Today, heat exchanger design and possibilities are limited by current production processes. But what new potential could be realised if heat exchanger design and manufacturing were made free from current production methods and constraints? Additive manufacturing of heat exchangers might provide this freedom.
Additive manufacturing of heat exchangers – technical problems
In a new project, HighEx, SINTEF researchers team up to solve two specific technical problems connected to additive manufacturing of novel heat exchanger concepts:
- Thermal stresses and deformations
- (Uncontrolled) surface roughness
We think that once we have the knowledge and tools to deal with these problems, we will finally be ready to use additive manufacturing to make functional heat exchangers that both look and behave as intended. Before looking more into the specific problems and describe what HighEx aims to do, we should address the reason for our enthusiasm for additive manufacturing of heat exchangers in the first place?

Heat exchanger cost and efficiency can make or break a project
Heat exchangers are crucial industrial components utilized in countless thermal processes in both industry and everyday life; heating your living room, cooling the battery pack in an electric car, in production of everything from yoghurt to petrol. The combined efficiency and performance of all heat exchangers therefore sum up to incredible significance for the world’s energy footprint.
For some applications, heat exchanger efficiency can be a missing factor causing new technology to fail to be implemented – it simply becomes too expensive to obtain the required heat exchanger performance compared to the produced benefit.
Producing electric power from industrial surplus heat is one application where we could consider the main “heat recovery heat exchanger” to make or break the project; On one side it must be efficient enough to capture the available heat at the highest possible temperature, but on the other side not cost too much.
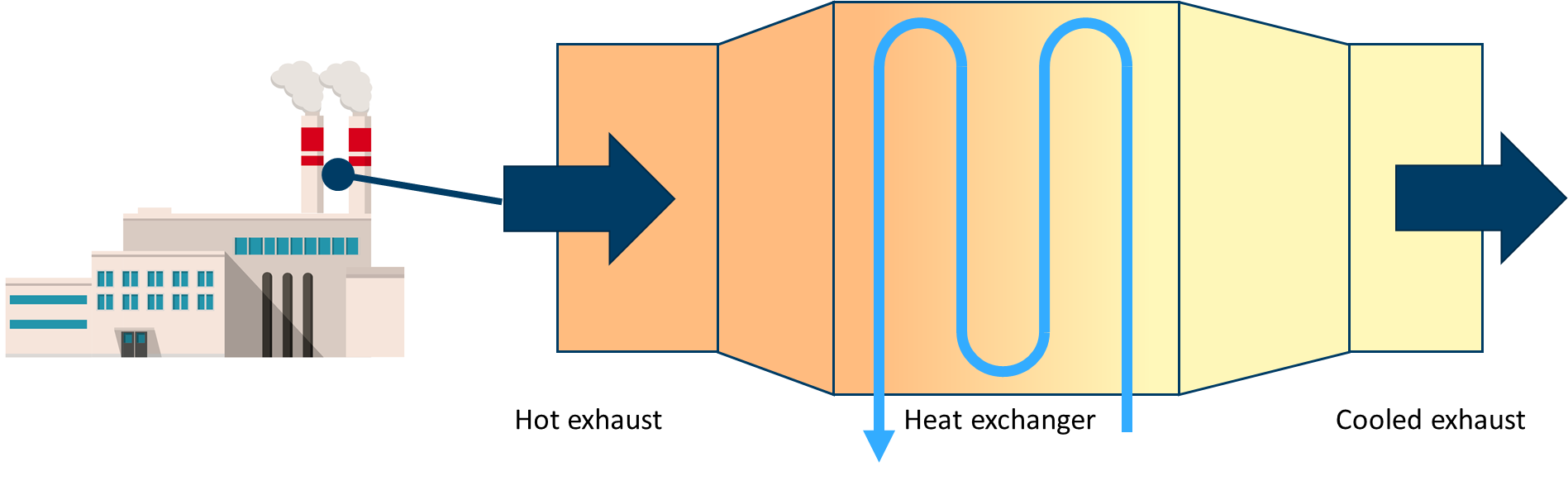
Opportunities in additive manufacturing of heat exchangers
Heat exchanger technologies are being developed on several fronts such as performance, cost, and energy- and material efficiency. Although substantial progress is undertaken by the manufacturers, the major focus is still on improving or optimizing specific heat exchanger types and technologies.
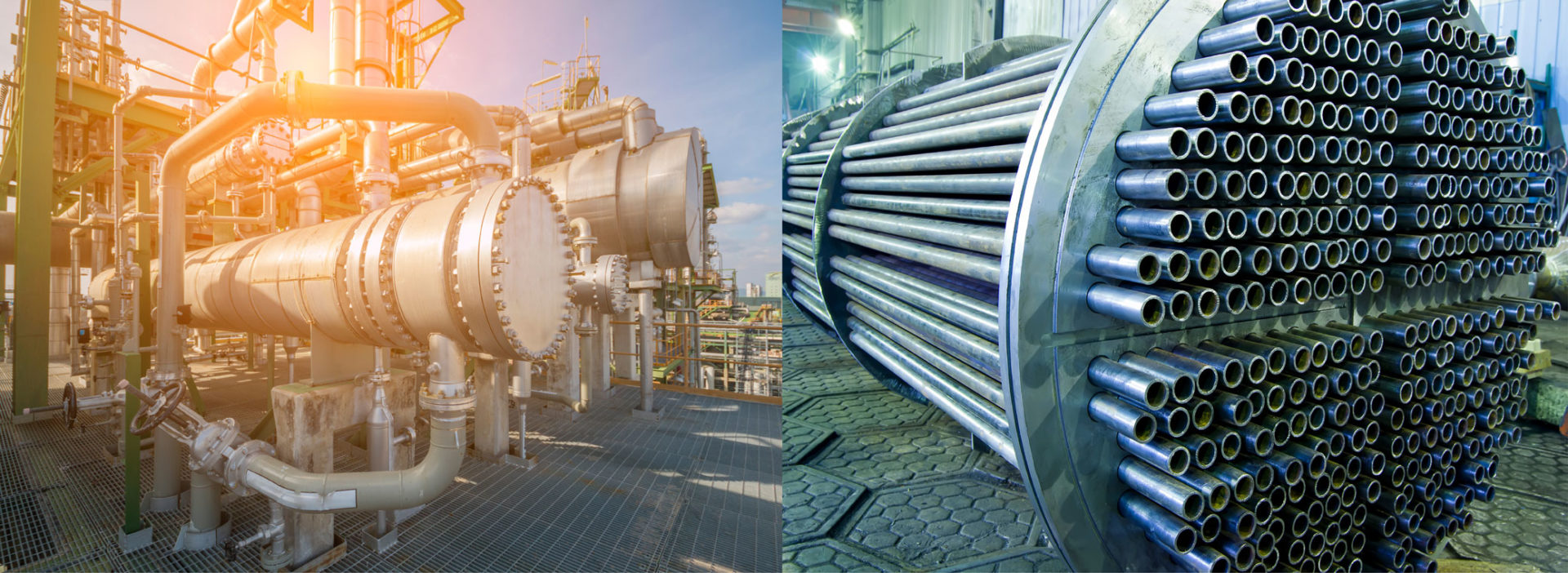
Manufacturers are limited by design boundary conditions that is controlled by the ‘manufacturability’ of the designs. On the other hand, additive manufacturing provides new opportunities for optimal design and advanced technology integration in this field, building up to the big innovation question: “What new potential could be realised if heat exchanger design and manufacture are made free from current production methods and constraints?”
FME HighEFF pursues development of more efficient heat exchangers, mainly from a pure performance focus; how efficient can we make a heat exchanger? New opportunities with additive manufacturing are also being considered, for example by exploring novel designs without concerning ourselves with any practical limitations to manufacturability. One example could be concepts with continuously changing geometry aiming to perfectly correspond to the changing fluid conditions flowing inside – such designs could prove impossible to manufacture by traditional methods.
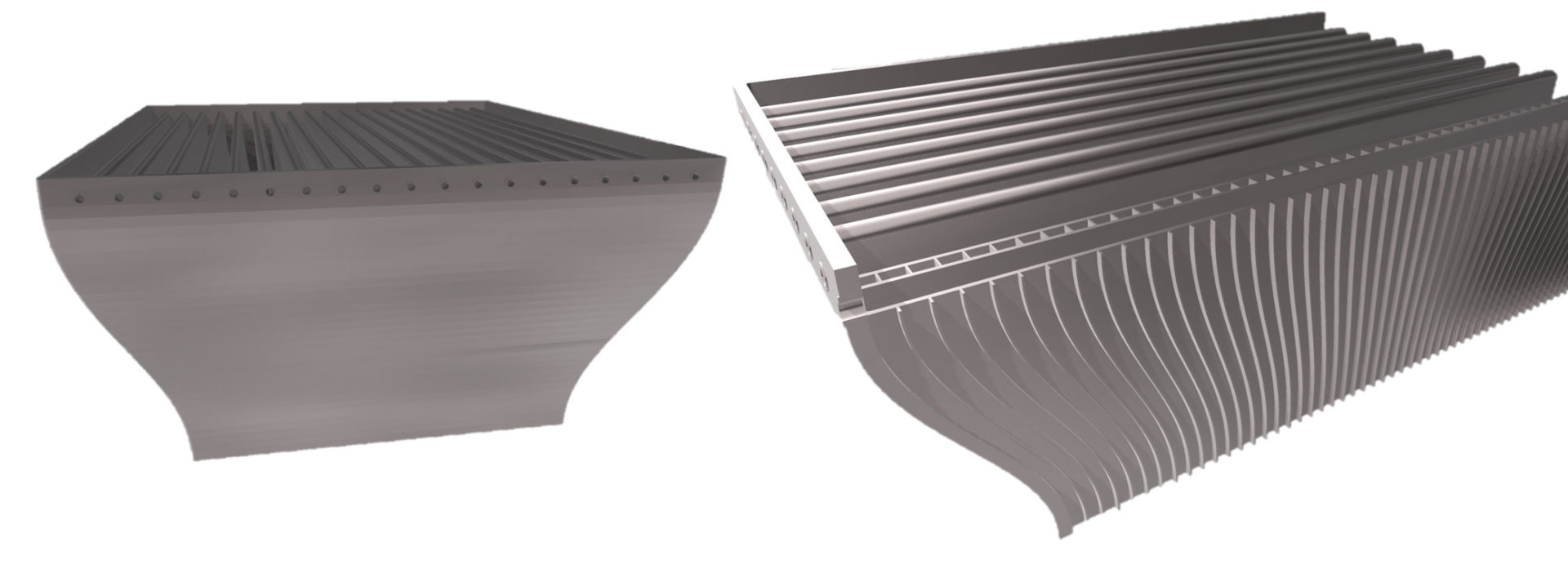
Where research activities in HighEFF explore design possibilities for more efficient technology concepts, HighEX aims to contribute necessary solutions to a couple of remaining, practical problems; thermal stresses and surface roughness.
Producing highly complex heat exchangers using the powder bed laser fusion (PBLF) technology will bring about unavoidable thermal stress and areas with relatively high surface roughness. In a heat exchanger, this will affect heat transfer and pressure losses. It is crucial to mitigate these effects, and ideally take them into consideration in the actual design.
The most relevant technology for additive manufacturing of heat exchangers
We consider the powder bed laser fusion technology to be very relevant for additive manufacturing of heat exchangers. In simple terms, a laser melts and fuses a metal powder so it solidifies into the intended shapes, incrementally in vertical layers. Different cooling rates in different parts of the object cause thermal stresses inside the printed part, which can lead to deformed and warped parts.
Many of the geometry features found in conventional efficient heat exchanger could be expected to enhance such stresses, for example sharp corners, and combining elements with very different metal thickness.
Tolerances on internal dimensions in a heat exchanger will be very strict. There’s simply no “free space” to contain any slack for warped parts without the heat exchanger either not working properly or being subject to failure due to e.g. fretting, clogging or excessive vibration.
Clearly, thermal stresses from the additive manufacturing process cannot be ignored. In this project, we will apply and validate a workflow combining heat exchanger design with stress prediction using a 3D FEM model of the additive manufacturing process of the heat exchanger. With this approach, we expect to be able to adjust the design to get the desired results. We will validate the method by submitting a couple of samples to the workflow, including the actual manufacture, and physically measure the results.
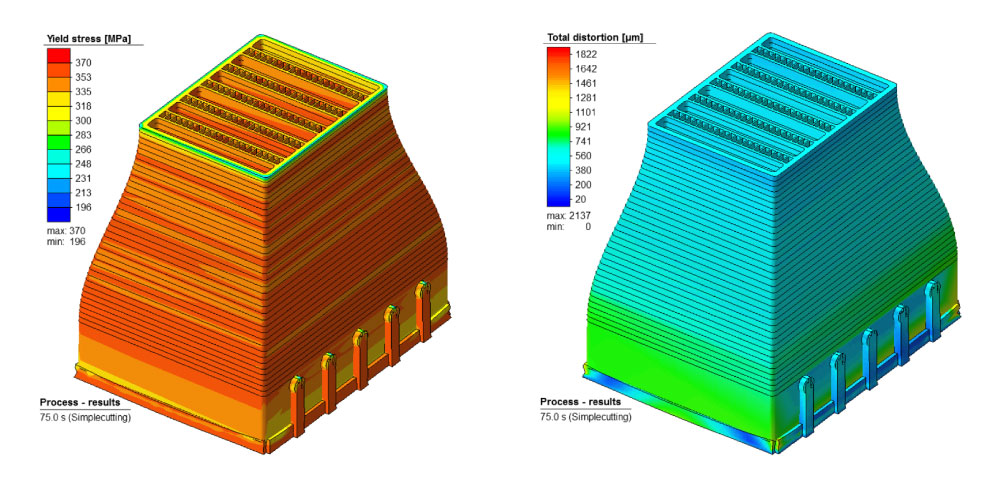
Surface roughness
Surface roughness in heat exchangers affect two crucial aspects; heat transfer efficiency and pressure drop. Some roughness in the correct location can be beneficial to heat transfer, while rough surfaces elsewhere may obstruct flow, cause vibrations, or collect dirt. As everything else in a high-efficient heat exchanger, roughness cannot be left to chance.
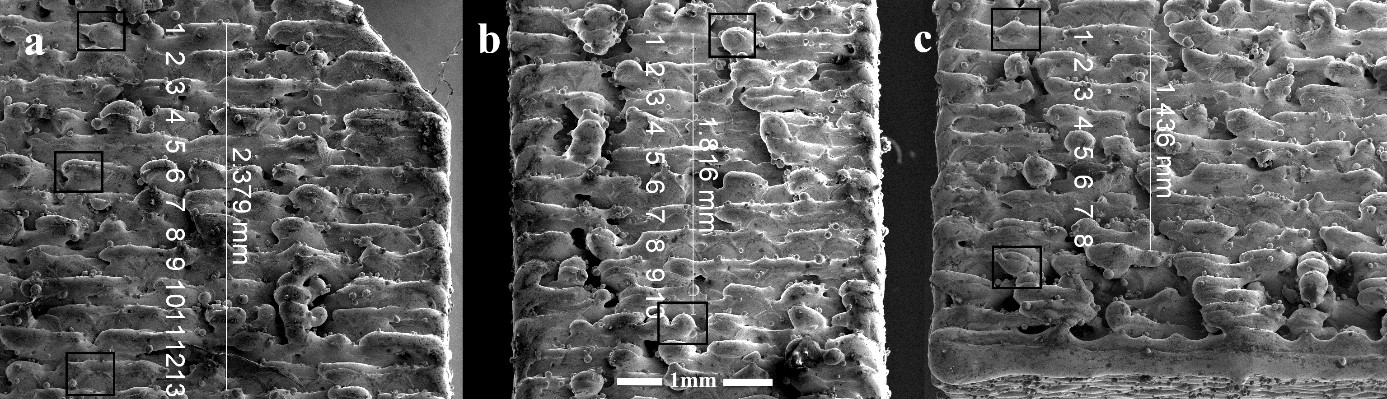
In the investigated additive manufacturing process, roughness is dependent on both surface orientation during manufacture, and process parameters such as layer heights, temperatures and manufacture speed. We can therefore at least to some extent predict and control the end result towards a favourable direction. Ideally, this is considered already in the heat exchanger design phase – how can we configure a heat exchanger so that the channels where fluid will evaporate become rough and full of nucleation sites, while the other fluid flows in channels as smooth and unrestricted as possible?
Integrated approach
The promising design freedom that additive manufacturing processes allow is genuinely extremely exiting, with great potential impact on current and future processes. However, the mutual influence of product design and actual production process is both significant and quite complex. This is the core problem of the project, and we want to evaluate the proposed workflow as a potential solution. That requires combining forces across traditional technical domains.
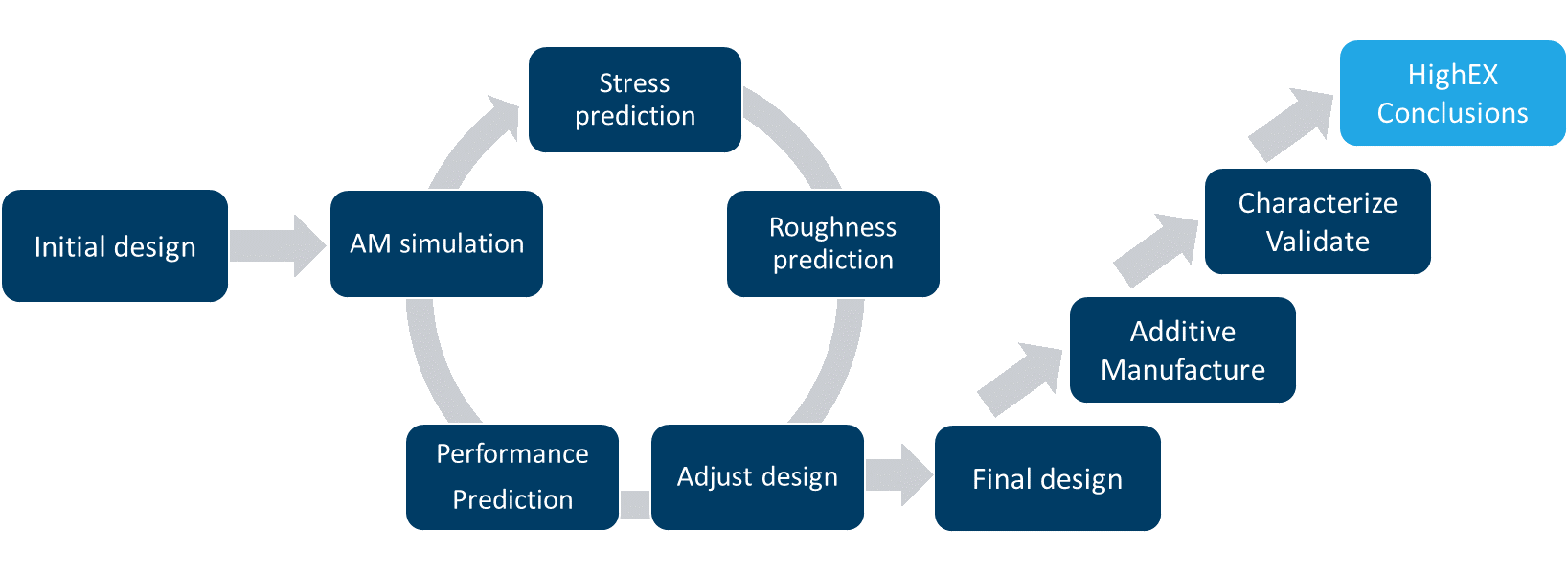
The project will culminate in the actual manufacture of a couple of samples of realistic and relevant geometry features, that will undergo characterization to measure whether surface roughness and dimensions are as predicted. If this project is successful and the proposed workflow produce satisfying results, the next project could aim to produce actual functional heat exchangers that can be tested in the laboratory or even in industry processes. There are already ideas being developed for new technology waiting to be realised and put to the test.
The HighEx project started in September 2019 and will run through May 2020. Researchers from SINTEF Energy Research and SINTEF Industry are involved in the project.
Comments
Thanks, sintef.com for publishing valuable article on Additive Manufacturing of Heat Exchangers. I hope it reaches more people.
Thanks for sharing very interesting blog. I like it very much because it really a nice blog.
Thanks for sharing the great information about heat exchanger manufacturers.
Great approach! Looking forward to the research results and future projects – good luck!