In contrast with the static cables, the dynamic power cables must be flexible to withstand harsh environmental loads in complex water conditions, and this is where SINTEF’s expertise comes in.
The dynamic power cable is used to transport the electricity from the structures either bottom-fixed or floating used to support a wind turbine or solar panels to an offshore substation. The electricity is then transported from the offshore substation to land by use of a subsea cable.
RenewableUK’s “Offshore Wind Project Intelligence Report – Cables Edition” estimates the installation of over 63 200 km of array cables and nearly 40 000 km of export cables by 2030. Norway targets 30 GW of offshore wind capacity allocated by 2040. In total, Europe will need approximately 6000 km of subsea power cables to support its floating wind projects annually. Globally the need for safe and cheap dynamic power cables will be enormous.
The problem of fatigue
One of the most common failure modes for these cables is fatigue. Designing dynamic power cables against fatigue is challenging due to coupling of hydrodynamic response and structural behaviour of the cable. Vortex-induced vibration (VIV) is the most challenging hydrodynamic response characterised by its complex excitation processes, and the say so-called ‘stick-slip’ behaviour characterises the complex structural behaviour of the cable.
VIV is a complex fluid-structure interaction phenomenon caused by flow separation and vortex shedding. VIV, combined with wave loads and floater motions, may significantly affect the structural integrity and service life of power cables. Therefore, accurate prediction of VIV-induced fatigue is crucial in the design, installation, operation, and maintenance of these systems.
Dynamic power cables are composed of helically wound conductive metal cores encased in insulation, armoured for protection, and covered by a durable sheath. Additionally, fibre optic cables are often integrated into the design to enable communication, data transmission between shore and offshore energy farms, and sometimes real-time monitoring of cable conditions.
The dynamic power cables exhibit unique ‘stick-slip’ behaviour, a phenomenon where two surfaces in contact alternately stick (adhere) to each other and then slip (slide) past one another. This behaviour can occur in the internal components of the cable, such as the conductor, insulation layers, or metallic shielding, especially during bending, tensioning, or thermal cycling. It is often associated with frictional forces and energy dissipation. The resulting non-linear hysteresis bending stiffness and damping properties are critical inputs for accurate numerical modelling and prediction of the behaviour of these cables.
Optimising the design
Large safety factors were traditionally used for the design of dynamic power cables in the oil and gas industry due to the lower voltage ratings, fewer number of cables and the profitability of the business. With smaller margins in the offshore renewable energy sector and the need for larger volumes with cables, the interest for more optimised designs of dynamic power cables is increasing. At the same time, the dynamic power cables have to be rigorously designed and verified for their ability to maintain the structural integrity throughout their operational lifespan.
The complex excitation and structural behaviour of dynamic cables is difficult to simulate due to its non-linear behaviour. Empirical data is needed to improve our understanding and to support the development of simulation tools. These cables are difficult to study experimentally by scaled models due to scaling issues. Therefore, full-scale testing is the state-of-the-art method for obtaining realistic measurements of these properties and global responses at full-scale Reynolds number flow regimes.
The Marine Technology Centre at your service
SINTEF Ocean’s Marine Structures Laboratory and Ocean Basin are ideally suited for conducting full-scale tests on dynamic power cables, as well as other similar structures like flexible riser and umbilical for offshore oil and gas industry.
The Marine structures laboratory, the first laboratory in the new Norwegian Ocean Technology Centre, is used for testing model-scale and full-scale structures, structural components and materials (e.g., fatigue testing, ultimate strength and collapse testing).
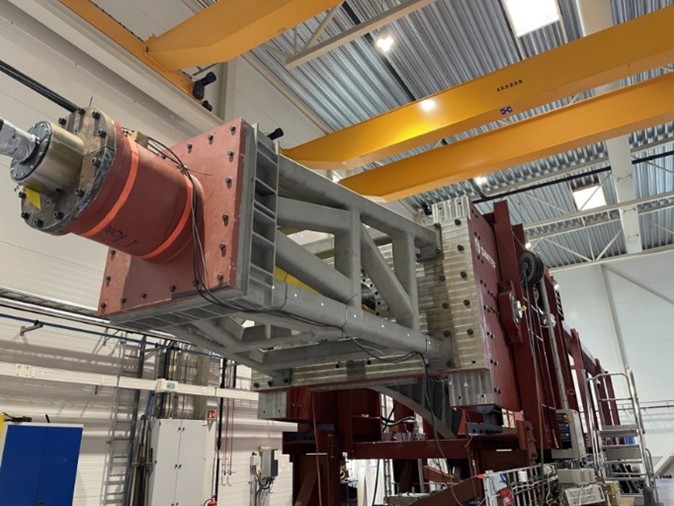
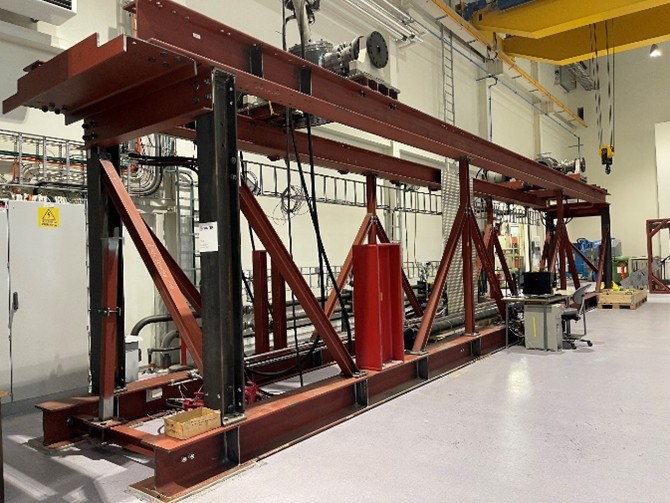
The Ocean laboratory is one of the largest hydrodynamic test facilities in the world, used for testing of ships and ocean structures from model to large scales. For cables, a specifically design rig can be used for towing of cables that are up to 30 m long. The cable is towed in the basin to simulate uniform currents with a speed range representing the design conditions. This offers an unparalleled ability to simulate real-world conditions and gather vital global response data.
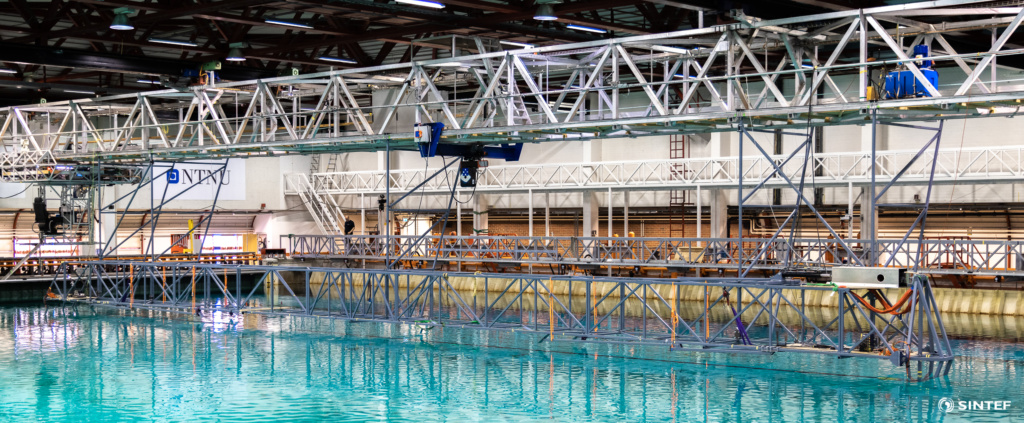
For testing of full-scale cables, SINTEF Ocean recommends starting with tests in the structure lab to document the mechanical properties of the cable. These properties are then used to select the optimal testing conditions for the ocean basin. The cable is then towed at different speeds in the ocean basin. The results from the mechanical and hydrodynamic tests are then used as input into our state-of-the-art simulation tools such as UFLEX, SIMA/RIFLEX/VIVANA and CONCORDIA.
Dynamic cable test capabilities of SINTEF Ocean’s laboratories
Marine structures laboratory | Ocean laboratory |
---|---|
Full-scale fatigue tests | Full-scale VIV/towing tests |
Full-scale compression/bending tests | Small-scale VIV/towing tests |
Small-scale tests | Full-scale bending tests |
The insights gained from testing in our laboratories, combined with decades of research, have been used to validate and improve our numerical tools, which are further used by the industry to ensure structure’s local and global behaviours of the cables satisfying the fatigue requirement.
With a proven track record in integrity verification for flexible risers, power cables, and umbilical for the oil and gas sector, SINTEF Ocean is uniquely positioned to support the offshore renewable industry. Through our cutting-edge structural and hydrodynamic testing, proprietary software, and deep expertise in structural behaviour, we offer valuable insights into the loads and structural responses of dynamic power cables at the component level, ensuring they meet the rigorous demands of offshore wind energy projects.
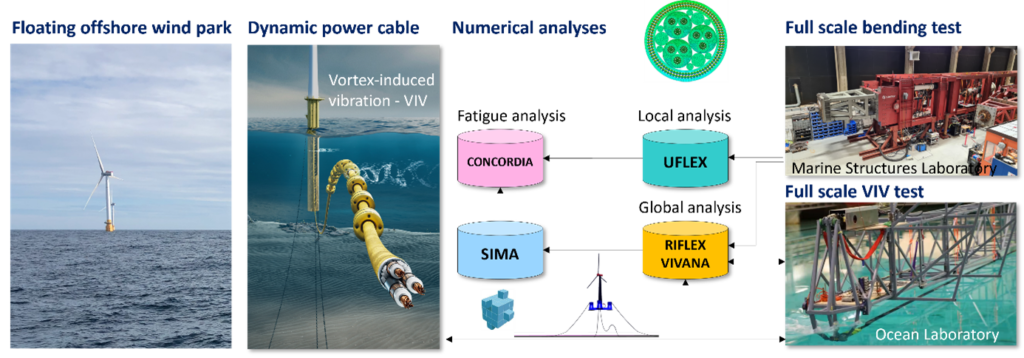
Comments
No comments yet. Be the first to comment!