India will in 2023 become the most populous country on Earth. In a world where the demand for food and energy is growing, it is very important to use technology that can fulfil the needs with the lowest use of energy possible.
The Norwegian-Indian project INDEE+ contributes to a sustainable transition to environmental and climate friendly working fluids in heat pumps and refrigeration systems. This research project will help school meal factories, hotels, seafood factories and more reduce their costs and emissions by introducing state-of-the-art technology.
After years of covid and restrictions, the INDEE+ team was finally able to meet in India in December 2022. Here, we visited three demonstration sites, where refrigeration/heat pumping systems with natural working fluids will be applied. In addition, three educational units with CO2 as working fluid are being developed.
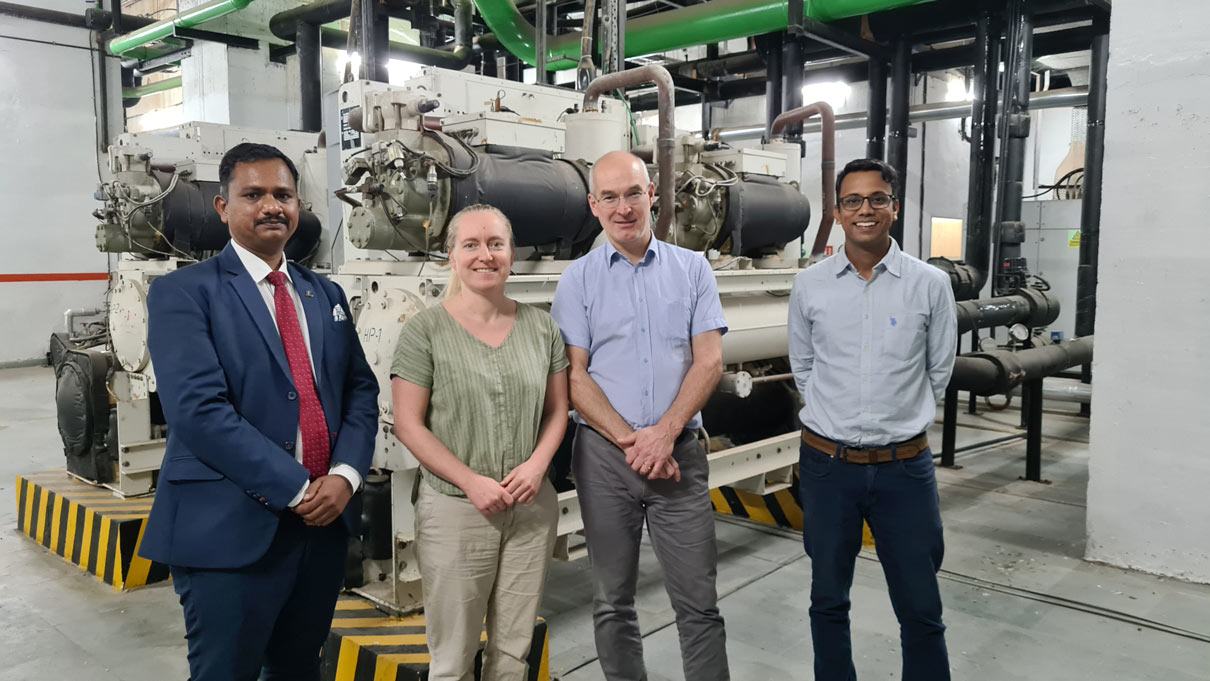
Perfect for a hotel in Goa
The first demonstration is related to hotels. Hotels have a large need of comfort cooling and tap water heating. This is a perfect combination for a CO2 heat pump/chiller, because it efficiently provides both heating and cooling at the required temperature levels.
A hotel is under construction in Goa, where such a unit will be implemented (see photos). The development of these CO2 units will be done with Indian manufacturers, creating value in the country, with assistance from the INDEE+ team in all phases from design to commissioning and follow up.
Seafood factories need efficient freezing
The second demonstration is related to seafood refrigeration. India is catching and producing a large amount of seafood, where some is eaten locally, and some is exported. Exported products need to be frozen quickly after harvest. As in Norway, this is commonly done in blast freezers with ammonia (a natural refrigerant) as the refrigerant.
There are, however, voices that are being raised now saying that ammonia is dangerous and should be exchanged. It is true that if ammonia leaks uncontrolled, there might be a risk for human health. On the other hand, ammonia as a working fluid is one of the most energy-efficient fluids and can also be handled well and safely, with proper education and training, as is the case in Norway.
The alternative is to have a cascade system, where one part contains ammonia at significantly reduced charges (as ammonia has excellent efficiency!) and another part containing CO2. CO2 systems are compact, and the fluid is transported in small-diameter tubes to where it is needed (also close to people and food).
The location of this demonstration is in Kochi, Kerala at BellFoods. Three vendors want to provide the refrigeration system and it is for the owner of BellFoods to decide which to go for.
70 000 school meals a day
The third demonstration site is a school meal production facility in Bangalore. Every day, 70 000 meals are produced on this site and delivered to schools nearby. To produce the steam they need for cooking, they have used fossil fuel boilers, but they will install a CO2 heat pump soon. They will still need the boilers for producing the steam, but the heat pump can heat the water to 85°C, reducing the total primary energy demand. Steam producing heat pumps are under development in Norway and will be implemented in the school meal facility in the next phase.
Education and training
Three educational units are located at INDEE+ project partner institutes: BITS Pilani, CIFT Kochi and IISc Bangalore. They have received prefabricated CO2 units which they will refurbish, develop and use for training and education. Equipment like ejectors and various heat recovery and AC options will be tested, and this will also be of interest for the equipment manufacturers.
Why should we use natural refrigerants?
There are many different working fluids, also known as refrigerants, with different properties. It is common to divide them into natural and synthetic fluids. The natural fluids have been utilized in refrigeration systems for a very long time and they are often produced as by-products of other processes. The synthetic working fluids are produced mainly for this purpose, and there are only a few companies across the world that produce them. A large part of scientists and manufacturers in the field are unanimously convinced that the only way forward is to use natural working fluids in heat pumping systems in new equipment.
What about the new working fluids, the HFOs? They have no ozone depletion potential and a very low global warming potential (GWP). The reason they have a very low GWP (which is calculated for 100 years) is that they decompose rather quickly – some are only stable in the atmosphere for a bit more than 10 days. However, they do not disappear. As for HFC 134a, most of these low GWP fluids decompose into HF and TFA, and will soon be restricted by an upcoming EU regulation under REACH (Registration, Evaluation, Authorisation and Restriction of Chemicals).
The history of refrigeration
If we make a short journey through history, in the beginning of refrigeration we used natural refrigerants such as CO2, ammonia and ether. In the 1930s though, the freons were introduced (R12 and later R22). These working fluids had good properties, so the demand increased quickly. In the 70’s it was discovered that they have a significant role in ozone depletion and a phase out plan was established with the Montreal protocol.
New synthetic refrigerants, the HFCs, were developed, now without the ozone depleting potential. However, it didn’t take many years until it was discovered that those have global warming potential. The next agreement was then the Kigali amendment, which is an international agreement with a goal of achieving over 80% reduction in HFC use by 2047. A consequence of this was again new forms of synthetic refrigerants, the HFOs, which have low global warming potential, but only because they decompose quickly. The decomposition products though, HF (hydrogen fluoride) and TFA (trifluoroacetic acid), are far from harmless, and can be dangerous both to people and the environment.
These agreements and others will hopefully initiate a new era and a great chance to stop using synthetic refrigerants, allowing us to focus on the introduction of natural working fluids in new sectors and new equipment.
India has great opportunities
Is this transition to natural working fluids only necessary for India? No, definitely not. We see the need for information, education and development in all countries. The difference between Europe and India is that in Europe, we already have some regulations, whereas India has more time to implement similar regulations and restrictions. Does that mean that they can relax and wait? Not if they are interested in national development and building up their own manufacturing industry able to support the global market with innovative and energy-efficient products. This is the potential for them to be self-reliant and ahead of the refrigerant phase-down progress.
INDEE+ team: NTNU, SINTEF, Miljødirektoratet (NEA), IIT Madras, IISC Bangalore, BITS-Pilani, CIFT, CEEW
Comments
No comments yet. Be the first to comment!