CO2 injection is one critical step of the Carbon Capture and Storage (CCS) value chain: it is when the carbon dioxide is pumped in the formation to be permanently stored. Injection technology has come a long way, but many questions on the process remain open.
“When we consider the scale of the energy and climate challenge, the critical importance of carbon capture is inescapable” – Dr Fatih Birol, IEA Executive Director
To picture CO2 injection, imagine putting a straw in a bottle full of sand and pouring water inside the straw. The sand quickly absorbs the water. Now imagine the water is cold enough that it could turn to ice in the process, cracking the bottle.
The CO2 injection process is analogous: CO2 is transported as a pressurised liquid (common transport conditions are about -25C and 20 bar). It is then pumped before being warmed up and injected deep into an underground formation (typically 2000 meters or more). To know how much heat to add, it is crucial to know as accurately as possible the CO2 temperature and pressure profile during the whole injection process, to avoid formation damages.
CO2 captured from different industrial processes comes with various impurities and must be purified before injection to prevent corrosion, in a process that drives the cost of capture. An accurate determination of how clean the CO2 must be for a safe injection could reduce the CCS cost considerably.
To answer these questions and more, the DeFACTO project has built a 90 meters underground test facility for CO2 flow assurance and injection inside the NTNU Campus!
Having the facility so close to the researchers is a considerable advantage: it gives the possibility to execute experiments with short notice and train adequately skilled researchers in the field of CCS.
About the DeFacto rig
To deal with the temperature challenges mentioned above, DeFACTO allows control of both pressure and temperature of the injected CO2, granting accurate monitoring of the pressure profile downhole for different realistic liquid/gaseous mass fractions at the injection head.
Furthermore, the design is performed to enable the execution of transients such as shut-in and depressurization tests. The operators routinely perform shut-ins and depressurizations for formation characterization, maintenance, and testing of valves and equipment. Transient operations are cost drivers because they often determine the equipment design parameters due to the extreme temperatures and pressures obtained compared to standard processes.
Another goal of the experiments is to improve insight into the interaction between CO2 and (reservoir) water, with possible hydrate and ice formation during sudden depressurisation events.
Simulation tools such as LedaFlow, OLGA, and CO2 DYNAMICS will be benchmarked and validated against selected experiments.
The results of the experiments performed with this facility will provide valuable data to verify CO2 injection models with impurities, an essential stepping stone towards the practical realisation of CCS. The facility further strengthens SINTEF’s experimental capabilities in the CCS realm, and many more exciting applications of the rig are to be expected.
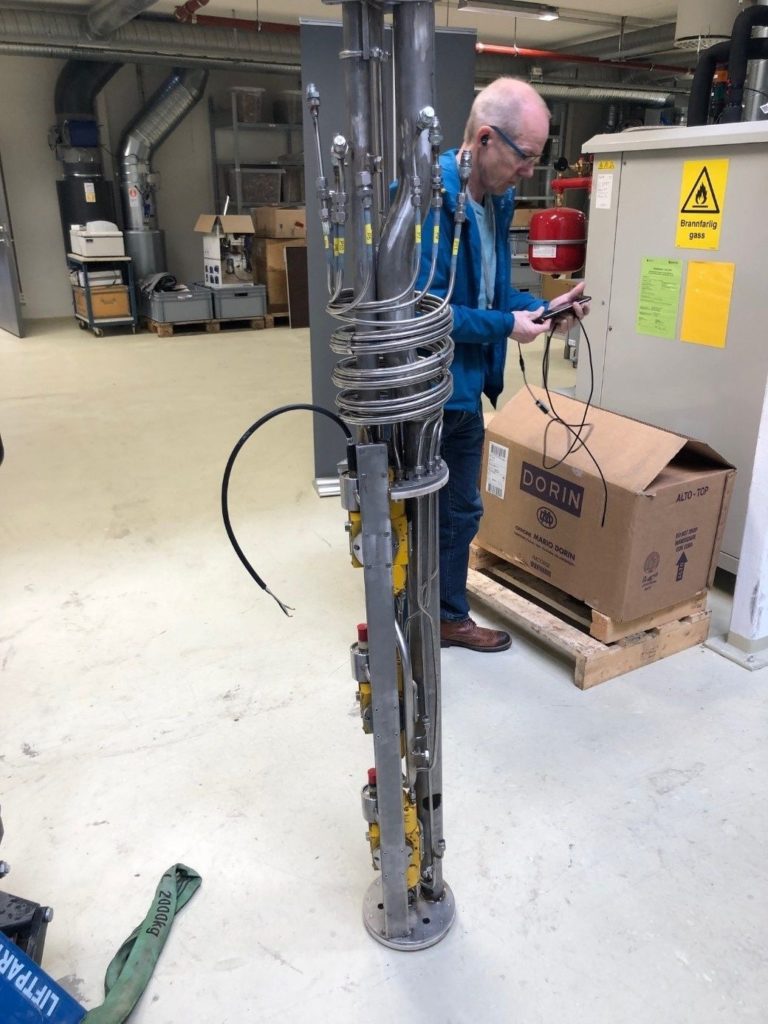
There is art in the process
The facility consists of a 139 meters long horizontal loop for CO2 conditioning (used to adjust CO2 temperature, pressure, and exact composition, as well as the liquid to gas ratio at injection), connected to a 90 meters deep u-tube with legs of different diameter (16- and 32-mm ID). At the bottom of the U-tube, two actuated valves allow the complete closure of each tube. A third valve enables the injection of water at the bottom of the tube from a 10mm ID water injection line to investigate hydrate formation. The 90 meters’ depth allows CO2 phase transition (gas to liquid) to take place in the tubes, which is the case in most CO2 injection projects.
The U-bend at the bottom of the well allows a total pipeline length close to 180m (50% upwards and 50 % downwards). Besides, the different internal diameters used for the two vertical pipelines allow testing in two different flow directions. Consequently, the influence of the tube diameter can be directly investigated in depressurisation experiments.
The tubes are surrounded by a heat transfer fluid (ethanol 70%), which can be heated or cooled between 5°C and 30°C to achieve relevant and repeatable test conditions independent from the ambient temperature at the site. High-frequency response pressure and temperature sensors are placed along the vertical pipelines to record P/T values during the test campaigns.
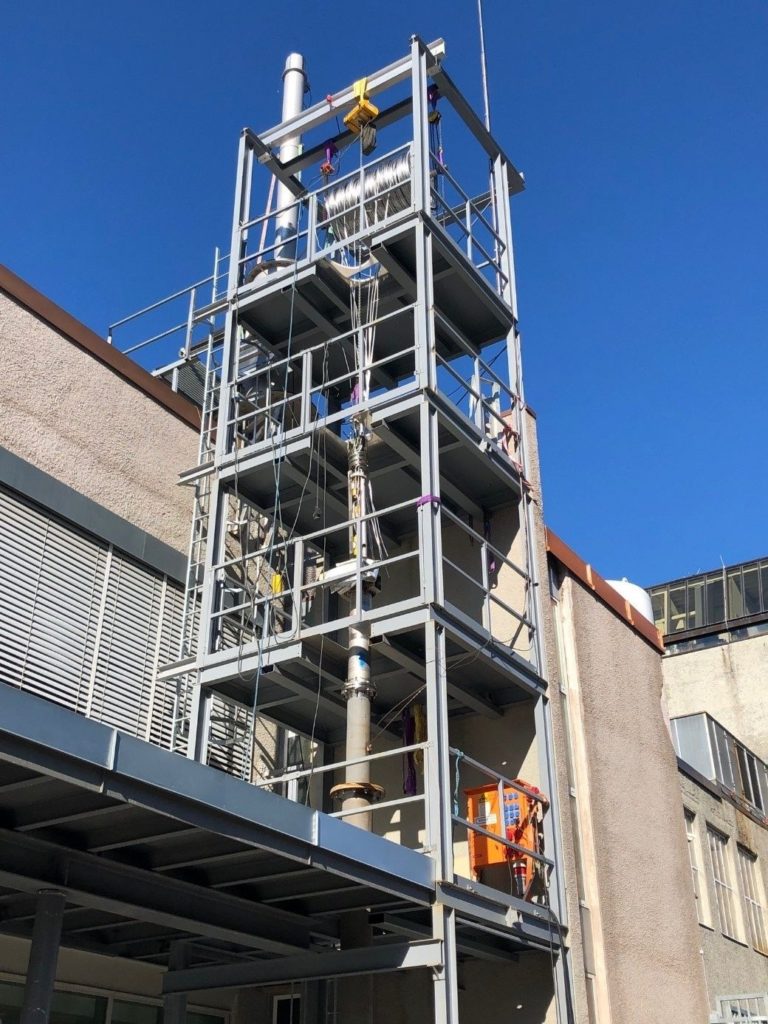
To sum up – over 140 high-frequency sensors, more than a km of cables, more than 10 tubes and 100 wires squeezed in a casing with a diameter of just 20cm. Quite an R&D feat in itself!
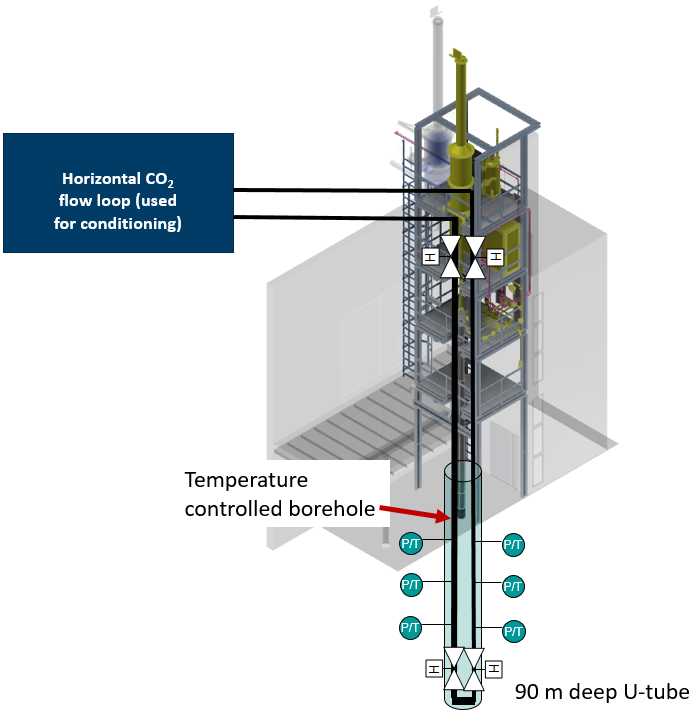
With the delivery around the corner (expected in summer 2020), the project team is in for a hectic ride. We are looking forward to the months ahead of us. We will keep you updated!
This project is partially funded by ECCSEL, Gassnova, Equinor and Total.
Comments
No comments yet. Be the first to comment!