With the end of 2014 coming closer, so is the end of the 6 year competence building project (KPN) Enabling Low-Emission LNG Systems (LELNG). SINTEF Energy Research, NTNU, Statoil, and GDF SUEZ have in this cross-disciplinary project joined forces to bring the natural gas industry closer to a more energy efficient liquefaction process.
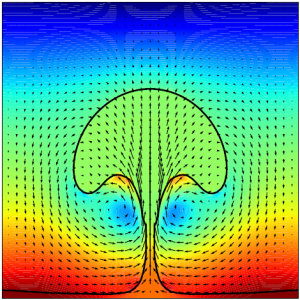
So, why did we initiate this project? According to the World Energy Outlook 2014 report, the natural gas demand will continue to grow in years to come. Natural gas will, according to some scenarios, pass coal and become the second-largest fuel after oil. For transportation over long distances, the natural gas is liquefied by cooling it down to around -160 °C. Liquefied natural gas (LNG) requires 600 times less volume than gas at room temperature, and is therefore the natural choice for ship transportation. Even though natural gas is an environmentally friendly energy source compared to oil and coal, the liquefaction process is power consuming and economically costly. Our project’s mission has therefore been to optimize the design and operation of the liquefaction process and one of the most power consuming and technically complex units of the process, the heat exchanger.
Inside the heat exchangers, the natural gas is cooled and, eventually, liquefied. By optimizing the natural gas liquefaction process in an economically feasible way, the power consumption, and hence CO2 emissions and ultimately climate impact of bringing the natural gas to the market can be reduced, and also make gas a more competitive alternative to its dirtier cousins oil and gas.
What has been the content of the project? To understand how to design and operate the complex process of natural gas liquefaction, an understanding of the underlying physical phenomena which govern the process is required.
Our project has really gone into the depth and developed models for and recorded experimental data on how droplets inside the heat exchanger interact with liquid films and pools, and with the heat transfer surfaces. In addition, experiments have investigated heat exchanger multiphase flow, and heat and mass transfer has been studied, as seen in Figure 1.
Such knowledge can be generalized such that it can be useful for the design and operation of heat exchangers. We have developed a heat exchanger model that not only considers the energy consumption of the process, but in addition include the size (footprint) and weight of the heat exchanger, two very important parameters in the oil and gas industry. The model is very robust and efficient, and can hence be used to reduce the energy consumption of the LNG processes. At the same time, it is detailed enough to uncover potential operational challenges. This sort of heat exchanger model is one of a kind and very attractive for the industry. The model has already been used to design heat exchangers for various applications.
Another direct link from the project to industrial applications is related to the combination of our knowledge of relevant physical phenomena and heat exchanger modelling into a process optimization framework.
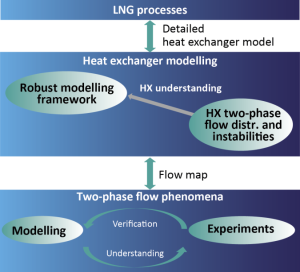
The project has developed a unique way of optimizing the entire LNG process and to compare the various processes in use today. Process optimization is a complicated field due to the high number of parameters involved and a large effort has been spent on evaluating and improving the existing LNG optimization techniques. The project has had the structure that is shown in Figure 2.
The Low-Emission LNG project is over soon. Even though the project has brought us a long way there is still work to do before we have deciphered all the relevant physical phenomena and provided the necessary basis for optimizing natural gas liquefaction process operation and design, which is of great importance both for Norwegian and global economy and the climate.
Hence, we in SINTEF Energy Research will continue the work needed to bring natural gas from exploration to market in the most efficient and environmentally friendly way
Comments
No comments yet. Be the first to comment!