Co-author: Ángel Álvarez Pardiñas
Through several research projects, SINTEF, together with NTNU and our industry partners, aims to support an agile adoption of natural refrigerants in heat pumps and refrigeration systems for the maritime sector, replacing substances that contribute to global warming.
The shipping sector must reduce their greenhouse gas emissions
In 2018, the International Maritime Organization (IMO) agreed on a strategy to reduce greenhouse gas (GHG) emissions from international shipping by 50% by 2050, compared to 2008. To achieve this goal, the emissions per transport work must be reduced by 40% by 2030 and 70% by 2050.
“Transport work” is the amount of cargo or number of passengers multiplied by the transport distance.
However, following new predictions of the growth in maritime transport, such as in the DNV report Ocean’s Future to 2050, IMO is now working on a more ambitious, revised strategy.
Changing to low-carbon fuels is not enough
Forecast reports, e.g. DNV’s Maritime Forecast to 2050, in line with the Fuel EU Maritime Initiative, indicate that alternative energy sources and fuels will be crucial for the maritime industry’s ability to achieve its climate goals. According to DNV’s report, electrification, biofuels, e-fuels (produced using renewable electricity) or onboard carbon capture and storage (CCS) are key to reducing GHG emissions. The report also pinpoints the need for more energy-efficient machinery, including refrigeration systems, chillers, and heat pumps, which are used to provide comfort to passengers and crew, and to preserve food or cargo.
For cruise ships, the cooling and heating needs represents, on average, 40% of the ship’s total fuel/electricity consumption. Part of this heating demand is currently met by waste heat from the combustion engines. As hybrid propulsion systems, such as a combination of batteries and combustion engines, are implemented, the availability of waste heat will decrease.
A need to efficiently meet heating and cooling demands
Heat pumps, refrigeration systems and chillers are all so-called vapour compression systems, and operate according to the same principles. The difference between them is basically the temperature level, dictated by the purpose of the system. Space heating and hot water needs are met by a heat pump, provision cooling by a refrigeration system, and space cooling by AC chillers.
As an example, the heat pump is able to upgrade heat at a relatively low temperature (heat source) to a higher temperature level (heat sink). To do this, an additional energy input (work) is required, typically in the form of electricity.

The energy efficiency of a heat pump or refrigeration systems is referred to as its “coefficient of performance” (COP). COP is the ratio between the amount of heating or cooling produced, and the electricity consumed. Typically, COP ranges between 2 and 4, depending on the operating conditions. For comparison, the COP of an electric boiler is always below 1, making the vapor compression systems far more energy efficient. If the system can fulfil both heating and cooling loads at the same time, the COP is even higher.
Refrigerants: the core of a heat pump and refrigeration system.
In a vapour compression system, a substance called a refrigerant undergoes several processes to absorb heat from the heat source, upgrade its temperature, and reject it to the heat sink.
The selection of refrigerant is crucial, as it affects how the system is designed in terms of layout, materials, operating pressures, etc. It also determines the safety measures to be implemented, since refrigerants can be toxic and/or flammable. Moreover, some refrigerants are produced through synthesizing different chemicals, and are connected with adverse environmental impacts.
Ideally, systems are built to avoid refrigerant leaks, but in practice, some refrigerant will escape. Leakage rates are higher onboard ships compared to onshore installations, probably due to vibrations from movement of the ship or the corrosive environment.
The refrigerant evolution
As represented below, the first generation of refrigerants were “natural”, in the sense that they were substances naturally found on Earth. At that time, the overarching goal was that the systems functioned. Safety issues, such as flammability and toxicity, were of secondary importance. Since then, the evolution of refrigerant selection has been linked to safety and environmental aspects.
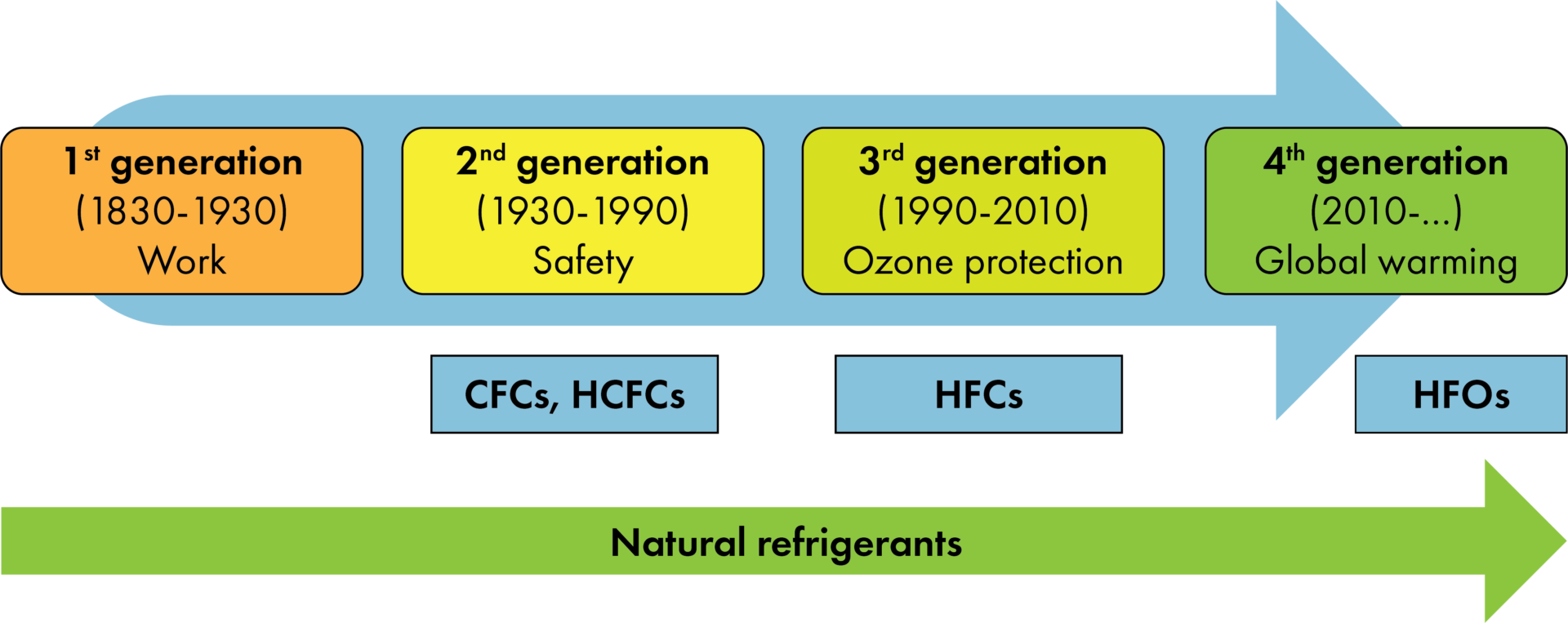
Unforeseen environmental and safety issues
In the 20th century, the chemical industry developed various synthetic refrigerants (second generation), which were safer to use. Most natural refrigerants were consequently discarded in favour of synthetic ones, such as chlorofluorocarbons (CFCs) and hydrochlorofluorocarbons (HCFCs). However, during the 1980s, CFCs and HCFCs were associated with ozone layer destruction, and their use in land-based applications was phased out following the Montreal Protocol. For the maritime sector, the phase-out of has been slower, but according to IMO regulations, there has been a total ban of CFCs in new installations since 2005, and of HCFCs since 2020.
While the third-generation refrigerants, the hydrofluorocarbons (HFCs), have no ozone depletion potential (ODP), they still have a strong global warming potential (GWP). In fact, some HFCs have a GWP that is several thousand times that of carbon dioxide. Thus, HFCs are also being gradually phased out, with drivers such as the EU F-Gas regulation and the Montreal Protocol amendments.
IMO has not banned HFCs in the maritime sector, nor are ship installations directly affected by the F-Gas Regulation, with a few exceptions. This includes a “Service Ban” from January 2020, which will affect certain existing systems using HFCs with a GWP above 2,500. The F-Gas Regulation will also have an indirect impact on maritime applications. For example, installing systems with HFCs will become more expensive, due to the reduction in the EU’s HFC import allowance.
What will the next generation of refrigerant bring us?
The current debate is whether yet another chance should be given to synthetic refrigerants, in the form of hydrofluoroolefins (HFOs), or if we should focus entirely on natural refrigerants.
HFOs are often advertised as fluids with a low GWP, with the sole disadvantage of being mildly flammable. However, several studies, recently reviewed in a report by ATMOsphere, indicate other concerns. For example, HFOs decompose in the atmosphere into the toxic trifluoroacetic acid (TFA), which is shown to accumulate in (drinking) water reservoirs. It also produces hydrofluoric acid (HF) when burned, which is acutely toxic. In addition, some of the decomposition products from HFOs have large GWP and even ODP.
The use of many synthetic refrigerants might soon be banned
Many of the refrigerants in the HFO and HFC family are classified as so called “Per- and polyfluoroalkyl substances (PFAS)” or “forever chemicals”. The PFAS group contains around 10,000 chemicals, used in a wide range of industries, and are known to be highly persistent, pollute the environment, and cause serious health effects.
As a consequence, some European countries, Norway included, have submitted a proposal to restrict or ban the use of PFAS in EU. The proposal is currently under evaluation by the European Chemical Agency (ECHA). If adopted, it will restrict not only the use HFOs but also several HFCs, such as HFC-134a, which is the most common refrigerant in ships’ AC chillers. In addition, there is an ongoing revision of a strengthened F-Gas Regulation. A stricter phase-out of both HFCs and HFOs is being debated between industry and the European Parliament’s Committee on Environment, Public Health and Food Safety (ENVI).
Natural refrigerants should be the natural choice
Considering the questionable history of synthetic refrigerants, a more sustainable strategy would be to focus on using natural refrigerants, and develop energy-efficient systems that utilise the characteristics of these fluids. This has actually started to happen: natural refrigerants, such as carbon dioxide, ammonia, hydrocarbons, and water, are gaining increasing interest from industry.
Natural refrigerants are competitive to synthetic refrigerants in close to all applications. However, there are safety concerns which cannot be ignored, such as high operating pressures, toxicity, and flammability.
SINTEF is involved in several projects that are developing and demonstrating the feasibility of natural refrigerant technologies. SuperSmart, MultiPACK, INDEE+, CoolFish, CruiZE, and LowPass focus on CO2 systems in supermarkets, fishing vessels and cruise ships, while SkaleUp concentrates on high-temperature heat pumps with hydrocarbons for simultaneous heating and cooling in dairies. Furthermore, HighEFF has conducted a case study on using an ammonia-water heat pump in a dairy.
The role of classification societies in the transition to natural refrigerants onboard ships
Ship classification societies are non-governmental organizations that establish rules and regulations to ensure the safety of all technical systems on board a ship. They define and update the minimum requirements that these systems must comply with, and perform ship surveys to ensure compliance. Registering ships, obtaining insurances, entering ports, etc. requires the approval of a classification society.
For vapour compression systems (refrigeration systems, chillers, and heat pumps), there are requirements on materials to be used, connection types, machine room conditions, equipment testing, detection protocols and alarms, etc. After reviewing the regulation documents from two of the largest classification societies, it is clear that natural refrigerant systems are predominantly evaluated on a “case-by-case” basis, if allowed at all. This is both time and resource consuming. A higher degree of standardization of these requirements is needed to make these systems more attractive to implement.
The regulations for using natural refrigerants must be updated
The EU’s F-Gas Regulation, and the proposal to the EU Chemical Agency has made the future use of HFCs and HFOs more difficult or even impossible. For many applications, natural refrigerants will be the only option left. Therefore, there is an urgent need to focus on adapting the regulations from Classification Societies to facilitate the safe implementation of natural refrigerants. Some aspects that should be considered include:
- The special safety requirements specified for CO2 are, if compared to some commonly used HFCs, unjustified and lead to a significant increase in costs. CO2 systems should be allowed in the main machinery rooms, just like the other non-toxic, non-flammable refrigerants.
- The detection of potential refrigerant leakages is a key safety measure. However, the maximum allowed concentration for a specific refrigerant should be linked to the Refrigerant Concentration Limit (RCL) as defined in standards such as ISO 817, and should not be arbitrary. As per now, the detection limit for CO2 could be reached without any refrigerant leaks, due to the breathing from hard working crew.
- For hydrocarbons (flammable), the role of ventilated enclosures may be crucial for their safe use. Systems in ventilated enclosures are well known in land-based applications. With charge limitations (EN-378), reliable detection, equipment for potentially explosive atmospheres (ATEX), separate ventilation, etc., these units could be adopted without compromising safety.
- The regulations should better clarify requirements on HFOs, focusing on how to deal with these refrigerants due to their flammability and potential environmental and health concerns.
As also stated in the maritime forecast by DNV, it is important to address challenges and speed up the progress of next-generation carbon-neutral ships. Heat pumps and refrigeration systems with natural refrigerants should be part of this work. SINTEF and our partners are ready and eager to contribute!
0 comments on “Heat pumps and refrigeration systems on board, naturally!”