Green hydrogen is produced by a process called electrolysis where renewable electricity, e.g., from wind turbines or solar cells, is combined with water to produce hydrogen gas. The hydrogen gas can then be stored, transported, and used on demand in a fuel cell to produce electricity where the only by-product is water vapour.
It’s easy to see how the idea of a zero-emission fuel created from renewable resources with unlimited supplies, i.e., sunshine/wind and water, has generated so much hype recently. So, why hasn’t the entire world’s energy infrastructure adopted green hydrogen as a replacement for fossil fuels? The short answer is cost. The production cost of green hydrogen is simply too high to be competitive with conventional energy sources, for now. There are big costs associated with renewable electricity and for the electrolysers/fuel cells.
Expensive materials
Electrolysers and fuel cells are complicated technologies that currently rely on expensive components, specifically precious metal catalysts, e.g., platinum and iridium, and fluorinated ion-exchange membranes. The International Renewable Energy Agency (IRENA) performed a cost breakdown analysis for a typical proton exchange membrane (PEM) electrolyser system and found that the catalysts and membrane combine to account for 24% of the total electrolyser stack costs.
Developing non-toxic, safe-by-design membranes
The ion-exchange membranes are a particularly interesting candidate for potential cost reduction as all commercially available PEM electrolyser and fuel cell systems currently employ a single type of membrane, broadly referred to as perfluorinated sulfonic acid (PFSA) membranes. These membranes are synthesized using expensive fluorine chemistry and, as a result, they represent a significant portion of the stack cost, e.g., 5% of the total electrolyser stack cost in the example below. In PEM fuel cells, the DoE performed a cost analysis of [1]Mirai fuel cell passenger vehicle and found that the PFSA membrane accounted for 14% – 19% of total fuel cell stack cost depending on the number of stacks produced per year.[2]
In addition to the high cost of PFSA-membranes, the use of these fluorinated polymers presents serious health and environmental concerns as their production, degradation, and disposal results in the release of hazardous perfluorinated compounds that have been shown to accumulate in the environment and are toxic to living organisms.[3] [4] Developing non-toxic, safe-by-design membranes is therefore crucial to ensure that renewable technologies that rely on proton exchange membranes remain an environmentally friendly solution.
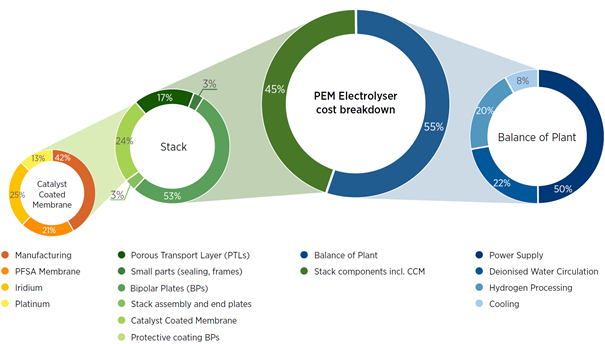
Two strategies
The stack is the heart and soul of all electrolyser and fuel cell technologies. This is where the main electrochemical processes take place and where the overall performance and lifetime of the system will be determined. It is therefore crucial to investigate new stack materials that can provide cost savings while also meeting performance, lifetime, and circularity targets.
In general, there are two strategies when it comes to material development of electrolyser and fuel cell stack components.
The first strategy is to find new materials that can directly replace the legacy materials used in proton exchange membrane electrolysers and fuel cells. Because PEM electrolysers and fuel cells are mature technologies that are seeing real-world implementation now, new materials for use in PEM technologies have the advantage of rapid market uptake and implementation for immediate cost reduction benefits. The difficulty in this approach lies in the fact that PEM technologies operate in an acidic environment and therefore require corrosion resistant components. Materials that are inexpensive, stable in the acidic operating environment, and show high performance are very difficult to find.
The second strategy is to change the operating environment of the electrolyser/fuel cell so that it is no longer operating in an acidic environment. In this strategy, electrolyser and fuel cell technologies are operated under alkaline conditions, opening up the possibility to use entirely new classes of materials that have distinct advantages and disadvantages over the acidic PEM system. These systems operating under alkaline conditions are referred to as anion exchange membrane (AEM) electrolysers and fuel cells. AEM-based systems can therefore be designed using less expensive catalyst (e.g., Ni vs. Pt) and component (e.g., stainless steel vs. titanium) materials, while maintaining the advantages of a membrane-based system like rapid responsiveness for dynamic operation and high selectivity. The potential use of AEMs across a wide range of sustainable energy technologies has resulted in a surge of interest and commercialization of several new AEM materials. Despite this, however, most anion exchange membranes remain plagued by either low stability in an alkaline environment or low ionic conductivities. To overcome these challenges, innovative polymer membrane designs are required where careful consideration of the chemical structure of both the polymer backbone and the ion-conducting functional group is required.
LOCOMOTION project – replace PFSA membranes in PEM fuel cells
SINTEF has recently been awarded funding through the Era.NET MarTERA programme to explore the development of hydrocarbon block copolymers to replace PFSA membranes in PEM fuel cells. The project is titled “Highly durable, low-cost membrane electrode assemblies for maritime fuel cell applications (LOCOMOTION)”. More information about the project can be found here.
This potential solution aims to replace the PFSA-membrane in PEM technologies with hydrocarbon-based proton exchange membranes (HC-PEMs). These non-fluorinated membranes can be synthesised from inexpensive precursors to offer significant cost savings and reduced environmental concerns. The main drawback of HC-PEMs is that they require a much greater density of sulfonic acid groups to achieve similar proton conductivities as PFSA-based membranes. This leads to greater water uptake and excessive swelling which ultimately leads to reduced mechanical stability of HC membranes. LOCOMOTION proposes the use of a block copolymer strategy to limit the water uptake and swelling of the hydrocarbon PEM while maintaining good ionic conductivity. As the ion, liquid, and gas transport properties of the membrane are largely attributed to the hydrophilic blocks (i.e., with sulfonic acid groups) and the mechanical, chemical, and thermal stability of the resulting membrane is determined by the hydrophobic blocks (i.e., no sulfonic acid groups), the resulting membrane properties can be tuned by varying the fraction of hydrophilic/hydrophobic blocks. Additionally, microphase separation and connectivity of the ionic domains, which are important to promote good ionic conductivity, can be tuned by varying the individual block lengths.
The expected results of our research findings will have a direct impact in the fields of PEMFC component development and zero-emission transport. Concerning the development of next-generation proton exchange membranes, greater insight surrounding the influence of hydrocarbon block copolymer structure on the nanoscale phase separation will be essential in overcoming the limitations of non-fluorinated membranes, namely achieving sufficiently high proton conductivities while avoiding excessive water uptake and swelling. The results from the LOCOMOTION project will contribute directly to reducing the performance gap between hydrocarbon- and PFSA-based PEMs, highlighting the viability of environmentally friendly and inexpensive non-fluorinated alternatives. A major outcome of this project will be the potential for a step-wise change in the development of proton exchange membranes with the potential to disrupt the current landscape that relies exclusively on perfluorinated membranes that are expensive to synthesise and pose health/environmental concerns.

COFFEE project – innovative anion exchange membranes
On the AEM side, SINTEF has been awarded funding through the m-era.net programme to explore the development of innovative anion exchange membranes. The project is titled “Cationic Covalent Organic Frameworks as Anion Exchange Membranes for Electrochemical Energy Applications (COFFEE)”. More information about the project can be found here.
This innovative project employs a bottom-up approach to membrane design that aims to overhaul the traditional AEM designs that rely exclusively on linear cationic polymers and instead develop an entirely new class of membranes based on covalent organic frameworks (COFs). COFs are cyclic molecules that undergo self-assembly to form highly ordered nanochannels. The main idea behind the COFFEE project is to take advantage of the supramolecular COF structure to enable ultra-fast ion transport through the COF network by functionalizing the inside of the COFs with anion conducting groups. These highly ordered COF structures will then be embedded in a polymer matrix to form membranes with an optimal balance of ionic conductivity and mechanical stability.
The successful incorporation of cationic COFs into a polymer matrix will pave the way for the first ever demonstration of COF-based AEMs in electrochemical energy conversion/storage devices. The breakthrough outcomes envisioned by developing an entirely new class of anion exchange membrane will push the development of AEM-based electrochemical energy conversion and storage technologies closer to commercial viability. The COFFEE project will therefore be contributing directly to ensure the future success of sustainable energy supply within Europe. The successful commercialization of anion exchange membrane water electrolysers and fuel cells has the potential to decrease the production costs of green hydrogen, thereby facilitating the widespread adoption of renewable fuels and directly supporting the European strategic policy targets for greenhouse gas emission reduction.
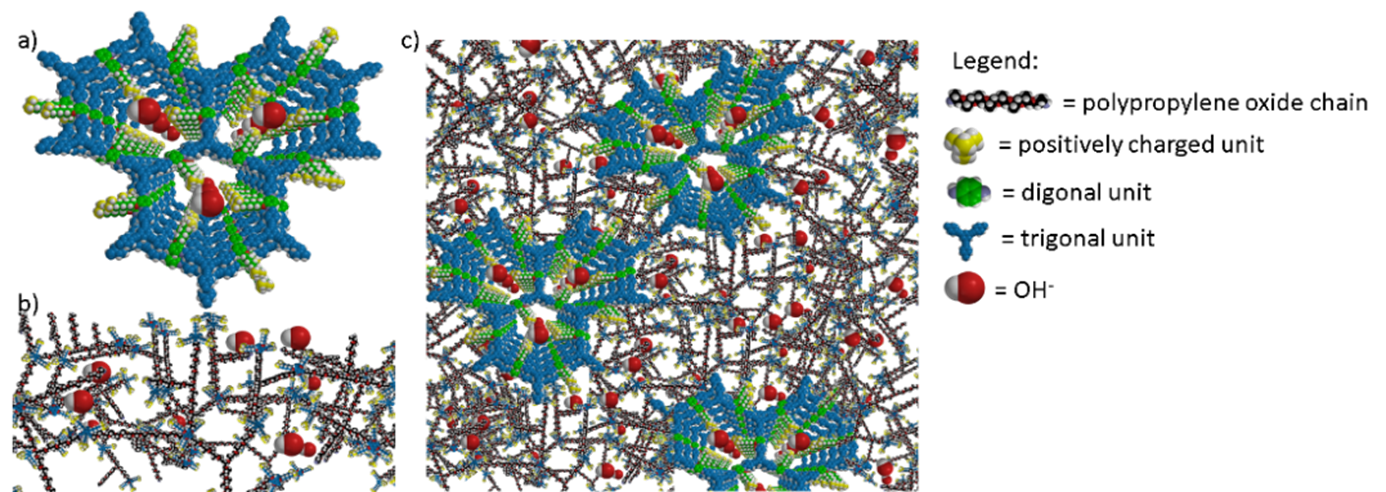
Aims to be in the forefront of the green hydrogen revolution
The current production cost of green hydrogen is a major barrier towards mass adoption. Research efforts towards innovative electrolyser and fuel cell components represents one of the pathways towards achieving low-cost electrolyser and fuel cell systems. More specifically, the development of novel ion-exchange membrane presents an opportunity for increased cost savings and reduced environmental concerns. SINTEF is currently active in developing innovative membranes for both PEM and AEM technologies in hopes of bringing these solutions to the forefront of the green hydrogen revolution.
[2] US DoE report (2018), Mass Production Cost Estimation of Direct H2 PEM Fuel Cell Systems for Transportation Applications[3] Feng, M.; Wang, Z. et al. Sci. Rep.2015, 5, 9859.[4] https://www.eea.europa.eu/themes/human/chemicals/emerging-chemical-risks-in-europe
Comments
No comments yet. Be the first to comment!