The electrical insulation system is “the heart” of every electric power component. If the system suffers from a catastrophic failure, the main function of the component is lost and repair or replacement (if possible) is needed.
Recent research has demonstrated the significant potential offered by the use of nanocomposites to increase the reliability and endurance of electrical insulation systems.
SINTEF Energy Research has extensive expertise in the fundamentals and practical application of insulation systems for a variety of electric power devices such as:
- power transformers
- rotating machines
- cable systems
- overhead lines
- switchgears
- power electronics
We carry out comprehensive research and development projects for utility companies and the electric power and subsea sectors.
Why do we need nanocomposites in electrical power devices?
Micro-fillers have been used in electrical devices for many years. They are essential for high reliability maintenance in electrical components, for example by limiting the thermal expansion of the composite to levels closer to those of the metal electrodes. However, the introduction of micro-fillers can significantly reduce the electrical withstand voltage of the material, and their impact is commonly like that of contaminants in the electrical insulation.
Nanocomposites exhibit significantly different electrical properties (e.g. conductivity and electrical breakdown stress) compared with conventional composites.
The nanofillers used in electrical insulation systems typically include nanoclays, metal oxides such as AlO2, TiO2 and …, non-metal oxides such as SiO2, phytosilicates and …, and nitrides such as boron nitride, alumina nitride and ….
Nanocomposites has potential to change design of future power components
In most cases, well-dispersed nanofillers have no detrimental effect on electrical properties because the inhomogeneities they represent are too small to have any significant effect on local electric field distribution.
This is why the introduction of nanocomposites has the potential to introduce large changes to the design of future power components and the conditions under which they can be used.
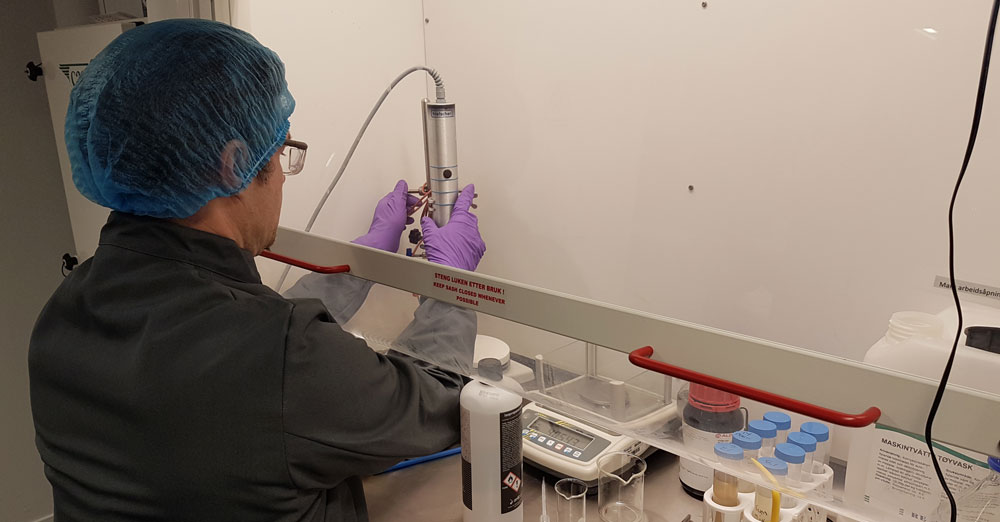
Due to their high surface energy, nanoparticles are prone to aggregation unless adequate precautions are taken. For this reason, the disaggregation of nanoparticle agglomerates before or during the manufacture of composites is key to achieving effective filler dispersion.
This issue represents an important obstacle both in the laboratory and, not least, during the industrial manufacture of nanocomposites. In a composite with poor nanofiller dispersion, the agglomerates introduce inhomogeneities that act as contaminants in electrical insulation systems. Furthermore, the interfacial area between the nanoparticles and the polymer will be significantly reduced. The resulting material will exhibit gradients in a variety of electrical and mechanical properties, which will be detrimental to its performance.
SINTEF Energy Research has established a new research laboratory for the synthesis and investigation of dispersions of nanoparticles in solution, prior to their incorporation into the electrical insulation in high-quality test objects.
Such facilities must be located close to the laboratory where the electrical test objects are manufactured. Time is crucial if the dispersion of nanoparticles is to be used in the casting and production of test objects for electrical testing. A long shelf-life of the liquid dispersion is not crucial due its quick incorporation in a solid epoxy, which freezes the particles in the matrix. Good dispersion can thus be maintained if it first survives the casting process.
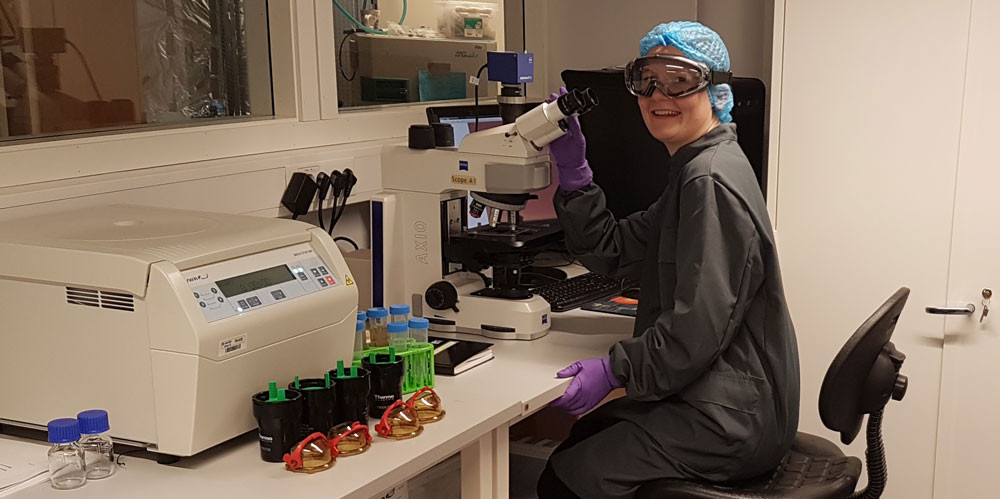
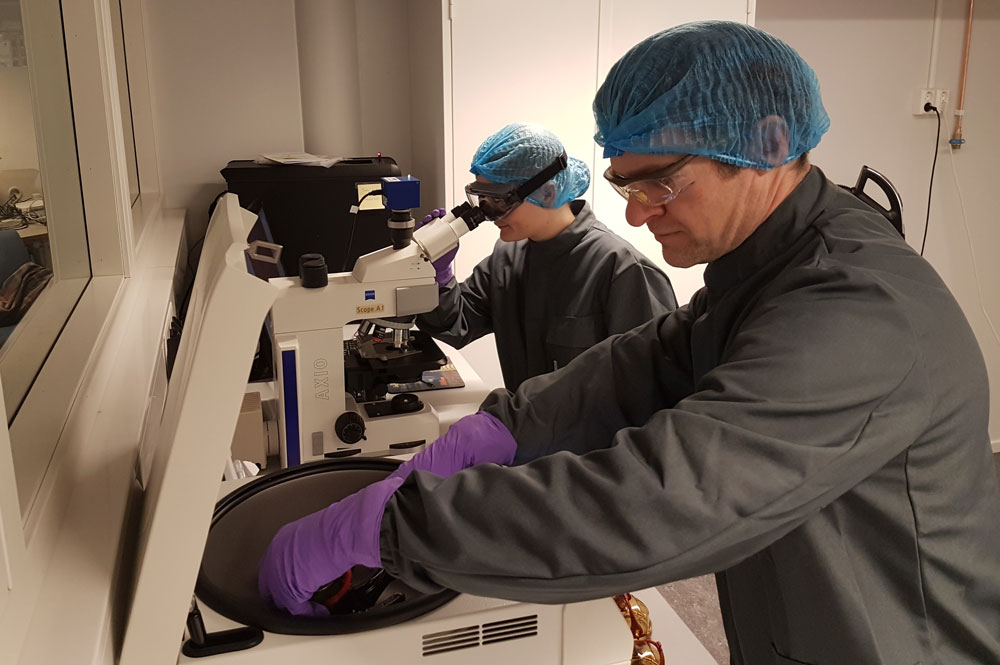
Safety measures
Nanomaterials are commonly made of compounds that we find in our everyday surroundings. As such it is easy to think that exposure poses no risk. However, nanoparticles may exhibit dramatically different properties from those of larger particles made of the same material. This is due to the very large surface area per weight and small size of nanoparticles, which enables them to penetrate the deepest parts of the lungs. It is thought that nanoparticles in the form of dry dust or sprayed aerosols may represent a health hazard and, for this reason, it is important to minimise exposure.
Some nanoparticles are probably harmless in normal exposure dosages, but until more knowledge has been obtained, and standards developed to guide safety decisions, nanomaterials should be handled in the same way as hazardous chemicals.
To limit the number of people exposed to nanomaterials, only qualified personnel are permitted in the laboratory while nanoparticles are being handled.
Nanoparticles are handled using a single fume hood equipped with a HEPA filter. A Nilfisk vacuum cleaner, equipped with a HEPA-14 filter and able to trap most nanoparticles, has also been purchased.
All researchers working with nanomaterials must wear personal protective equipment such as:
- A special lab coat that must be buttoned to the chin
- Cleanroom gloves (two layers)
- Hairnet
- Gas mask with particle filter
- Sealed safety goggles
- Beard net (if necessary)
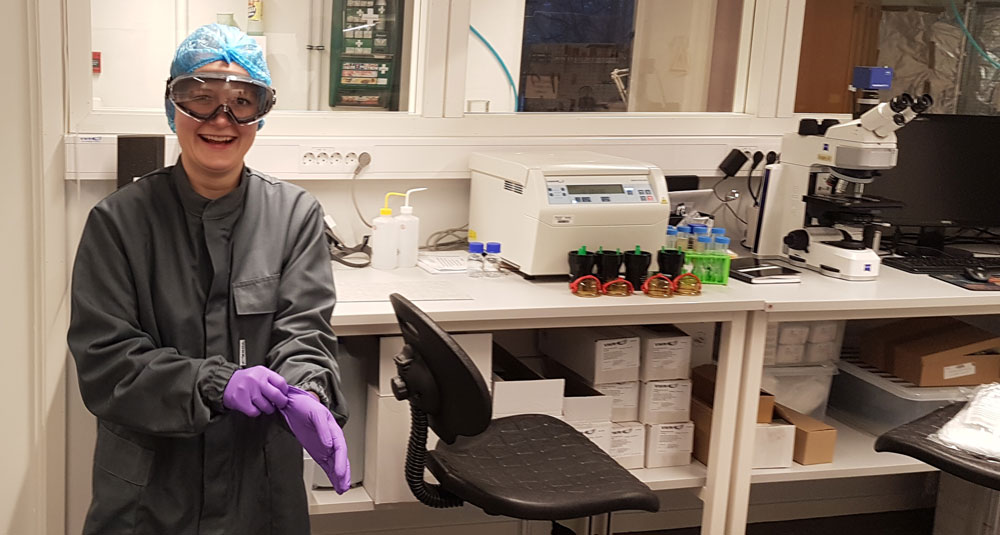
Comments
No comments yet. Be the first to comment!