Cheap, flexible electronics (can be bent) have potential uses in many areas where the flexibility itself is one of the defining characteristics of the product, e.g. in clothes, toys and other electronic products. Even though these electronics can be very cheap due to the large-scale roll-to-roll manufacturing process, there is still an expectation that they will function after exposure to the strains and stresses expected during bending. Since different flexible electronics products will be used differently, it is essential that a testing setup is flexible with regards to different parameters.
To meet this demand, SINTEF has developed a bending machine to facilitate a repeatable and representative way to characterize the reliability of flexible electronic systems in relation to bending. This was done in Flextag, a project with ThinFilm Electronics which purpose was to develop smart tags on flexible substrates for a multitude of uses.
How FlexTag tested flexible electronics differently from others
Previous setups for bending of electronics have mainly been based on clamping each end of the substrate and oscillating the ends to and from each other. As the clamps approach each other the substrate bends to a specific radius. Although this might be representable for some applications, it is far better for analysis purposes that the radius stays constant throughout the process.
The FlexTag project set three main criteria for the design of the bending machine:
- Constant bending radius, but possible to vary between experiments
- Constant tension, but possible to vary between experiments
- In-situ measurement of electrical properties to analyze the number of cycles before failure
Bending machine design
The developed bending machine can be seen in Figure 1. It consists of a horizontal motorised cylinder (a), whose motion is actuated by a 12 V DC motor with a 1:3240 gear ratio (b) and controlled by a digital control unit (DCU) (c).
The DCU receives positional information from optical sensors (d) that can be adjusted to accommodate for different sample lengths. The test samples are clamped to the cylinder by 3D printed test probe holders (e). Constant tension is applied to the samples by fishing weights (f) that are clamped to the bottom of the samples. During bending, the electrical characteristics are logged to a Keysight 34972A data logger.
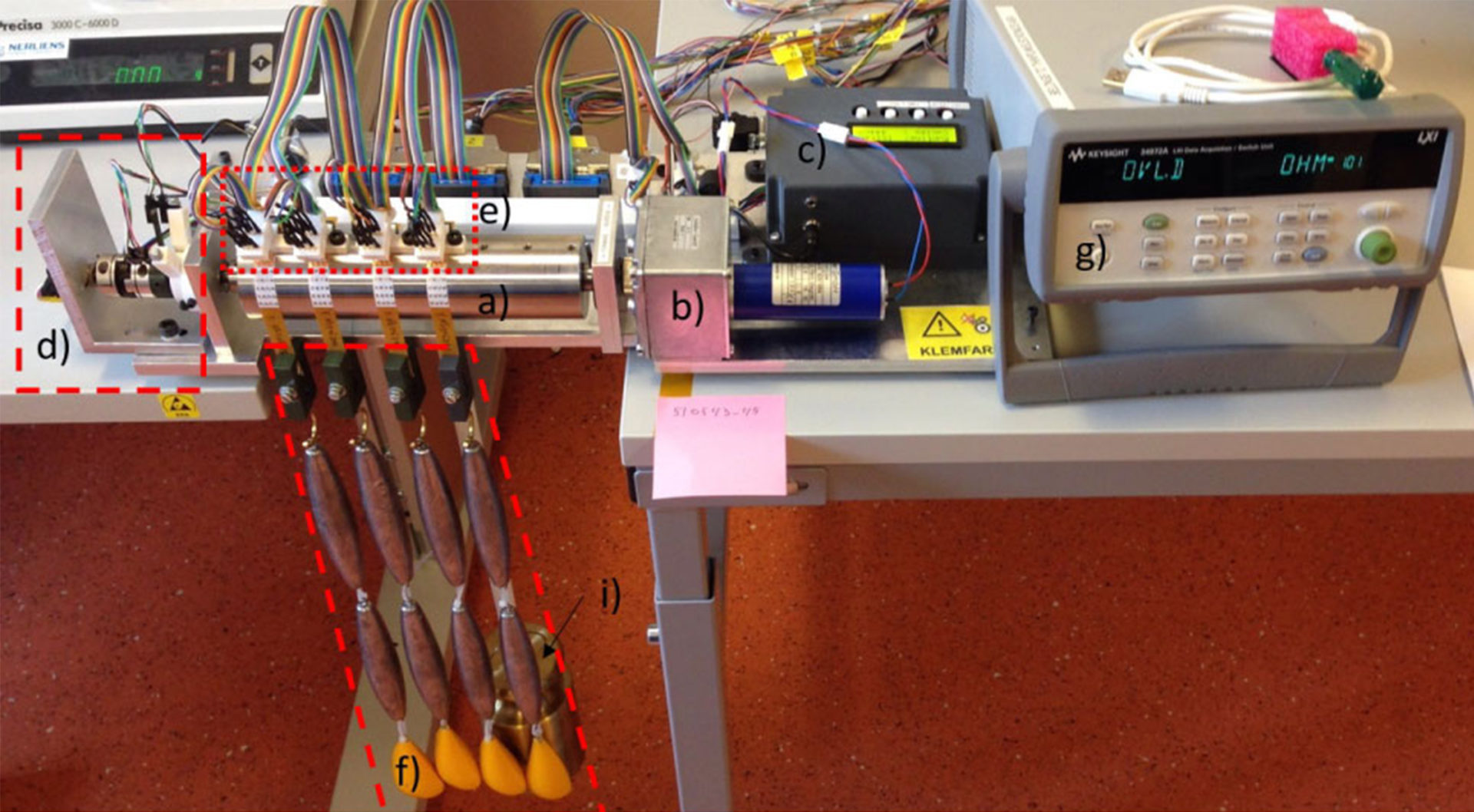
Understandably, the machine in Figure 1 was designed around the samples from the FlexTag project, but the simplicity in design and the use of 3D printed components means that it possible to accommodate samples of different widths and lengths. With the current design the maximum bending diameter is 78 mm, but with minor changes this can be expanded. Smaller bending diameters can also be accommodated by attaching different diameter addons on the cylinder. All the current setups are illustrated in Figure 2.
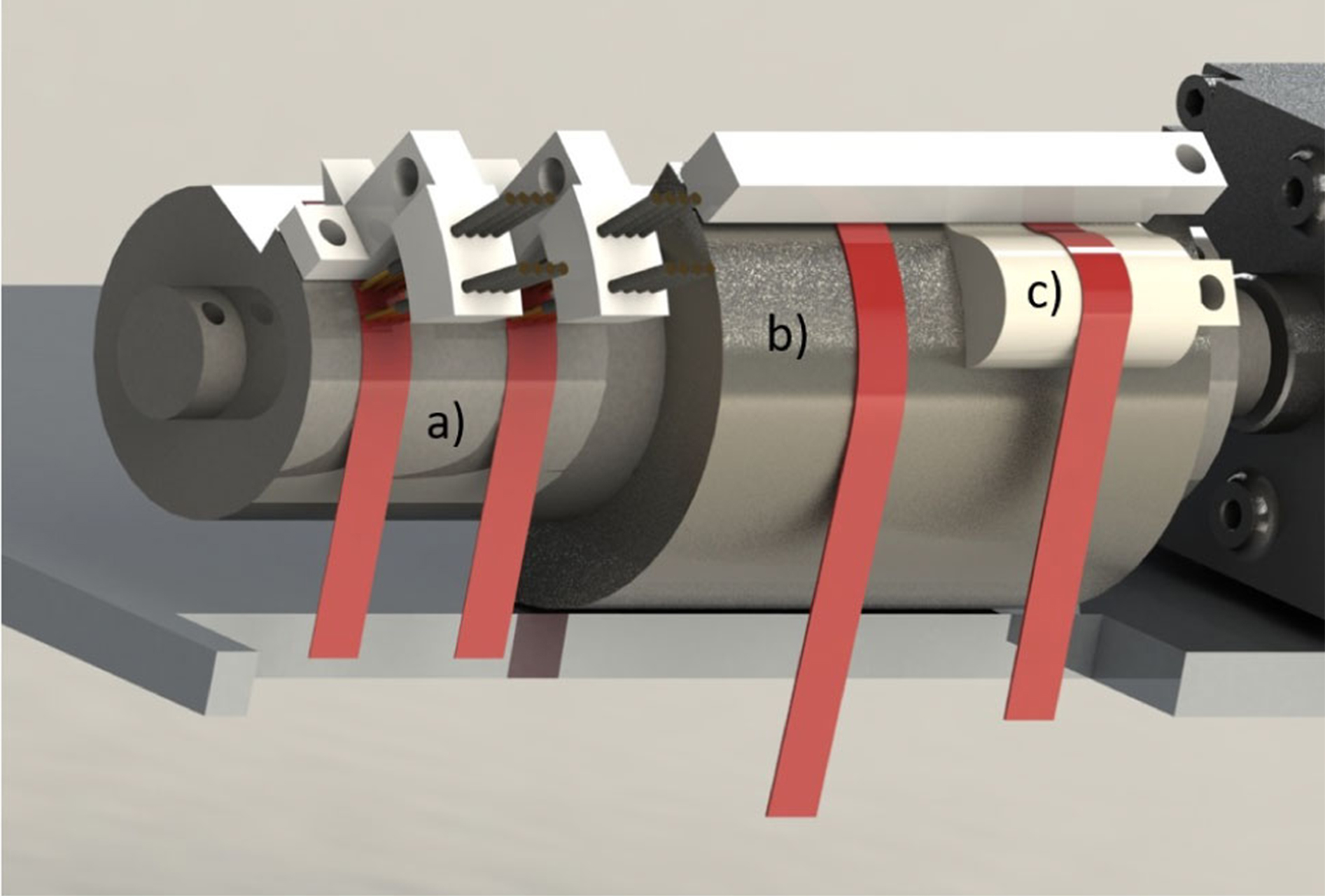
What can we find out by repeated bending of flexible electronics?
In the FlexTag project we designed representative samples that enabled measurement of electrical properties during the bending experiments (so-called in-situ measurements). By analysing the data afterwards, we could count the number of bending cycles the samples tolerated before they were considered to have failed. This gave us insight into the nature of the failure mechanisms invoked by the repeated bending and thus the opportunity to mitigate potential problems, either by changing the design, materials or both.
For example, in the start of the project the samples were constructed using silver printed conductive lines on PEN substrates with electrical components attached with anisotropic conductive paste (ACP) for both mechanical and electrical connection. Although the silver lines themselves did not deteriorate during bending, it was clear that the electrical connection between the silver lines and the electronic components provided by the ACP slowly worsened and in the end surpassed the 20% increase in resistance that was set as a failure threshold.
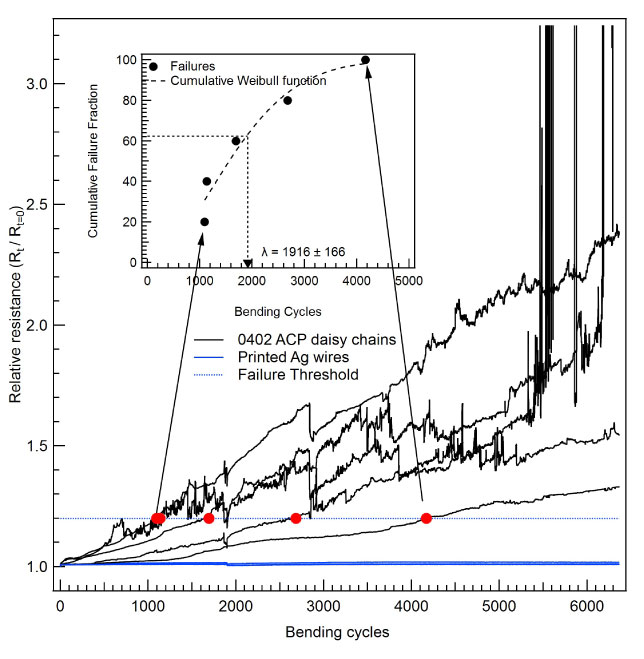
But what does this actually mean? Let’s pretend that this of kind flexible electronic circuit was an integral part of a system that monitored your knees while jogging so the circuit would be bent every time you would take a step. The inset in Figure 3 shows that 62.3% of the circuits will fail after 1916 steps. At a leisurely jogging pace of one step per second per leg, the circuit would not be expected to last more than about 32 minutes, which is not adequate.
This potential problem was mitigated by replacing the printed circuitry by a more conventional flexible circuit made by PI with laminated copper tracks. Instead of ACP, the electronics were attached using a low temperature solder. For this structure, most samples did not fail, even after several thousand bending cycles, and using statistical analysis it was estimated that 62.3% of the samples would fail after about 50 000 cycles, which would mean operation for at least 14 hours in the above example.
0 comments on “FlexTag – Bending the rules for flexible electronics”