Bloggers: Mari Voldsund and Kristin Jordal
The 8th Trondheim conference on CO2 capture, transport and storage was held on June 16-18. The conference was organised in collaboration between NTNU and SINTEF, under the umbrella of the BIGCCS research centre.
Representatives from the Horizon2020 project CEMCAP (coordinated by SINTEF Energy research) was present during the conference with the purpose to present the project and be updated on other progress in the field of CO2 capture from cement.
No doubt that CO2 capture will be needed, the question is how
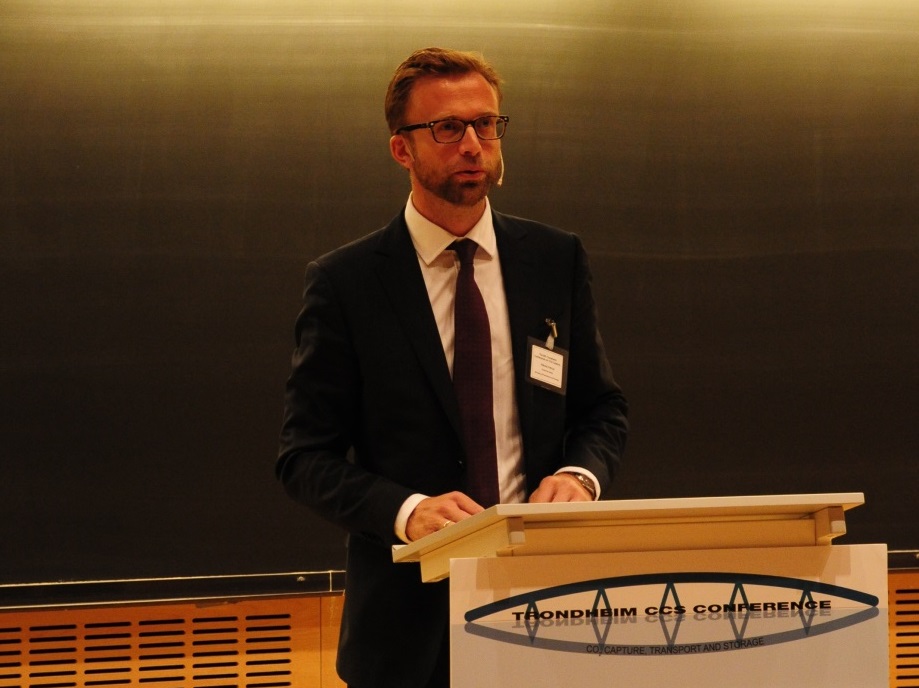
The increased attention to CO2 capture from the cement industry was evident from the start. Nikolai Astrup from the Ministry of Petroleum and Energy presented Norway’s strategy for CCS deployment and stated that there is no doubt that CCS will be needed, the question is how. He also emphasised the importance of CO2 capture from industry, and highlighted the Norcem CCS project as an example of the necessary industrial involvement in CCS.
Further on, CO2 capture from cement production was the topic in several of the presentations in the technical sessions.
Case: Norcem Brevik
Ragnhild Skagestad from Teltek presented five feasibility case studies on CCS (CO2 capture, transport and storage) in the Nordic region, carried out through the NORDICCS networking platform. One of the case studies includes the Norcem cement plant in Brevik. For the case of the Brevik plant, Skagestad said that the transport could be carried out either with ship or pipeline for storage in the Gassum or Utsira formations. The area around Skagerrak is interesting for a CCS cluster, due to several large point sources of CO2 nearby.
It is the first project where several CO2 capture technologies are tested for the cement industry under realistic conditions for the same plant
A presentation on the Norcem CCS project (2013 – 2017) was provided by Liv Bjerge from Norcem. This is a unique project: It is the first project where several CO2 capture technologies are tested for the cement industry under realistic conditions for the same plant (the Norcem Brevik plant). Four technologies of different maturity have already been tested, namely amine absorption, solid sorbent, membrane separation and calcium looping.
The technologies are being evaluated with respect to capture rate, energy consumption, impact of gas impurities and costs. The project has the perspective that full scale CO2 capture does not necessarily imply a 100% capture rate. An alternative may be the capture rate that can be achieved by utilising the waste heat at the cement plant. Bjerge emphasised the testing of the amine absorption (provided by Aker Solutions) as a great success. The technology could capture CO2 with 2.7 GJ/tonne CO2 captured, and capture of more than 90% of the CO2 in the flue gas has been demonstrated. With use of Norcem plant waste heat only, 48% of the CO2 could be captured. (It must be commented on here that the Norcem plant has a particularly high potential for utilisation of waste heat due to its use of relatively dry limestone. Many other cement plants will not have this potential.)
1,5 month old: The CEMCAP project
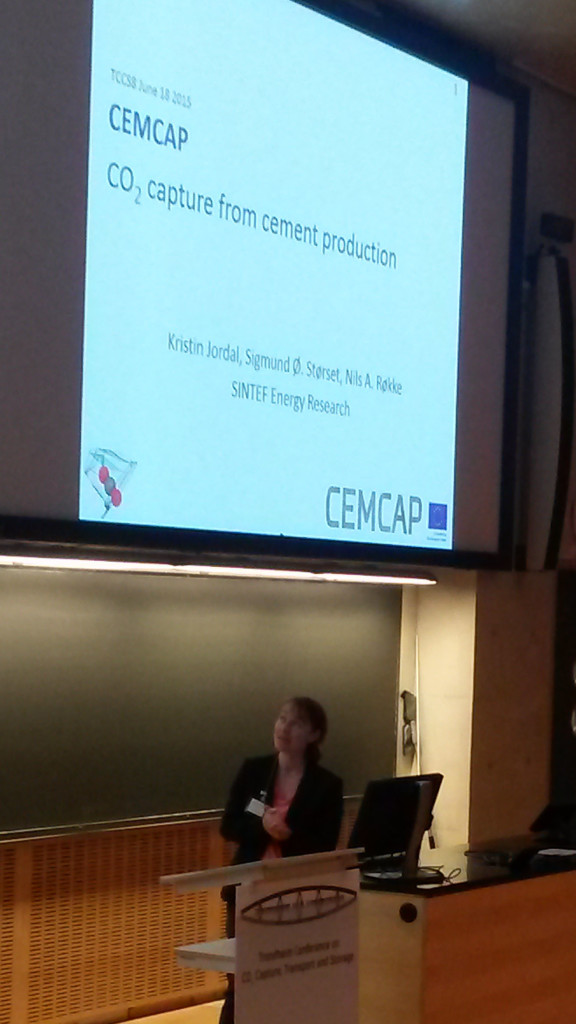
The CEMCAP project was presented by project coordinator Kristin Jordal from SINTEF Energy Research. The project started 1.5 months ago, so no results could be presented yet. An outline was provided on the necessity to implement CCS in order to reduce CO2 emissions from the cement industry. The connections to ongoing ECRA and Norcem CCS projects were explained: In the field of oxy-combustion capture (topic in the ECRA project) CEMCAP will test three key components required to enable oxyfuel capture from cement plants. In the field of post-combustion capture, CEMCAP will, under conditions relevant for cement plants, complement the Norcem project through bringing calcium looping further (de-risking study at the University of Stuttgart conducted in the Norcem project) and testing of the chilled ammonia (proprietary technology of Alstom Power) and membrane-assisted CO2 liquefaction technologies.
Altogether, the CEMCAP partners will work together to evaluate and compare four fundamentally different capture technologies. The overall CEMCAP objective is to prepare the grounds for CCS in the cement industry, and it is recognized that knowledge transfer is extremely important. A pool of CO2 capture expertise established in projects focusing on CCS in the power sector is in CEMCAP made available to the cement industry and must be exploited in the most purposeful manner.
The overall CEMCAP objective is to prepare the grounds for CCS in the cement
Calcium looping is promising for application in cement plants
Heiko Dieter from the University of Stuttgart IFK institute gave a general overview of the status of the calcium looping technology, before providing an insight into the experimental research to be conducted in CEMCAP. At the University of Stuttgart there is a 200 kWth pilot rig that will be utilised in the project. Dieter explained that calcium looping is even more promising for application in cement plants than for power plants, because limestone, which is used as sorbent in the calcium looping process, is the raw material for cement production. This allows the use of a higher amount of fresh sorbent, which potentially could have a positive impact on CO2 capture cost. Calcium looping will generate excess heat that should be employed for power generation, thus enabling cement plants to generate their own power.
Matteo Romano from Politecnico di Milano presented a study on CO2 capture in cement plants by calcium looping with entrained flow reactors. The work was conducted in cooperation with CEMCAP partner Italcementi. A new cement plant concept was presented, where the CO2 capture with calcium looping takes place in entrained flow reactors, and this process is integrated with the pre-calciner in the cement plant. The plant has a positive net power output due to an installed steam cycle, and simulations show the possibility to achieve a capture efficiency of up to 95%.
The work presented by both Heiko Dieter and Matteo Romano will be taken further in the CEMCAP project during the coming years.
It was inspiring to see the ongoing focus on CO2 capture from cement, to meet colleagues working in the field and to present the CEMCAP project to a scientific audience at TCCS8. CO2 capture from cement plants is research in progress – the attention to the topic is relatively new, but it is recognised that CCS will be required for significant emissions reduction from cement plants, since fuel switching alone is not sufficient. Fortunately, CO2 capture for cement plants can build on the extensive research already conducted for power plants.
Fortunately, CO2 capture for cement plants can build on the extensive research already conducted for power plants.
Comments
No comments yet. Be the first to comment!