A little background first
A subsea HVDC power cable is a transmission cable carrying electric power at high voltage over long distances below water. The cables are made of a conductor, which is usually copper or aluminum, the insulation, which is XLPE and some protective screens around the insulation. Cables that withstand a voltage higher than 52 kV are usually equipped with an extruded lead sheath to prevent water ingress inside the insulation. This is a well-proven design but it has some limitations, mostly because of the lead sheath which is costly to apply and reduces the flexibility of the cable. Moreover, the European Union is likely to ban the use of lead in the near future. This means other solutions need to be considered.
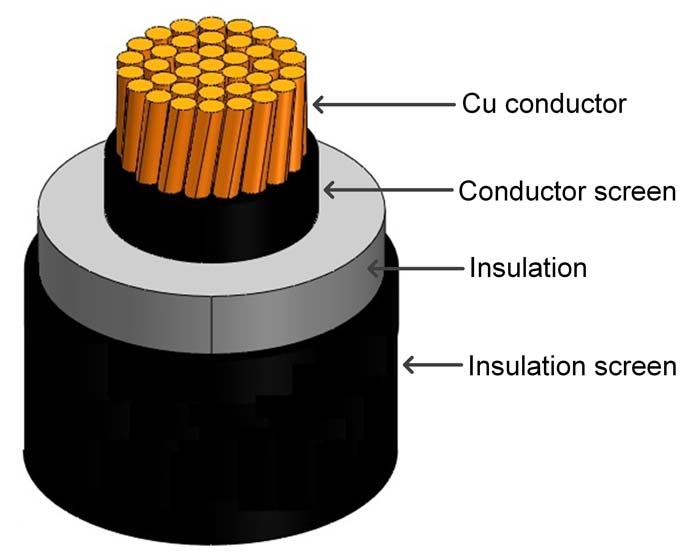
To suggest new designs and therefore reduce the cost of subsea cables, it is vital to understand the effect of different material properties on the long-term ageing of the cables. The use of wet-design high voltage AC power cables (see Figure 1) – meaning with no metallic protective barrier, where water can enter in the cable – is an interesting alternative. These cables are easier to implement and to install than traditional heavier cables. Since they are lighter, longer sections can be transported at once, reducing the overall costs. To sum up, they are cheaper and easier to make. However, over time, water will enter the cable and cause a degradation of the cable insulation which will result in a reduction of its service lifetime. When water can enter the insulation system, several ageing mechanisms can cause a decreased lifetime. The combination of electrical stress, water soluble contaminants and a humidity level above 70% can result in growth of so-called water trees.
What is a water tree?
A water tree is a diffuse, partially conductive 3D plume-like structure, or in other words a dense network of extremely small water-filled channels.
For water treeing to appear at the interface between the semi-conductive layers and the insulation, a contamination by ions is necessary. Since the 1980s, a lot of effort has been made to reduce the concentration of critical ions in the semi-conductive screens by improving the materials that are used and how they are manufactured and handled. Nevertheless, despite the continuous technological progress, water trees still grow in new and modern insulation and the semi-conducting layers can play an important part in the treeing process when ions are present.
What is the purpose of this study?
In Figure 2 we show an example of a vented water tree observed with an optical microscope, growing from the screen inside the insulation. The surface is very smooth and does not seem to be contaminated. There is no apparent anomaly, such as a void for example. So, what caused the growth of this tree at this spot? This is what we are trying to figure out.

The aim of this study is to examine different methodologies to detect the ions responsible for the initiation and growth of water trees in a modern subsea cable insulation by determining the chemical composition in very localized spots near the root of the water tree. If the overall concentration of ions inside the material is close to zero, we want to prove that a high localized concentration can result in the growth of the water trees.
The results
Scanning Electron Microscopy (SEM) analysis was used to examine the interface between the semi-conductive screens and the XLPE insulation in the vicinity of a water tree (Figure 3). However, the trees become indiscernible through SEM as the tree structure dries out during the vacuum process, making it difficult to find specific spots where water trees are located.
Energy Dispersive X-Ray analysis (EDX) is used to determine the chemical composition of the area investigated by SEM (figure 3). The y-axis depicts the number of counts and the x-axis represents the energy of the X-rays. The position of the peaks is used for the identification of the elements and the peak height results in the quantification of each element’s concentration in the sample.
It was found that the concentration in sodium and chlorine observed near the position of a water tree was two times higher than elsewhere, revealing a potential localized higher concentration of salt, leading to the growth of the water trees.
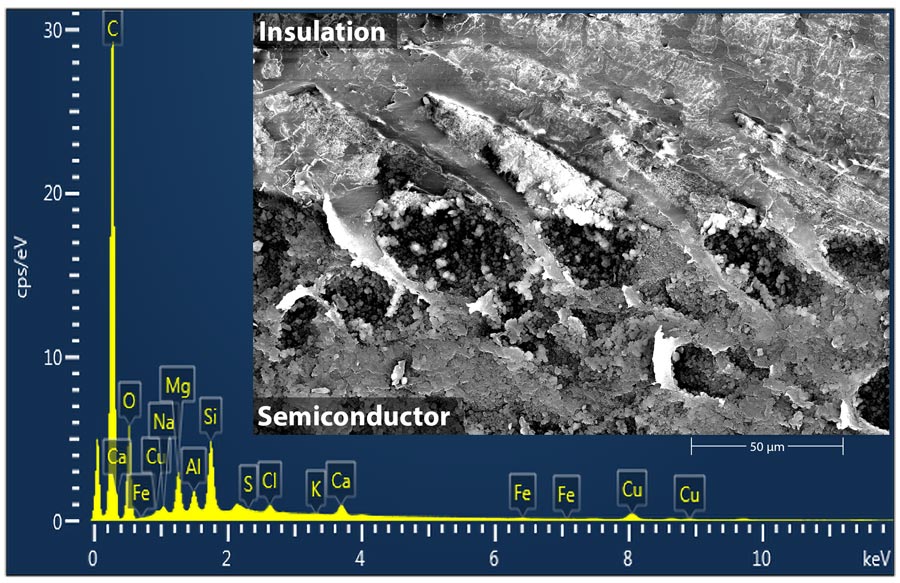
In order to investigate if what was observed with the combination of SEM and EDX was relevant or only a surface (contamination) effect, a focused ion beam (FIB) was used. Gallium ions are bombarded at the surface of the sample in order to mill in depth (ca 50 μm deep), as observed in Figure 4. FIB-milling is an inherently destructive process, as the bombardment of a surface with ions causes atomic sputtering from the surface. The sample is then tilted and the chemical composition of the surface between the insulation and the semiconductor can be investigated by EDX along a straight line as observed in Figure 4. Very simply put, we dug a hole inside our sample to check the composition below the surface.

The EDX spectrum along the line under the surface revealed only carbon and oxygen. No other elements were found. The concentration differences in elements observed at the surface can vary within just a few microns. It is therefore quite possible that the investigated area was too far from the water tree. However, no other element than carbon and oxygen were observed at all under the surface. It is a possibility that the bombarding with gallium has wiped out completely the surface of the other elements and this requires a further investigation.
To conclude
Water trees can grow even in modern HV XLPE cable insulation with significant lengths. Moreover, even though no apparent contaminations are present at the interface, if the contaminant ions responsible for inception of the water trees at the screens are available at the surface, they can be revealed by a simple methodology consisting of examining the surface by SEM combined with EDX.
The results displayed here show that any surface contaminations could dilute the results, making this approach challenging. To overcome this, FIB-milling can be used to exclude contaminations at the surface, detecting ions tens of microns into the sample.
Comments
Hi,
Interesting reading.
You start the article with describing a subsea HVDC cable and later talking about AC, is the results for AC?
It looks like salt can be a source for water treeing but you have not written that in the conclusion, right?
J admire le travail que tu as développé même que pour moi qui ne peut pas tout comprendre est lu avec intérêt ton compte rendu et j’ai pu comprendre le sens de cette recherche
Bravo mon fils je suis fier de toi
Pp