Upcoming industry 4.0
The manufacturing sector is on the verge of a major change toward the so-called Industry 4.0. This revolution takes its roots in the digitalization of the value chain from concept, design, to production and recycling. It is associated with large increases in volumes of data generated, analysed and retrofitted into the system.
For example, in the production step, increasing integration of sensors in equipment and tools generate statistical data that could be treated by Big Data algorithms. However, the key for competitive industry is innovative products and many innovative products are enabled only by newly developed high-performance materials. Innovation in material science is the result of three factors:
- theoretical understanding of the material physic
- ability to characterize and model material state and properties
- exploitation of that knowledge.
SINTEF is working on a new approach to facilitate the exploitation of the characterization results and enhance communication in material development by using a web-based application.
Complex material description
For aluminium alloys, three parameters are determining the material performance:
- the composition
- the particles
- the grain structure
To quantify these parameters and the associated properties, various microscopy techniques, mechanical testing, and resistivity measurements are applied. In addition, numerical models are used to investigate material from atoms to component scales. These observations generate a large amount of data that must be communicated in interdisciplinary research teams. For example, in Competence Building project AMPERE lead by NTNU, the aim is to study the effect of high temperature exposition of aluminium alloys on strength (car components) and electrical conductivity (sub-sea cables). To study that problem, the project generates microscope images, strength measurement and electrical conductivity measurements as well as numerical simulations.
AMPERE facts:
The aim of the KPN project AMPERE (2015 – 2020, 15.8 MNOK budget) is to establish a scientific basis that allows designing alloys and processing schedules to yield optimum combination of various mechanical properties and electrical conductivity at elevated temperatures (in-service conditions), and a methodology that can be used to support related mechanical product design. This will be achieved through enhanced fundamental understanding of the correlation of material microstructure, mechanical properties and electrical conductivity and the influence of elevated temperature and time.
The research partners are NTNU (project host) and SINTEF and the project is supported by the Norwegian Research Council and will be carried out in collaboration with both metal producers and metal users, i.e. Norsk Hydro, SAPA, Nexans, Raufoss Technology and Gränges.
Material Database
Until now, this data is independently stored and exchange through memo or presentations. The traceability is often difficult and comparison is sometimes problematic due to the lack of information. In addition, over time, large number of tests and measurements have been performed and the way data is stored (for example a plot in a journal paper) is inappropriate for retrieving and exploiting that information. Therefore, a new solution is required to better retrieve, compare and analyse the material data.
Building a new solution
In that perspective, SINTEF has started to develop a Material Database. The main idea is to store all the required information to understand, analyse and reproduce an experiment or simulation. The solution is relying on a data server that can be reached through a web application. It will combine three set of tools:
- registering of new tests
- search engine
- analysis tools
In the first stage, the focus was primarily on mechanical testing. The advantage is that mechanical tests are usually carried out based on well-defined procedures defined by international standards. However, AMPERE project has other needs.
Therefore, based on SINTEF material database platform, a new set of data structure for the relevant observation have been defined to handle microstructure and properties evolution during temperature cycles. In collaboration with the research team making the measurements, a list of parameters and results have been identified allowing for a precise description of the experimental test or simulation. Reports and presentations are still stored in the database but, in addition, raw measurement data, microscope images, procedures, equipment set-up, history of the material are stored. It facilitates the exchange of data, as the format is generic, and enables anyone in the project to access directly the original results.
Moreover, NTNU and SINTEF are working in many projects were open data is generated. The Material Database would then offer a unique platform to share data between projects to avoid duplication of work.
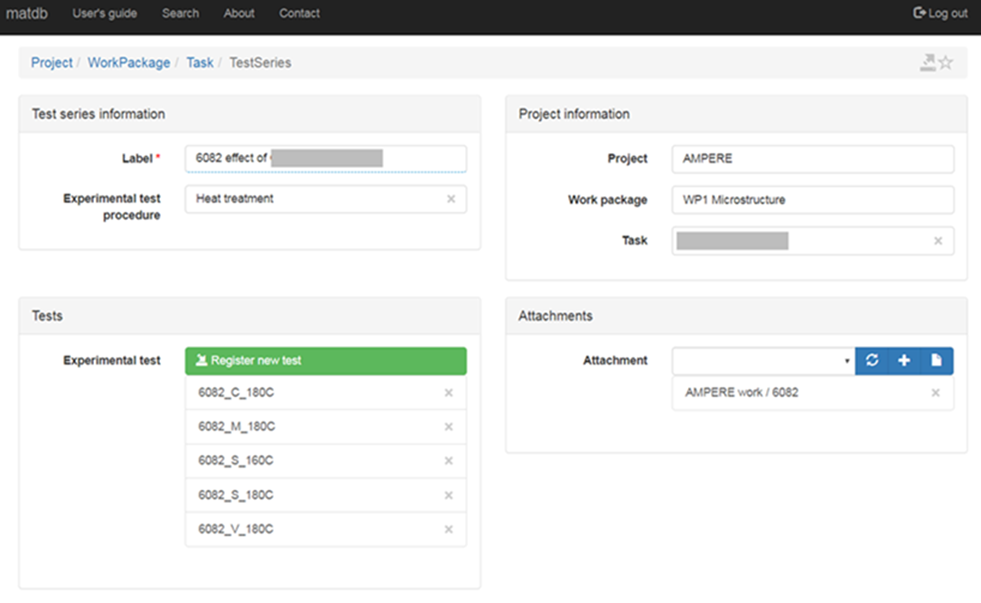
Future application to alloy and process development
The final goal of AMPERE is to provide industrial partners a framework to develop new alloys and products. The efficient storage of the information generated during research activities is an important initial step. Based on the well-defined and easily accessible data stored in the new material database, a set of numerical models will be developed, calibrated and validated. These models could be used to predict the effect of process parameters on the material properties and help design innovative alloys. In addition, the framework will include an optimization tool connecting the different models and automatically optimizing the alloy composition to reach higher performance.
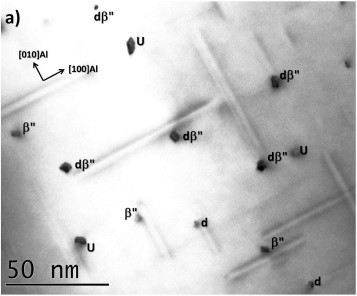
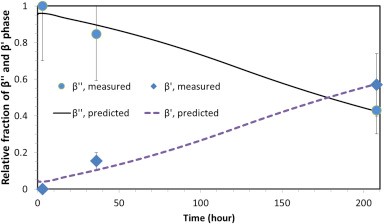
For the industry, access to this framework is important to reach new market or strengthen their positions. For example, by traditional approaches, the development of Al alloys is time consuming and expensive. Reliable simulation tools like the ones to be developed in AMPERE can significantly reduce the time span and cost from alloy design to mass production. For component manufacturing, the raw material has a strong effect on the properties of the final product. It is expected that the results from AMPERE will help in optimizing microstructure and heat treatments to fully exploit the potential of newly developed alloys.
AMPERE project will build some key elements to implement a virtual production line along the value chain and offer well calibrated models that can be applied for exploiting sensors data when integrated in the production machines.
Comments
No comments yet. Be the first to comment!