Co-authors: Rune H. Gaarder (SINTEF), Jon Hermansen (BEWI Biobe) and Olav Larsen (BEWI Biobe) –
Can the use of plastics (polymeric materials) in components in CO2 capturing plants reduce the cost per captured ton of CO2? In this blog we discuss some pros and cons of plastics regarding their usage in the absorber and desorber columns in CO2 capture plants.
CO2 is emitted from power generation and industrial processes, such as Norcem’s cement factory in Brevik (Norway). In the fight against climate change, the CO2 should be captured and stored safely, or used as a raw material. Technology for capturing CO2 from exhaust gases has been developed for many years. However, the cost per captured tonne of CO2 is still very high, and many studies have tried to reduce the costs and identify the most cost-effective applications.
[blue_box]
CO2 capture with amine-based solvents and the role of structured packing
- In CO2 capture, transport and storage (CCS), it is estimated that more than half of the cost is related to the CO2 capture. This cost can be divided into installation (investment) costs and operation costs. Also note that the operation requires energy. This means that if the CO2 capture is powered by a CO2 emitting process, there is an energy penalty which must be considered. On the other hand, the cost of CO2 capture can be reduced if the site (for example a cement factory) has excess heat and low-pressure steam that can be used in the capturing process.
- The most mature technology for capturing CO2 from exhaust gases is based on chemical absorption of CO2 molecules into an amine-based liquid solvent. So-called structured packing is the preferred gas-liquid contacting medium, due to their large mass transfer area and low pressure drop. In the absorber column of a CO2 capture plant, the structured packing is a passive meeting place for the exhaust gas (with CO2) and the solvent which absorbs the CO2. Structured packing is also used in the desorber column, where the CO2 is stripped from the solvent.
- The packing in the absorber column must have a large effective surface area for CO2 absorption (to have a high capturing efficiency), but at the same time the pressure drop associated with pumping the exhaust gas through the column should not be too high (to avoid high operation costs). The absorber column internals, especially the structured packing, contribute significantly to the installation cost of the plant. The operating cost of the absorber column is dominated by the energy cost to blow exhaust gas through the column.
- Some of the most common amine-based solvents degrade chemically in the capturing plant, and they need to be replaced after a certain time. It has been shown that contact with metals (certain metal ions) contributes strongly to this degradation. Degradation of solvents has been the topic of many studies, such as the Horizon 2020 project LAUNCH.
[/blue_box]
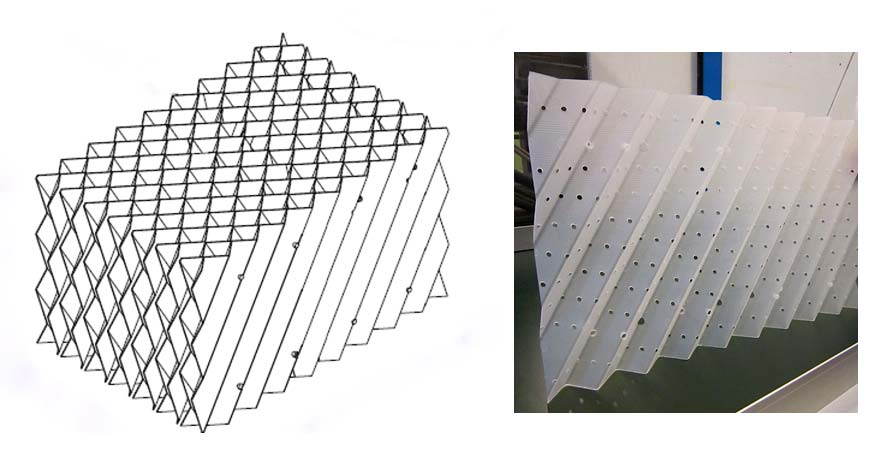
Plastics in “structured packing”
The FANGST project focuses on the use of plastics in structured packing for CO2 absorption and desorption, but the project also considers plastics and composites for other components in CO2 capturing plants. The project performs research on the lifetime of plastics and composites when exposed to amine-based solvents. There are also activities on optimizing the geometries and surface properties of structured packing, aiming at increasing its CO2 capturing efficiency for a given pressure drop.
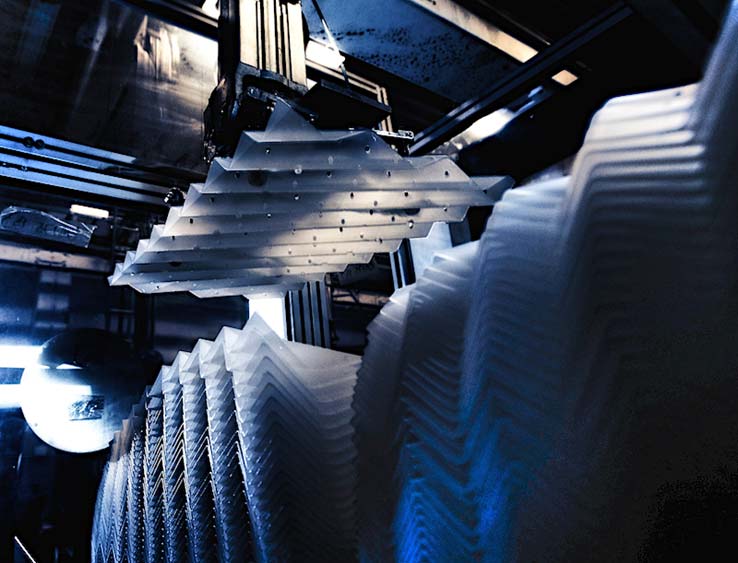
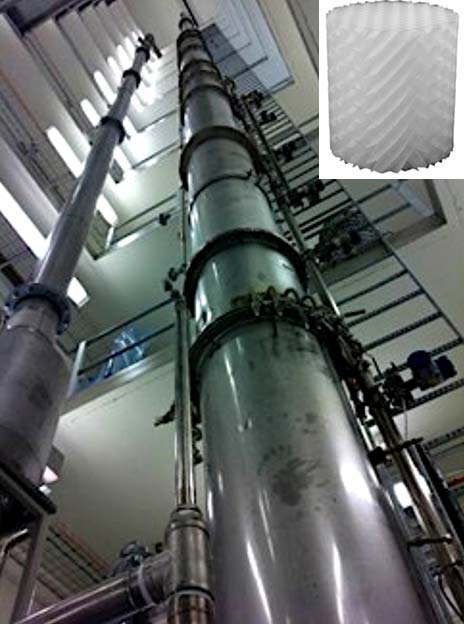
Today, plants for amine-based CO2 capture typically use packing of stainless steel, but there are also polymer-based materials (plastics) with good chemical resistance towards amine-based solvents, as we have demonstrated in the FANGST project.
Packing made of plastics, using mass-production methods such as injection moulding, can reduce the investment costs compared to packing made of stainless steel. Recycled plastics can also be used. Regarding operation costs the picture is more complicated. The pros and cons of packing made of plastics vs. stainless steel can be summarized as follows:
- The cost per absorber column volume: For a structured packing with a certain specific surface area (i.e. packing surface area per absorber column volume), the cost of a packing in plastics is substantially lower than for one in stainless steel. Plastics packing also has lower weight, which reduces transport and mounting costs. Regarding transport costs we assume that the volumes are the same for plastics and steel packing. Note that structured packing plates are typically stacked effectively during transport.
- The lifetime of the solvent: As mentioned in the fact box, metal surfaces can accelerate the degradation of the solvents. Hence, the use of plastics can extend the lifetime of the solvents, thereby reducing the operation costs. Plastics packing, and other components in contact with the solvent, are also less prone to fouling, and corrosion is not a problem. It should be noted that some types of CO2 absorbing solvents are less prone to this metal-induced degradation, but these solvents have other drawbacks.
- The efficiency of the packing: As mentioned in the fact box, the packing in the absorber column must have a large effective surface area for CO2 absorption – a large area covered by a flowing solvent “film”. Metals have some more freedom in making packing with a large nominal surface area, especially so-called wire gauze metal packing. However, the main limitation of plastics packing is perhaps to achieve a high effective surface area (for a given nominal surface area). Packing materials should enable good wetting and liquid film forming on the surface in order to achieve an efficient CO2 capture process – here surface tension is an important parameter when selecting solvent-packing systems. Typical plastics materials are hydrophobic while the solvent is hydrophilic. Hence, the solvent will not wet a plastic surface as well as a metal surface. Therefore, the solvent film on the packing will cover a smaller area on a plastic packing. This means that the area available for CO2 absorption will be smaller. However, we are looking into mitigating factors such as material modifications and surface structures/textures that can improve the wetting of plastics packing, and also improve the mixing between solvent and CO2. In principle, an absorber column with plastics packing can be extended to have the same capturing capacity as a metal packing, but this will lead to a higher pressure drop for the exhaust gas pumped through the column.
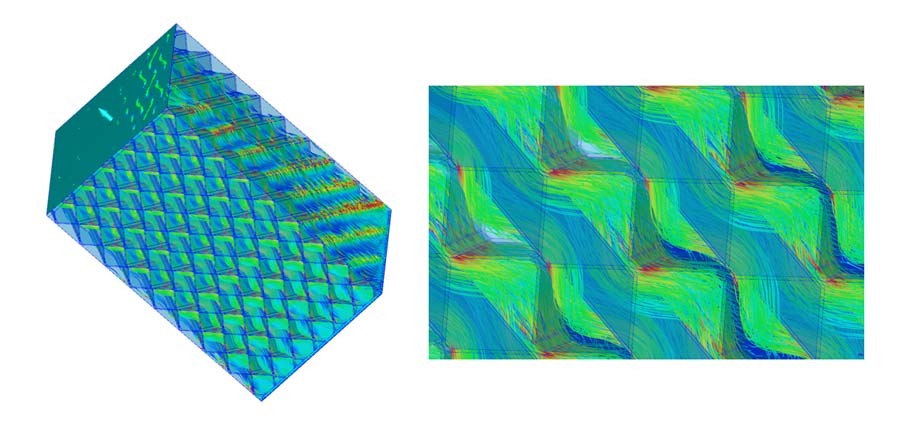
In summary, there are both pros and cons of plastics packing in CO2 capture plants. The relative performance of a plastic material vs. stainless steel depends on the details of the plant, and whether it is on the drawing board or already in operation. Furthermore, there are R&D activities on plastics packing that may improve its efficiency in the future. Research on new solvents that are less chemically aggressive may also open for even more types of plastics.
Finally, it can be mentioned that SINTEF has initiated an R&D project on the use of polymeric materials in the CO2 transport chain (CO2 EPOC).
Comments
No comments yet. Be the first to comment!