Metals have a wide range of uses, and can be found in countless products that we take for granted today. Our society is, quite literally, built on a foundation of metal, and has been since the Iron Age.
A lot has happened since then, including the Industrial Revolution, which was also enabled by the discovery of fossil resources (first coal, then oil, and finally gas). In Norway, we have also been lucky enough to be able to produce power from water – hydropower – as an important contribution in this revolution. Others have had to rely to a much greater extent on those fossil resources.
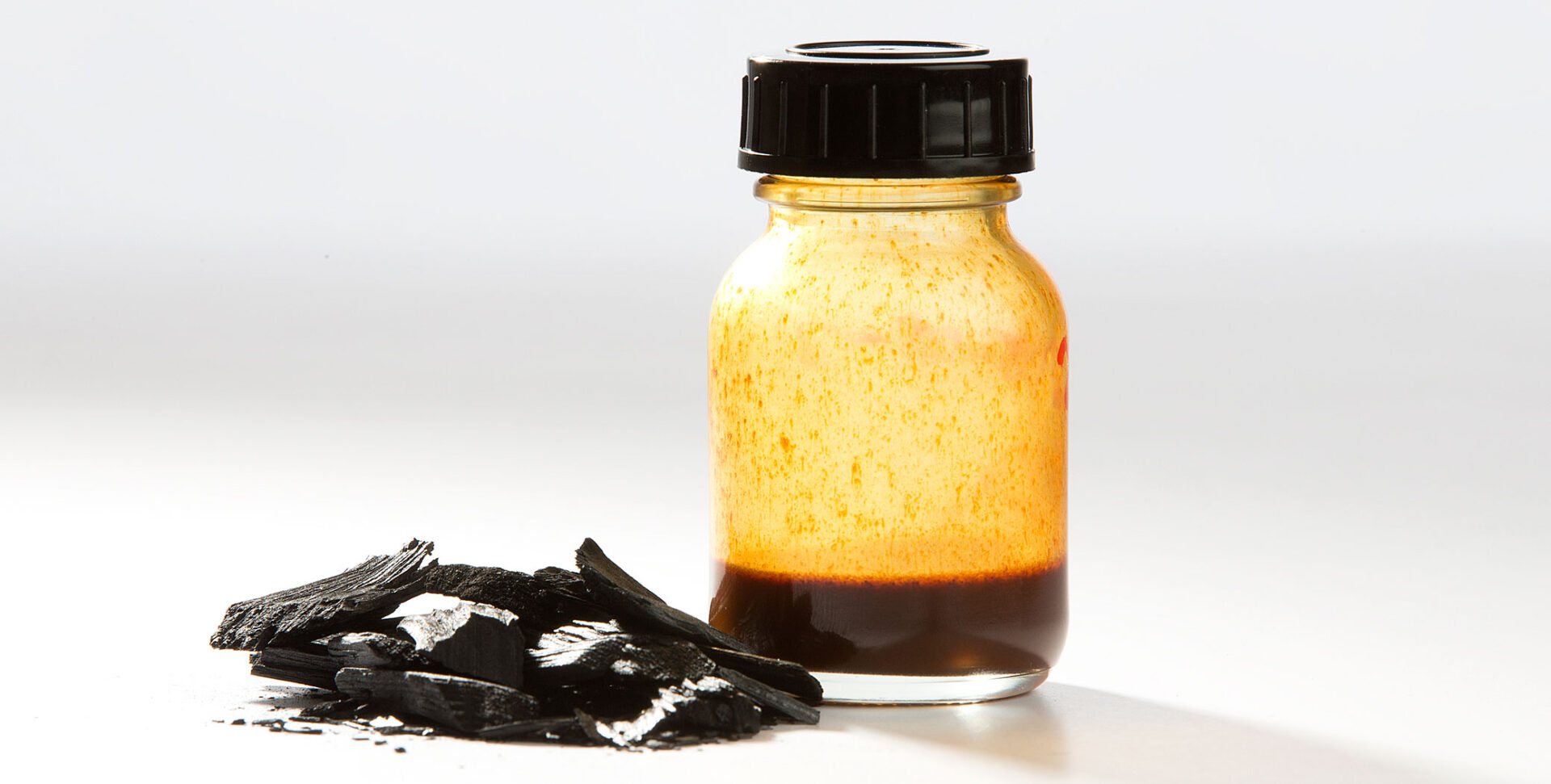
Biochar and tar/bio-oil can replace fossil materials in metallurgic processes. However, the Industrial Revolution has left deep scars, not least of which include global warming, which has led to the climate crisis we’re currently experiencing. Put simply, we have to fix this, for both our children and planet Earth.
Fossil resources for meeting the material need
The metallurgic industry still uses fossil resources in metallurgic processes, not to meet energy needs but to meet material needs. These processes need carbon to remove oxygen from metal oxides. Since the oxygen is bound extremely well to the metal, a lot of energy is needed to remove it.
This is where Norwegian hydropower enters the picture, as it provides the electrical power required to achieve the high temperature needed in metallurgical processes for removing the oxygen and producing pure metal. The fossil carbon ends up as CO2, which is currently released into the atmosphere, contributing to global warming.
Renewable carbon from biomass
For several decades, the metallurgic industry in Norway has been investigating opportunities to replace the fossil carbon with renewable carbon from biomass.
Earth’s biomass is renewable because it is part of a short carbon cycle, wherein it is used and converted into CO2 emissions as part of various natural processes, and continuously replaced. Moreover, the amount of carbon used in this process is constant, and the average amount of CO2 emitted to the atmosphere as part of this cycle is therefore zero. However, using this biomass in industrial processes does result in actual CO2 emissions, and therefore, it is important that it is used as efficiently as possible.
Challenging to replicate fossil resources for the metallurgical industry
We could produce alternative materials to use instead of fossil resources, but the characteristics of the fossil resources that the metallurgical industry needs are challenging to replicate. For example, fossilised coal is the result of a conversion process that took millions of years, wherein the biomass has been buried and slowly converted to various coal forms, depending on the process conditions (pressure, temperature and time).
When we talk about the characteristics of coal, we are mainly referring to its strength and reactivity. Traditional charcoal production leads to lower strength and higher porosity, and therefore higher reactivity with CO2, than the coal qualities that are used in metallurgical processes (based on bituminous coal, or anthracite). In order for the solid carbon to survive long enough on its way down in the metallurgical furnace, to where it is needed, it needs high strength and low reactivity.
In addition, bituminous coal is often upgraded to coke in order to satisfy the requirements for some metallurgical processes. The coal tar pitch resulting from this upgrading process is repurposed as a binder in anodes that are used in the current aluminium industry. Petroleum coke, produced from the heaviest part of crude oil, which does not yield liquid petroleum products, is the source of carbon in these anodes.
Therefore, we must instead investigate how the biochar can achieve better characteristics when it is produced, or how it can be upgraded to achieve the same.
The biochar should also be procured in the most sustainable way possible throughout its entire value chain, from the resource stage to its end use in the metallurgical industry. This will minimise the resulting CO2 emissions from this value chain as well as address other pillars of sustainability, such as the environment in general, the economy, and social needs.
Moreover, biochar for the metallurgical industry is currently mainly based on wood. Whether we have enough biomass resources to meet all needs in the future is a very pressing issue, and therefore, perhaps biochar for this industry should also be based on other biomass sources than wood.
Optimising the biocarbon chain
In the collaborative and knowledge-building project BioCarbUp, we have spent four years investigating how the biocarbon chain for various metallurgical industries in Norway can be optimised, in terms of producing biochar with satisfactory characteristics in a sustainable way.

Biochar’s characteristics are defined by the origin of the biomass it is based on, and even different tree species will produce biochar with varying properties. For example, the density of the tree species will impact the density, strength and porosity of the biochar. As such, the biochar that is currently used in the metallurgical industry (in silicon and ferrosilicon production) is based on hardwoods in order to achieve better characteristics.
Once the biochar has been produced, it is important to lose as little as possible of it as fine dust when it is handled and transported. Fine dust represents a loss of valuable carbon, and is hazardous to both the environment and our health. Therefore, it is best to prevent – or at least limit – the formation of fine dust. One way of trying to satisfy the requirements for resource utilisation, as well as strength and reactivity, is to collect any fine dust formed and use it, for example, to produce compressed biochar in the form of briquettes or pellets.
For metallurgical processes, the solid carbon is important, as the carbon that is gassed off during the process will not act as a reducing agent. Yield of solid carbon in a biochar production process depends a lot on various process conditions. Traditional charcoal production typically results in a relatively low yield of fixed carbon.
The yield can be increased considerably when the tar components that are gassed off spend more time in and near the biochar. This enables the fixed carbon potential in the tar components to also be utilised, and the theoretical potential to be achieved, which can be calculated through an equilibrium calculation. This can be achieved for larger particles, at a low heating rate, without the addition of carrier gas, by ensuring internal or external recycling of tar components and by pressurising the process.
The strength of biochar can be increased through densification and compression. For densification, the biochar is used as a catalyst for splitting methane (from, for example, biogas production), so that the carbon attaches to the biochar surfaces inside the porous biochar, creating hydrogen as the residual product. A postdoctoral researcher in BioCarbUp investigated this, and demonstrated that it was possible to achieve significant densification that resulted in increased strength and reduced reactivity.
Compression can take place in the traditional way by making briquettes or pellets from biochar powder by using a binder (glue). The tar components from the biochar production process can also be used as a binder, and when these compressed materials are heated before or in a metallurgical process, the tar components will contribute to an increased solid carbon yield. Alternatively, biochar can be produced from compressed biomass, e.g. pellets made from steam-exploded wood. The tar components can also replace the currently used coal tar pitch as a binder in the production of anodes.

During pressurised biochar production, at special conditions, the tar components can act as a binder in the biochar as a direct result of the production process itself. When this biochar is further compressed, the end product is a highly compressed biochar with very high strength.
However, there are other important characteristics than strength and reactivity, and we need to look at the whole picture when assessing the suitability of different grades of biochar for use in metallurgical processes. The most critical requirement must be satisfied first, and having a good analysis procedure to make that evaluation as effective as possible becomes important. With the extensive knowledge that has been built up over the years in the metallurgical industry and at SINTEF, it is now possible to do this without carrying out costly experiments.

We then approach something similar to what Mother Earth has spent millions of years producing, and which can actually be used in current metallurgical processes. However, we still need to do this in a way that satisfies the economic pillar of sustainability. Therefore, a lot of work remains to further develop, test, verify, streamline and optimise concepts and processes, as well as expand the biomass resource base to ensure access to resources, reduce the resulting CO2 emissions and the CO2 footprint (from the use of fossil resources) throughout the entire value chain, and – not least – reduce costs.
We must not forget why we are doing this
Finally, we must not forget why we are doing this – aka going to large lengths to produce something that can be characterised as gold (from a metallurgical point of view) from rock (aka biomass).
We are doing it to reduce global warming. It does not matter where the CO2 molecule comes from or where it was emitted from at Earth. All biomass that is used for various energy or material purposes, and that, by definition, does not contribute to global warming, is a very valuable resource, with the potential to substitute fossil resources used for the same purposes. In order to maximise this substitution effect, we need to utilise our biomass resources in an optimal way, including reducing the associated CO2 emissions, and in interaction with other renewable resources.
A timely yet sensitive question then remains: will we have enough biomass in the future, and if not, what will we use it for? Here, prioritising CO2 footprints or finances can give completely different answers.
A fresh article in EERA bioenergy newsletter entitled “The contribution of biomass to reduce global warming” tries to set this in perspective.
If you want to know more about the BioCarbUp project and its results, you can look at the handbook we produced.
We’re starting a new project
A new collaborative and knowledge-building project is due to start in 2023 to continue to develop the knowledge base, which will enable us to obtain biochar for use in various metallurgical industries. This will be a very important contribution to substituting the fossil resources that are currently used, and which contribute significantly to global warming.
After all, this substitution is about sustainable carbon cycles. For the climate on Earth, a CO2 molecule is a CO2 molecule, and when it is released into the atmosphere, it contributes to global warming. Where the carbon comes from becomes a technicality. Therefore, we must be aware of our responsibility, and contribute to reducing the total CO2 emissions by optimising the coverage of all our energy and material needs to minimise our CO2 footprint (globally).
Perhaps this sounds a bit banal and simple, but in the end, it is this simple yet so difficult in practice. We are already paying the price for this today, and unfortunately that price will increase exponentially as global warming accelerates.
Therefore, we have no time to lose or biomass to waste.
0 comments on “Biochar: Renewable carbon from biomass for the metallurgical industry”