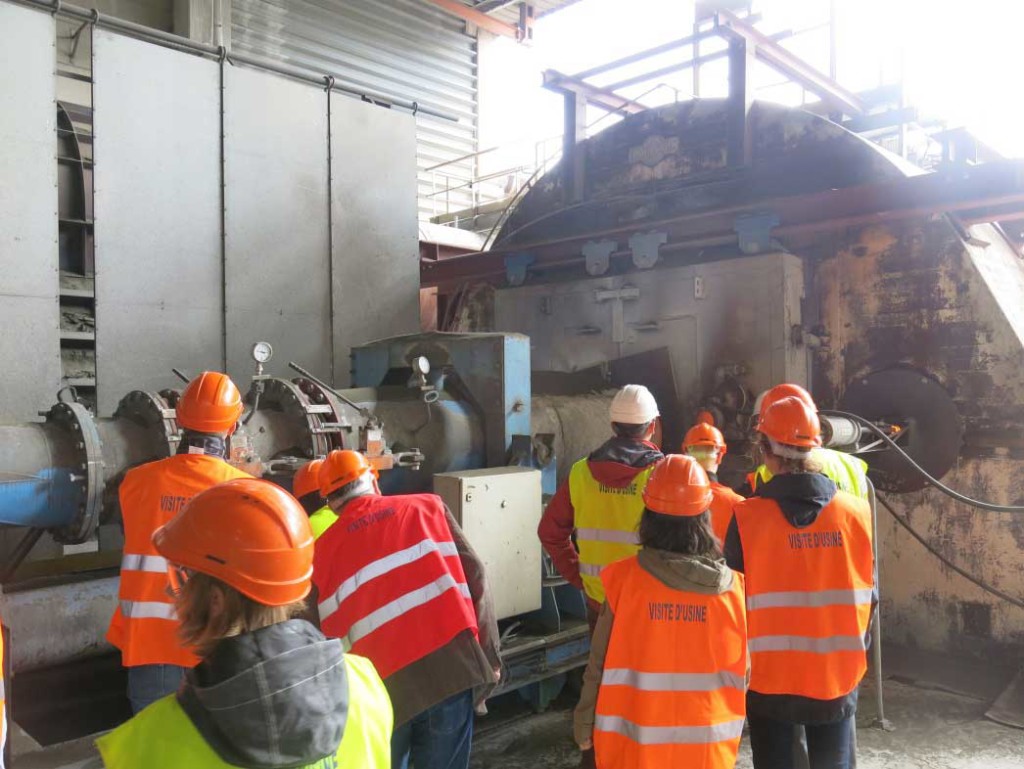
Day 2: CBR cement plant
The second day of the workshop was spent at the CBR cement plant (belonging to HeidelbergCement Group) in Lixhe, Belgium. Lectures were given by ECRA members before a guided tour to the cement plant.
Key issues covered during the lectures were:
Cement and concrete:
- Overview of the cement production process, what are the chemical reactions during clinker burning and the resulting clinker phases.
- Overview of different standardized types of cement, their compositions, cement hydration and requirements on concrete.
Modern clinker production:
- Cement kilns are operated continuously for ~300 days/year or more.
- Ongoing development towards increased energy efficiency and use of alternative fuels
- The origin of CO2 emissions (CaCO3, fuel, electricity)
- The temperature profile of gases and materials along the clinker production process
- Key elements in plant design and functioning of the different elements of the kiln.
- The main advances in cement production over the past few decades are due to improved measurement and analysis techniques as well as process control.
Raw materials and fuels:
- Constituents of clinker are CaO (main constituent), SiO2, Al2O3, Fe2O3.
- Coal is so far the basic fuel for most European cement plants.
- Use of alternative fuels in the kiln is an opportunity for reducing the use of fossil fuels.
- Due to the changed fuel properties (heating value, shape, homogeneity etc.) of alternative fuels challenges for the kiln operation might occur.
- Examples of alternative fuels are: Pre-treated industrial or domestic wastes, wood chips, granulated plastic, sewage sludge, animal meal, car tires.
Emission abatement technologies:
- Cement plant emissions are regulated under the Industrial Emissions Directive (2010/75/EU).
- Examples of emissions that must be limited according to this directive are dust, HCL, HF, NOx, SO2.
- The directive requires use of BAT (best available technologies).
The guided tour to the Lixhe cement plant gave CCS researchers insight into the dimensions of such a plant, and valuable understanding of how the plant is operated. The experiences and knowledge gained from this second day of the CEMCAP/ECRA workshop will be directly applied in the upcoming CEMCAP research – the CEMCAP project is now concluding an initial phase with preparations for experimental research and establishment of a consistent techno-economic framework. Work will now be directed towards experimental and analytical research.
0 comments on “First workshop to prepare the ground for large-scale CO2 capture from the cement industry in Europe”