Blog written by Thomas Sauder and Maxime Thys.
For almost a decade, SINTEF Ocean has been assisting designers to assess novel floating wind turbines concepts by using ReaTHM® testing (real-time hybrid model testing).
It is a cyber-physical method where the physical experiment (in a wave tank) interacts in real-time with a numerical simulation. The method enables representing wave, current and wind loads on the floating wind turbine with high accuracy, and hereby obtaining the complete picture of its dynamic response.
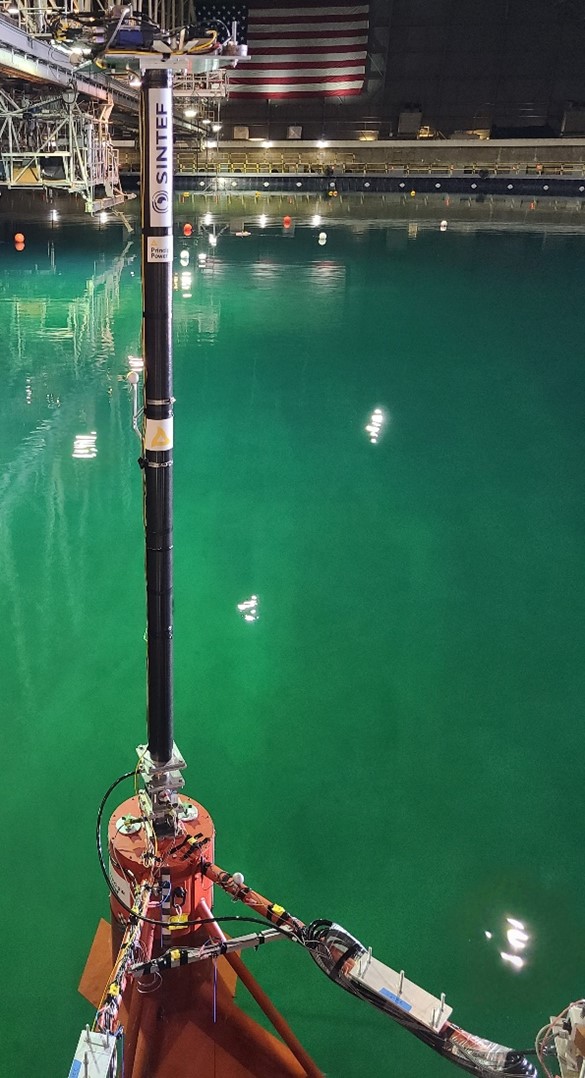
When testing offshore wind turbines, the numerical simulation consists in a tailor-made version of OpenFAST [1]. It is used to compute the turbine-induced loads on the floater, which are applied to the floater model using a cable-robot [2]. See Figure 2. The motions of the physical model are measured, and fed to OpenFAST. The output of OpenFAST is the turbine-induced loads which are applied on the model, on top of the physical wave and current loads. This way, we account for the effect of the turbine motions on the loads; aerodynamic damping is, for instance, precisely modelled.
Figure 2: testing of INO WINDMOOR 12 MW floating wind turbine at SINTEF Ocean
This method solves the notorious Froude-Reynolds scaling mismatch issues. Froude scaling is adequate to scale down waves while Reynolds scaling is adequate for wind; but both can’t be achieved at the same time. As wave and wind loads are equally important for floating wind turbines, ReaTHM® testing is the only way to obtain the full picture of the problem in experiments. Additional benefits of the method are: controlled wind field, reduced cost for model testing and increased flexibility in the test conditions. A vast majority of the floating wind turbines producing electricity today, or in the pipeline, have been undergoing cyber-physical tests at SINTEF Ocean, and such tests give precious insight in phenomena specifically related to floating wind turbines [3, 4, 5, 6,7].
While we have been using and continuously developing cyber-physical testing in our lab since 2014, SINTEF has for the first time applied this method in another hydrodynamic laboratory. And what a laboratory!: the manoeuvring and seakeeping laboratory of the US Navy, which is the largest in the world (110 x 73 m, see Figure 3). The tests were performed for Principle Power, a major actor of the offshore wind business, who was aiming at creating a digital twin of its flagship Windfloat® concept. We are very proud to have assisted Principle Power and the US Navy, and grateful to them for making this collaboration possible. For SINTEF researchers, performing experiments in this gigantic laboratory was of course exciting, but also showed the maturity of our tools and procedures, which we could adapt to a new site.
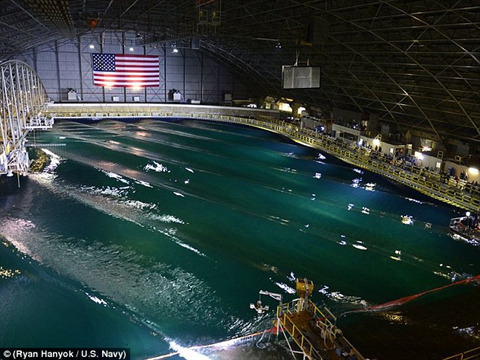
The following video shows views of the tests. Note that in general, we use six cables to apply five components of the turbine-induced loads (all except the vertical force that is generally unimportant [8]).
We are fully expanding the range of applications of cyber-physical testing in marine hydrodynamics, with applications to sail-assisted propulsion of ships [9], to the estimation of nonlinear hydrodynamic loads on floating structures [10], and much more to come. Stay tuned, and feel free to contact us for more information.
References
[1] NREL, 2022, OpenFAST v3.3.0 on Github, https://github.com/OpenFAST/openfast, accessed 21.11.2022
[2] Chabaud, V., Eliassen, L., Thys, M., Sauder, T., 2018. Multiple-degree-of-freedom actuation of rotor loads in model testing of floating wind turbines using cable-driven parallel robots. Journal of Physics: Conference Series. https://doi.org/10.1088/1742-6596/1104/1/012021
[3] Souza, C.E.S., Bachynski, E.E., 2019. Changes in surge and pitch decay periods of floating wind turbines for varying wind speed. Ocean Engineering 180, 223–237. https://doi.org/10.1016/j.oceaneng.2019.02.075
[4] Haslum, H., Marley, M., Skaare, B., Andersen, H., 2020. Aerodynamic Roll-Yaw Instabilities of Floating Offshore Wind Turbines, in: Volume 9: Ocean Renewable Energy. Presented at the ASME 2020 39th International Conference on Ocean, Offshore and Arctic Engineering, American Society of Mechanical Engineers, https://doi.org/10.1115/OMAE2020-18273
[5] Thys, M., Souza, C., Sauder, T., Fonseca, N., Berthelsen, P.A., Engebretsen, E., Haslum, H., 2021. Experimental investigation of the coupling between aero- and hydrodynamical loads on a 12 mw semi-submersible floating wind turbine, in: Proceedings of the ASME 2021 40th International Conference on Ocean, Offshore and Arctic Engineering. https://doi.org/10.1115/OMAE2021-62980
[6] Fonseca, N., Thys, M., Berthelsen, P.A., 2021. Identification of wave drift force QTFs for the INO WINDMOOR floating wind turbine based on model test data and comparison with potential flow predictions. J. Phys.: Conf. Ser. 2018, 012017. https://doi.org/10.1088/1742-6596/2018/1/012017
[7] Bachynski, E. E., Thys, M., Sauder, T., Chabaud, V., and Sæther, L. O., 2016, “Real-Time Hybrid Model Testing of a Braceless Semi-Submersible Wind Turbine: Part II — Experimental Results,” Volume 6: Ocean Space Utilization; Ocean Renewable Energy, ASME, Busan, South Korea, p. V006T09A040. https://doi.org/10.1115/OMAE2016-54437
[8] Bachynski, E.E., Chabaud, V., Sauder, T., 2015. Real-time Hybrid Model Testing of Floating Wind Turbines: Sensitivity to Limited Actuation. Energy Procedia 80, 2–12. https://doi.org/10.1016/j.egypro.2015.11.400
[9] Sauder, T., Alterskjær, S.A., 2022. Hydrodynamic testing of wind-assisted cargo ships using a cyber–physical method. Ocean Engineering 243, 110206. https://doi.org/10.1016/j.oceaneng.2021.110206
[10] Sauder, T., 2021. Empirical estimation of low-frequency nonlinear hydrodynamic loads on moored structures. Applied Ocean Research 117, 102895. https://doi.org/10.1016/j.apor.2021.102895
Comments
No comments yet. Be the first to comment!