Co-Author: Jørn Kjølaas, SINTEF –
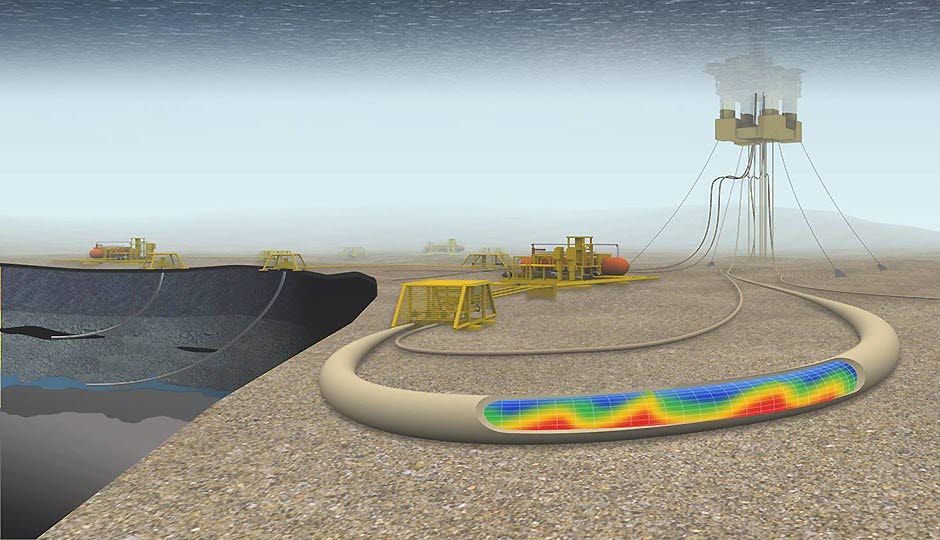
Tieback solutions to existing oil and gas facilities can play a key role for Norway’s ability to meet emission targets while maintaining a competitive industry. However, petroleum production systems often deliver fluids with complex physical chemistry. The innovation project ChemFlow aims to develop new models in the multiphase flow simulator LedaFlow taking the properties of fluids with complex chemistry into account.
Ongoing experimental campaigns in ChemFlow reveal new knowledge that is essential for understanding the impact of chemicals on flow behaviour and improving the accuracy of the prediction models required for cost efficient and safe design and operation of tie-back systems.
Senior Research Scientist Jørn Kjølaas, principal investigator in ChemFlow, preparing experiments in the medium scale flow loop at SINTEF’s Multiphase Flow Laboratory. (Picture SINTEF)
Enabling subsea tiebacks with complex fluid chemistry
The complexity of petroleum production systems arises either from natural surfactants or chemicals added to prevent corrosion or other flow assurance issues. The presence of chemicals/surfactants can change the flow behaviour drastically, potentially causing severe problems such as flow instabilities, separator flooding, poor separation, and foaming. These issues will often lead to production loss, as well as increased emission of greenhouse gases. For example, if the gas contains too much liquid after the separation stage, it will typically have to be flared.
The industry is not equipped to predict problems associated with chemicals and surfactants, as current models can only deal with “ideal” fluid systems. The consequence is that decisions regarding design and operation of petroleum production systems are based on incomplete information and are suboptimal from both an economic and environmental viewpoint. To improve this, ChemFlow will develop new models in LedaFlow, enabling the industry to predict the behaviour of complex fluid systems. Multiphase pipeline flow experiments and fluid characterisation test will be an important basis for the research.
Exploring the impact of chemicals on the flow of production fluids
Several exciting two and three phase experimental campaigns are currently taking place at SINTEF’s multiphase flow laboratories at Tiller. The purpose of the experiments is to investigate the role of surfactants on liquid dominated multiphase flows, and this matter is investigated by adding various amounts of crude oil to the refined oil. The baseline fluid system used in the experiments consists of Exxsol D60 oil, tap water with 3.5% NaCl, and Argon at 11 bara pressure.
Some of the key questions being addressed are:
- How do surfactants affect the rheological behaviour of the fluid system?
- How do surfactants influence the evolution of droplet and bubble size distributions?
- How do surfactants affect the evolution of oil-water and gas-liquid flow regimes?
The picture shows a three-phase flow situation in a pipeline: a water layer with dispersed oil droplets at the bottom, an oil layer, and gas in the top layer (Picture: SINTEF). Two and three-phase flow experiments in ChemFlow are coordinated with experiments conducted in two complementary competence-building projects: KSP SlugFlow (RCN project no 280610) and KSP NexFlow (RCN project no 295035) and builds on the strong knowledge base being established in these projects.
The selected fluid systems are deployed in a flow loop setup with a valve near the inlet. The medium scale flow loop is over 200 meters long, and the flow downstream of the valve is monitored using traversing gamma densitometers measuring density profiles and pressure transducers. Droplet size measurements are also performed at selected locations. Using this instrumentation, we can observe the evolution of the flow along the loop as it approaches equilibrium.
From the preliminary results we have observed that adding crude oil to the fluid system has several implications:
- The flow evolution after the partially choked valve becomes slower.
- The so-called “drag reduction” effect observed at low water fractions, where water droplets dispersed in the oil reduce the flow resistance, is reduced.
- The “oil/water phase inversion point”, where the flow abruptly switches from oil-continuous to water-continuous, takes place at a higher water fraction.
- The flow regime transition between bubbly flow and slug flow is not significantly affected.
Leveraging unique experimental data for advancing LedaFlow
In the coming months the ChemFlow project will analyse the experimental results to build a better understanding of the investigated fluid systems. The outcome will serve as basis for developing new functionality that enables the multiphase flow simulator LedaFlow to predict the impact of complex chemistry on pipeline flow. The flow experiments will also be used to validate the accuracy of new methods for characterizing fluid systems with chemicals/surfactants using simple setups that we plan to develop in the project.
The innovation project ChemFlow is owned by LedaFlow Technologies DA and is supported by the Research Council of Norway (project number 314165). Project partners are TotalEnergies, ConocoPhillips, Lundin, Kongsberg Digital and SINTEF.
0 comments on “Multiphase pipeline flow experiments for enabling tieback solutions”