The fourth industrial revolution, or Industry 4.0[1], is a concept characterized by a high degree of automation, extensive use of sensors and continuous data exchange in production, through the utilization of new ICT solutions (eg Sensorics, Augmented Reality, and industrial internet) and methodologies (eg Big Data Analytics). This industrial revolution will create new values, among other things by new smart product services, and integration of value chains.
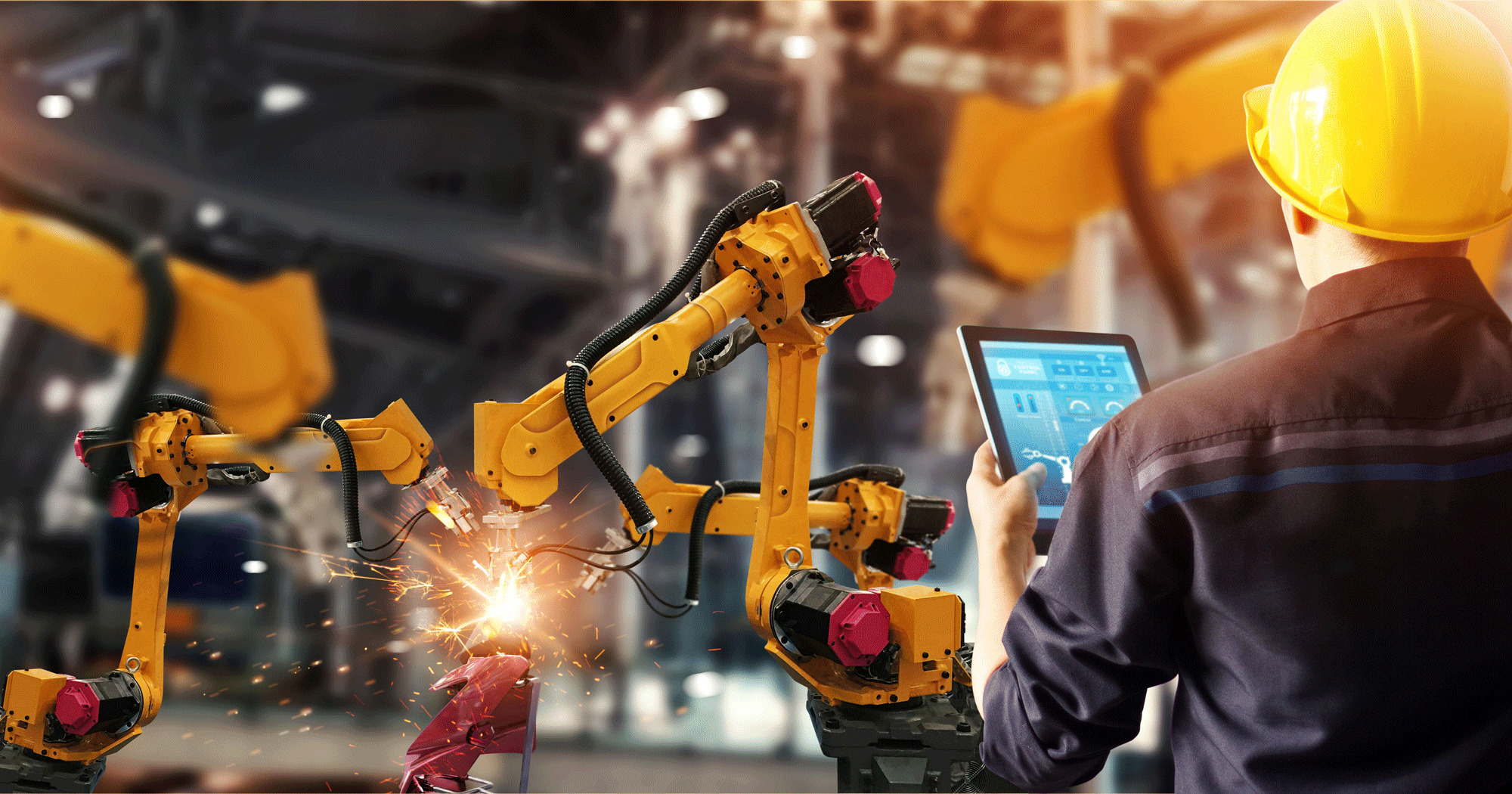
Despite the automation and digitalization pace, workers remain a critical resource for the competitiveness of the European manufacturers, especially in complex, high-tech, and customized manufacturing industries as the Norwegian industry. Highly skilled, independent, and flexible workforces are foundational to solve problems, resolve root causes, drive continuous improvement efforts, and innovate towards short-term and long-term changes. Digital transformation and value creation of the Norwegian manufacturing industry therefore requires that the production companies utilize the digital technologies to enhance the operators.
Norwegian industry economic report for 2016 nevertheless shows that, even though we have flagships that can be said to be at the forefront of the utilization of modern industrial production methods, there is a great deal of improvement potential. Less than half of the companies say that they use opportunities that can be considered premises for digital value creation activity:
- 50% have one or more robots in production
- 47% use electronic data exchange in the value chain
- 25% automatically utilizes captured data from production to improve or control process
SINTEF performs applied research on digitally enhanced work
In line with this industrial requirement, SINTEF has also increased its efforts for helping the digital transformation of manufacturing companies, and the digital enhancement of operators at both national and international level.
As an example of international project, SINTEF coordinated the HUman MANufacturing (HUMAN) project, a European H2020 project that ended in 2019. HUMAN aimed to leverage digital technologies to augment the human worker on the shopfloor to mitigate the human shortcomings and limitations of technology. Consequently, the project developed a platform that was contextually aware of the factory, the human operator and the task being carried, identifying when an intervention was necessary to support the operator in performing their tasks with the desired quality, whilst ensuring their well-being. The project explored different technologies (e.g. Augmented Reality, machine learning) as part of the platform to provide the operators on the shopfloor with cognitive and physical support. A critical outcome of the project was KIT-AR, a fully integrated industrial AR system that aims to increase manufacturing productivity whilst providing support for quality assurance by using machine learning and computer vision. This functionality was coupled with process mining and analytics to support organizational learning and optimisation. Three distinct end-user organizations took part of the project, with wide range of different requirements, which in the case of cognitive augmentation resulted in the following three use cases:
- The Airbus case (Spain) consisted of supporting the assembly of electrical harnesses within the fan cowl of the A320 neo engine. The aim was to ensure that operators would follow the recommended good practice and to have automated quality control of the correct fixture of the electrical harness;
- The Comau case (Italy) consisted of the assembly of a robot forearm. The aim was to ensure recommended good practice was followed, and include the support for automated quality verification of the sealant application and subsequent quality traceability;
- The Royo Group case (Spain) consisted of reducing the time of competence for seasonal workers who require to acquire the knowledge of a large collection of products and focused on imparting the required knowledge to trainees to reduce the need of involving experienced operators during the training phase of the seasonal workers, thereby reducing the overall training time by 25%.
As an example for a national project, Aktiv Operatør was an industry-driven innovation project ended in 2020, focused on technology support for production operators to increase situational awareness, enable real-time control of production, and facilitate three-dimensional team coordination (time, place, and competence). The project involved GKN Aerospace and Sandvik Teeness to investigate, test, evaluate, and implement the digitalization methods and technologies in pilot cases. By digitally enhancing their operators, GKN and Teeness enhance their ability to take more responsibility in the production system, increase their confidence to make better decisions for efficient production, coordinate themselves, work safely and ergonomically, and continuously improve their competence.
- The GKN case focused on testing Augmented Reality glasses for operator learning, and placing dashboards on the shop floor for visualization of the production plan, and integrating El-Watch sensors to obtain an overview of machine status in real-time.
- The Sandvik Teeness case focused on developing a decision support tool for situation awareness and production control in the assembly department.
Further research on digitally enhanced operators
More recently, SINTEF has started a new project called HUMANNOR, funded by the Norwegian Research Council. The objectives of this project are:
- to increase the awareness of the Norwegian organizations on the digital enhancement of operators
- to perform dissemination and exploitation activities, and facilitate the adoption of the digital technologies and results of the earlier national and EU project in the Norwegian industry and research communities
- to build a strong Norwegian community in the area of the digital enhancement of human-centred manufacturing environments, and
- to support the Norwegian participation in future national and international projects related to this topic of digitally enhanced operators
The project will organize and perform eight webinars, six seminars, and four dedicated workshops related to this topic. These activities will have impacts on increasing the knowledge on the potential impact of cognitive augmentation of workers, hands-on experimentation of cutting-edge technology, identification, and planning of digitalization of shopfloor. For those interested in going beyond experimentation, increasing knowledge and wish to commit to the digitalization, SINTEF supported by KIT-AR will work with the company on new proposals for collaborative research projects both in Norway and the EU context.
Join us in this journey and be part of our LinkedIn community, if you are also interested in the digital enhancement of production operators. You will be informed about the state-of-the-art applications, cutting-edge reports, and events we will organize. You will also have the opportunity to choose the topics we will post, share your experiences, engage with other companies that have implemented certain solutions, and build partnerships for future projects.
0 comments on “Digitally enhanced operators as a competitive advantage”