The salmon farming industry is an example of a highly successful and profitable global industry, with Norway alone producing 1.1 million tons of salmon in 2020. However, with the growth in sea-based production, there is also a trend towards developing larger land-based facilities and tanks to address the increased need for smolt and make the fish more robust before transfer to sea. The industry is investing heavily in new technology, such as automated feeders, advanced camera systems, and robotic solutions, to improve efficiency, address specific challenges, and enhance fish welfare.
The land-based production segment of aquaculture in Norway is mostly focused on smolt and post-smolt producers, with a few exceptions for fully grown salmon. However, compared to the sea-based salmon farming industry, the facilities for smolt production are largely based on the same management principles and methods as the first-generation plants established in the 1980s, but on a larger scale. Many day-to-day operations are currently performed manually, with significant labor costs and potential for errors. It is therefore crucial to optimize the day-to-day management of smolt facilities through more optimized and autonomous operations, a notion that harmonizes with the ambitions of Industry 4.0. Addressing the issues through exploration of new technology and automation solutions to improve efficiency, reduce costs, and minimize errors. The utilization of new technological solutions and automation principles can be aimed to be incorporated in a holistic way, making use of the precision fish farming (PFF) concept and moving towards Industry 4.0, to improve objectivity in all stages of smolt production. The overall goal is still the same as before. To ensure fish welfare, optimize production at low costs and low environmental footprint, and to minimize the need for human personnel in operations that are dangerous, dirty, or dull.
Industry 4.0 and smolt production
The fourth industrial revolution, Industry 4.0, refers to the integration of cyber-physical systems and digital technologies into all aspects of production, business, and customer experience. Other industries such as oil and gas, automotive, and agriculture are motivated by the benefits of Industry 4.0, and are adapting their business models to incorporate digitalization, big data, IoT, automation, and other technologies. We have seen that some aspects of Industry 4.0 are already being implemented in the sea-based aquaculture industry (e.g., feeding cameras and automatic net cleaners) in sea cages. The goal of these efforts is to improve monitoring, control, documentation of the biological processes in fish farming activities, increase production and overall effectiveness, and ensure a healthy environment and welfare both for the fish and workers. Land-based fish farming has also seen the benefits of utilizing technological advancements, but has not yet fully adapted an Industry 4.0 approach. The industry needs to shift from a case-by-case practice to a more holistic approach through the adaptation of technology to fully exploit the benefits of Industry 4.0. A realistic way to achieve this is to mimic other industries and target the research needs in the context of land-based fish farming. Moreover, this industry should strive to adapt an Industry 4.0 model to not only change how products and services are produced, but also to adapt their business models for increased efficiency and effectiveness.
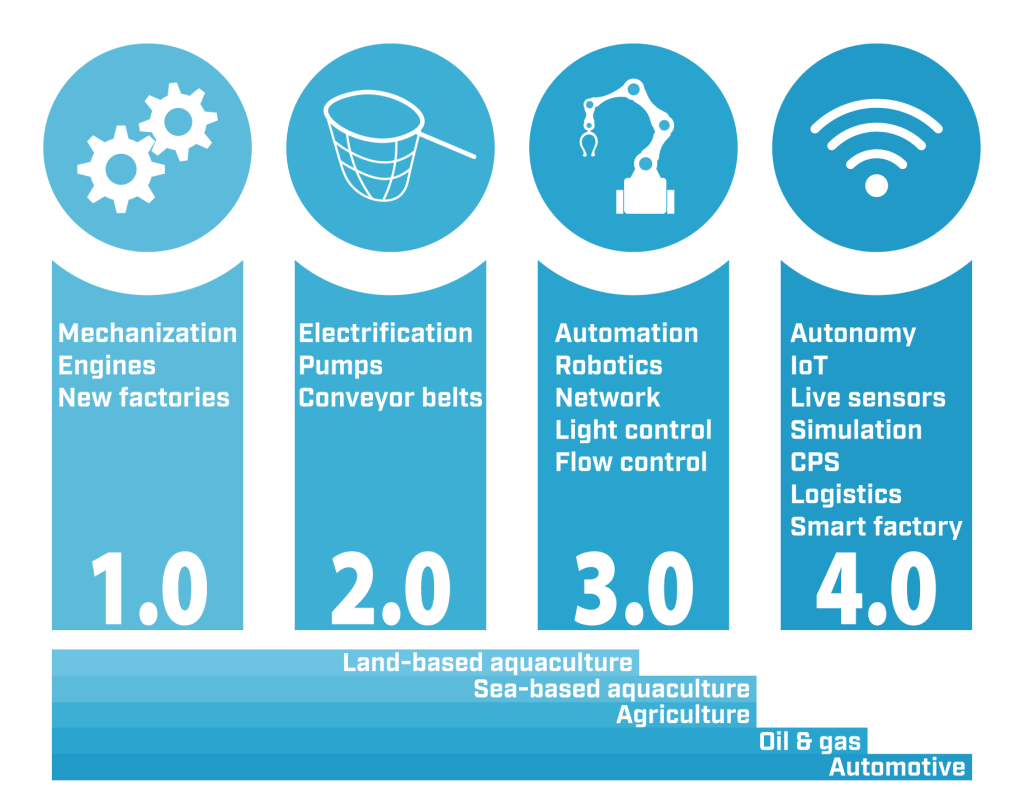
Current status and challenges
Some of the most common operations in smolt production and insights into their current level of automation can be found below. It is important to know that while systems for automating certain operations have been developed, most operations still rely on manual labor. This work can be tedious, risky and increases the probability of errors or undesired consequences such as leakages, fish mortality, escapes, or sub-optimal feeding.
Water quality monitoring
Ensuring high water quality is critical for the fish. Some of the most important water quality parameters for fish farming can be measured continuously using sensors in the tank while other parameters must be found through laboratory analyses. Sensors suffer from fouling and measurement drift, leading to low reliability and need for maintenance and calibration. Sensor data are usually interpreted manually but serve as excellent candidates for automation when fused together and when cross-referenced with desired parameter values and production plans.
Sensor equipment maintenance
Equipment maintenance mainly involves cleaning, removing biofouling, equipment disinfection, changing wear parts, and periodic sensor calibration. Unfortunately, calibration and maintenance of equipment is time-consuming and may lead to production downtime, and is currently done manually.
Light and temperature control
Light and temperature are used to simulate circadian and seasonal variations and affect social interactions, resting behavior, exploration, and feeding and to improve control over the production. Light and temperature requirements typically follow production plans but may also be used together with decision support systems related to fish behavior and health for optimal light and temperature conditions.
Fish population monitoring
Daily inspection is typically done by employees visually inspecting the population directly or through cameras. Some companies use cameras with computer vision and machine learning systems. Understanding fish behavior and detecting indicators of reduced welfare (e.g., wounds, deformities, potential disease indicators, dead fish) relies heavily on the observer (human or machine). The increase in tank sizes in the industry also makes manual inspection more difficult.
Splitting and sorting biomass
Size grading and sorting machines are commonly used to keep the size of the tank population as uniform as possible, which entails using specialized equipment to transport fish onto a horizontal surface grid and into differently sized holes based on their size. Sorting may also be done automatically during vaccination using machines. However, manual labor is still needed to set up the equipment and determine when to start the process. Sorting also involves handling the fish, which may impact welfare.
Dead fish and waste removal
Dead fish and waste materials such as uneaten feed particles and feces accumulate in the tank over time and need to be removed from the tank to avoid detrimental water quality. Dead fish are typically removed manually when floating on the surface or using an installed dead fish collection system, while waste is often removed using filters on in- and out-flux water or surface treatments applied to the tank wall. In the end, ensuring that the dead fish are removed and applying surface treatments to the tank wall are still necessary to do and are currently fully manual processes. Moreover, existing systems for automated waste collection may be difficult to install after a facility has been built. Managing the collected waste and dead fish also poses challenges related to deposition or recycling/reuse of these in further value chains.
Tank cleaning
Periodic cleaning of tanks is necessary to maintain water quality. This is usually done manually using high pressure hoses and other cleaning equipment between production cycles and may increase the downtime of the tanks leading to reduced productivity. High-quality cleaning with minimal physical stress on human personnel and minimal downtime of the tanks is challenging to achieve. Other methods, such as lowering the water level and cleaning exposed parts of the tank, are generally not desirable as waste particles from the tank walls may detach and enter the tank before being removed by the flow. The same applies to solutions where the population is moved to a temporary holding tank while cleaning takes place, as this is labor intensive and can be stressful for the fish.
Biomass estimation
Biomass estimation is a challenge in the aquaculture industry generally. The most common method involves manually catching a representative number of fish, weighing them and extrapolating the weight of the entire population, but this is stressful for the fish and may be highly inaccurate. Camera-based biomass estimation systems using computer vision are also being used and some are already in the market for sea-based aquaculture.
Vaccination
Vaccination is mainly achieved using vaccination machines that both dose and deliver vaccines autonomously. These units use computer vision to detect the fish and decide where to place the syringe, providing highly accurate biomass results and population numbers because all fish are handled individually.
Feeding
Feeding is the most important operation that takes place. The amount of feed needed for each individual fish depends on factors such as fish size, feed composition, and water quality parameters, and the feed size increases as the fish grow. While feed is usually distributed to the population by automated dispensers, the amount of feed delivered to each tank is usually a subjective decision based on observations and experience, and the dispensers typically need to be filled manually. The sea-based farming industry is investigating different products that exploit machine learning to estimate the required feed amount in a more objective and automatic fashion, but these are not yet adapted to tanks. Some fully automated feeding systems that hold feed of various sizes exist, but have yet to see widespread use by the industry.
Smoltification tracking
The industry mainly employs two strategies for determining smoltification degrees in farmed fish: sampling gill tissue for laboratory analysis or exposing individuals to saline water and analyzing the sodium chloride content in blood. Both methods, which are done manually, are invasive and have negative impacts on fish welfare. New methods such as hyperspectral imaging coupled with machine learning have been proven to estimate smoltification with high accuracy but are not yet ready for industrial application. Desmoltification is a general challenge that can cause major mortality events and other challenges, and thus, there is a strong motivation for accurately assessing when the metamorphosis has taken place.
Autosmolt2025 project
The Autosmolt2025 project aimed to create the foundation for future unmanned, self-rearing and cost-effective smolt production systems. The ultimate vision of the project was to adapt and develop a holistic approach to the next generation of smolt production by applying the principles of Precision Fish Farming (PFF) at different stages of the smolt production cycle, bringing smolt production closer to realization within the framework of Industry 4.0. This included increasing the level of autonomy and objectivity in smolt production operations to reduce dependencies on manual labor and subjective assessments, and to improve accuracy, precision, and repeatability. The project was led by a global leader in aquaculture technology (Scale Aquaculture AS) and involved collaboration with three salmon farming companies (Sinkaberg-Hansen AS, Salmon Evolution AS, and Andfjord Salmon AS), a world-leading supplier of smolt production tank systems (Brimer AS), companies with expertise in autonomy and sensor technology (Wago Norge AS, Festo AS, and Posicom AS) and two research partners (SINTEF Ocean AS and NTNU).
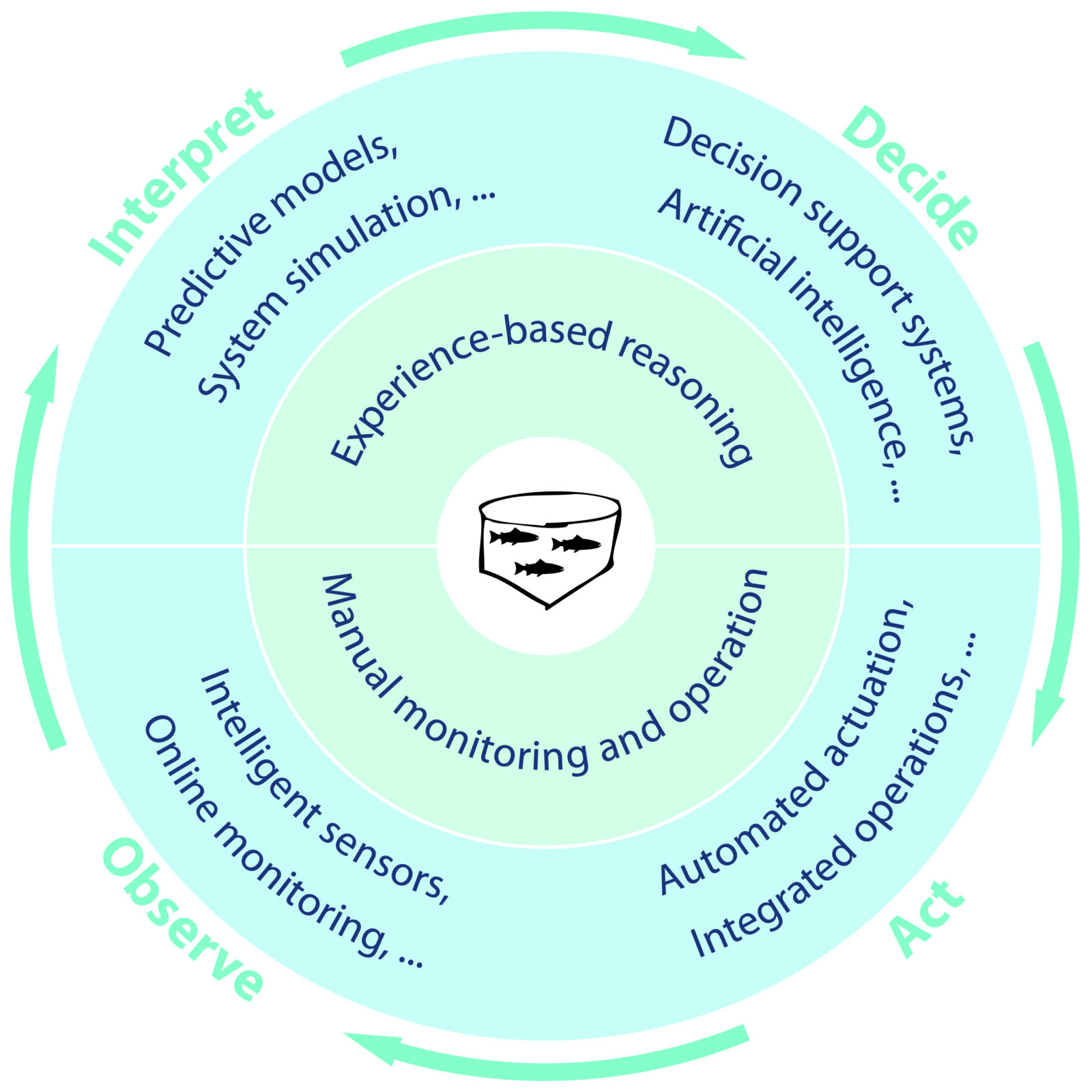
The project sought to adapt a holistic approach to smolt production through the development of novel technology for data collection and analysis, autonomous operations, and maintenance by targeting the following objectives:
- Developing a holistic approach and derive specifications, conditions and requirements for optimized and autonomous smolt production facilities
- developing sensor packages and algorithms for online data collection and processing of environmental conditions and welfare-related parameters for self-monitoring rearing tanks in smolt production
- developing concepts for modular and flexible robotic tools and tool carriers for autonomous tank operations
- validating technologies, methods, and concepts through laboratory and full-scale demonstrators featuring case studies relevant for real-world smolt production.
Directions for optimized production
The Autosmolt2025 project surveyed the project partners to share practices and thoughts on the topics of automation principles, how technologies are used in smolt production today, what tools they foresee serving to improve future operations, and optimized smolt production. The questionnaire results showed that the industry can benefit from more objectivity and automation in tasks such as water quality monitoring, fish population monitoring, physical in-tank operations such as dead fish and waste removal and cleaning, and decision making to increase production. To address these needs, three case studies were proposed: self-monitoring rearing tanks, autonomous tank operations, and Smolt 4.0 – a holistic system for high level decision making based on data from self-monitoring tanks.
Self-monitoring tanks
The core technologies needed to develop self-monitoring tanks have existed for some time and have successfully been applied in other industries. Base components are sensors that quantify important variables in the tanks and communication systems for transferring sensor data to a centralized hub. The hub should be responsible for collecting, processing, and storing the collected data. Typical sensors may be cameras for visual observation (for inspection of fish behavior, cleanliness of the tank, detecting dead fish, status of nearby equipment, etc.) and water quality sensors (e.g., for pH, dissolved oxygen, nitrates, CO2, and more). A combination of sensor data may provide better insight into the overall production systems and the health of the fish. Moreover, the data can be linked to alarm systems, may be presented directly to the user for decision making, and may also be valuable for autonomous tank operations.
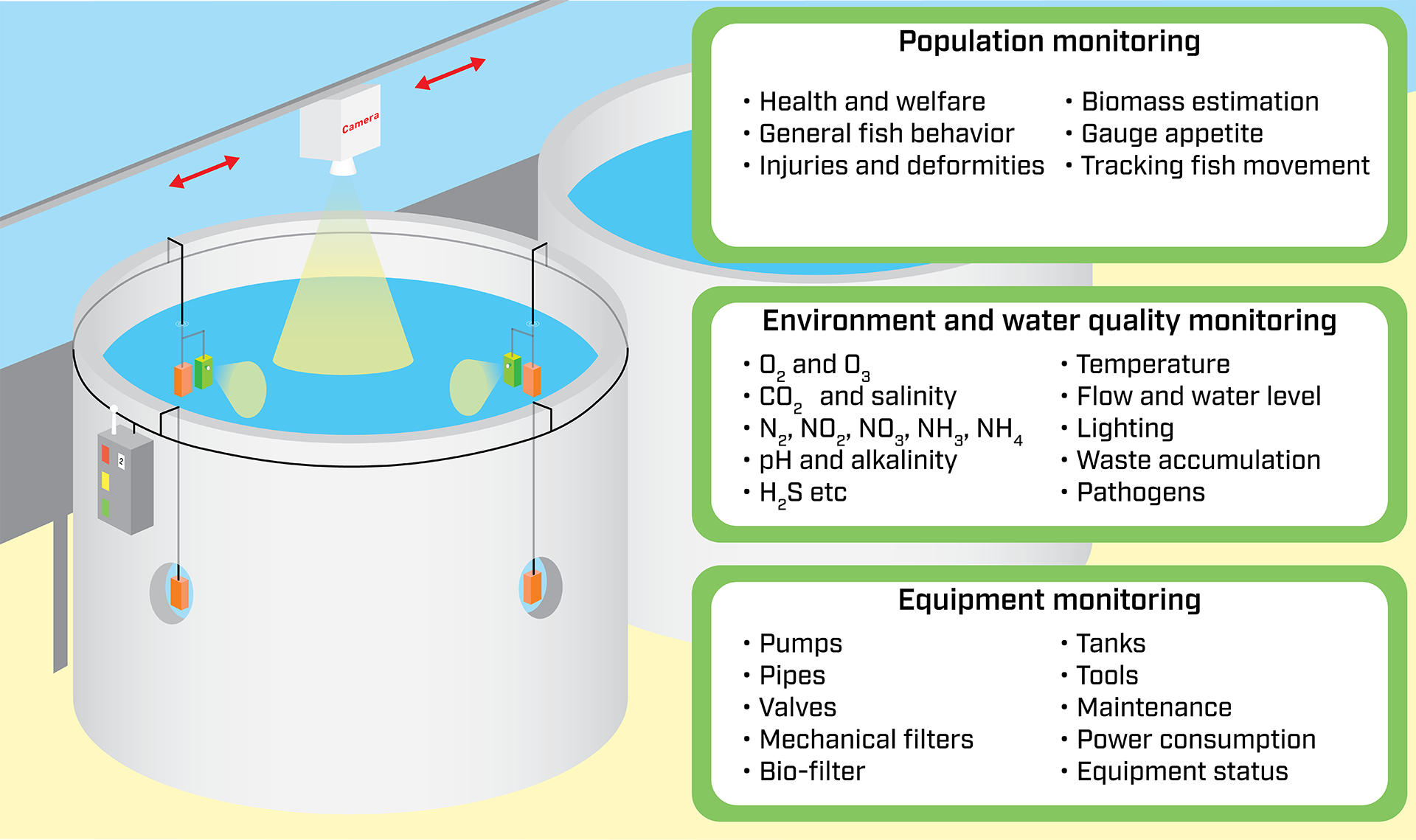
Autonomous tank operations
There is a foundation for automatic or autonomous tank operation based on available sensors and equipment that exist commercially. For instance, tank operations may require robotic vehicles able to navigate near or within a tank and robot manipulator arms for underwater use, and sensors that give the robotic systems a way of perceiving the environment. This would be crucial both to ensure that the operation is executed properly (e.g., by monitoring the results), and to ensure that the operation is as gentle and non-invasive as possible with respect to fish and structural integrity. Based on the importance and labor intensiveness of tank operations, three key application areas of autonomous tank operations are feeding, tank cleaning, and dead fish removal.
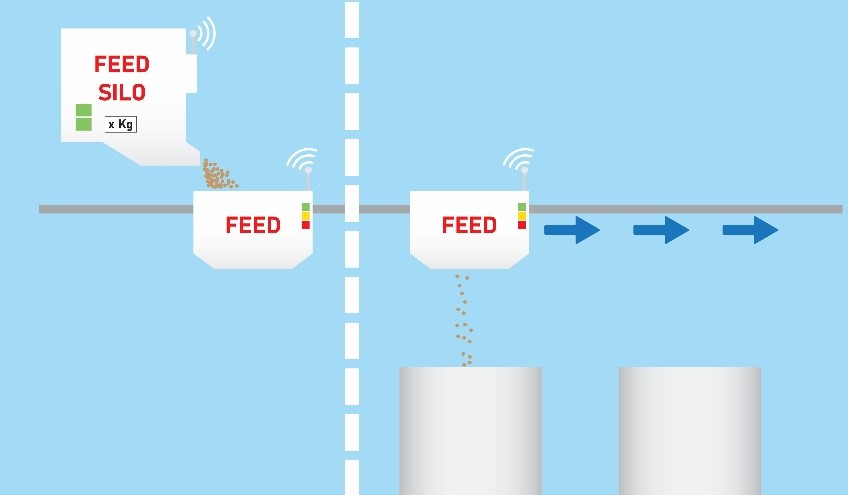
Autonomous feeding operations involve the use of complex systems that combine actuation and intervention technology with monitoring and sensing systems to transport and dispense feed to fish, choose the proper feed dose and type, and estimate fish appetite. Some automatic feeding systems already exist and can serve as a foundation for an autonomous system. These systems could enable feedback control for feeding based on fish appetite and reduce labor for manual tasks such as filling feed containers.
An autonomous cleaning system would identify when cleaning is necessary, initiate and perform the cleaning, collect excess waste, and get approval before the tank can be used again. Cameras with computer vision and machine learning methods could be used to estimate cleaning waste and determine when cleaning is necessary. The cleaning activity could be executed by a continuously moving cleaning system, a robotic manipulator, or a self-propelled robotic system equipped with cleaning tools. There are also commercial solutions that could be useful components in such systems, such as units mounted on the tank that clean walls and floors, autonomous underwater vehicles for cleaning and inspecting tanks, and moving cleaning vehicles. Autonomous tank cleaning operations would enable a more continuous and less labor-intensive cleaning process that improves water quality and provides a healthier environment for the fish.
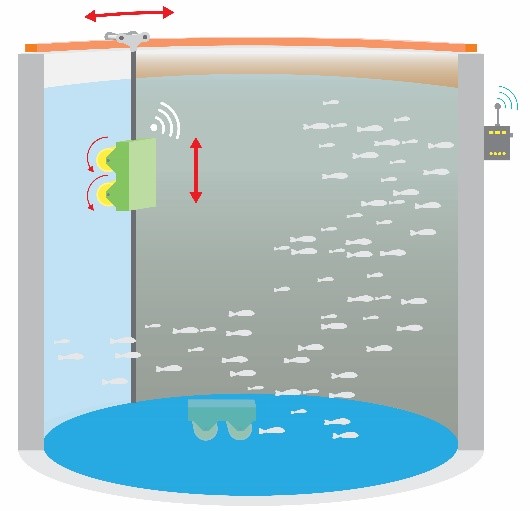
Autonomous dead fish removal involves the use of robotic solutions that can detect, verify if a fish is dead, and remove it. The main components of such solutions would be suitable robotic tool, perception systems, and software that allow for safe and efficient operations. This requires a manipulator with soft grippers and algorithms for planning and executing the motions and grasping. Autonomous systems that continuously search for and remove dead fish would likely improve the production environment by reducing the potential for pathogens and unwanted substances, as well as improve health safety and environment (HSE) conditions by reducing labor and dirty work.
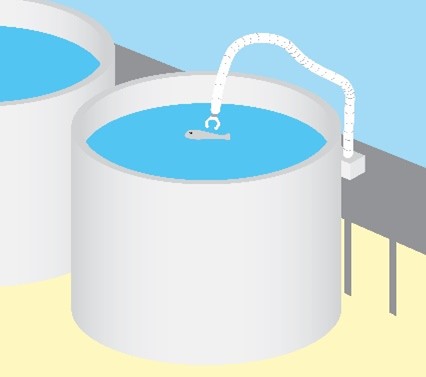
Smolt 4.0
Smolt 4.0 represents an innovative and holistic approach to smolt production that combines self-monitoring tanks, autonomous tank operations, and high-level decision support within the Industry 4.0 framework. This fully integrated system should continuously gather data, produce reliable estimates of the current status and predictions, and apply these for environment and population control purposes. This would lead to the production of robust, high-quality smolt while also ensuring the welfare of both fish and employees. At the core lies also the opportunity to achieve repeatability in production by allowing farmers to keep production conditions similar across batches. The illustration of such a system can be seen in the figures below.
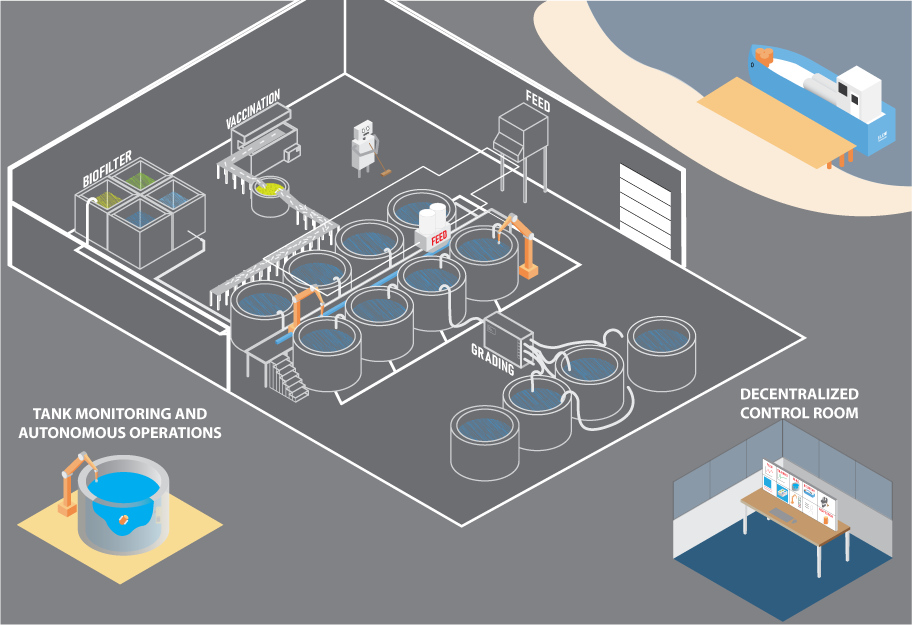
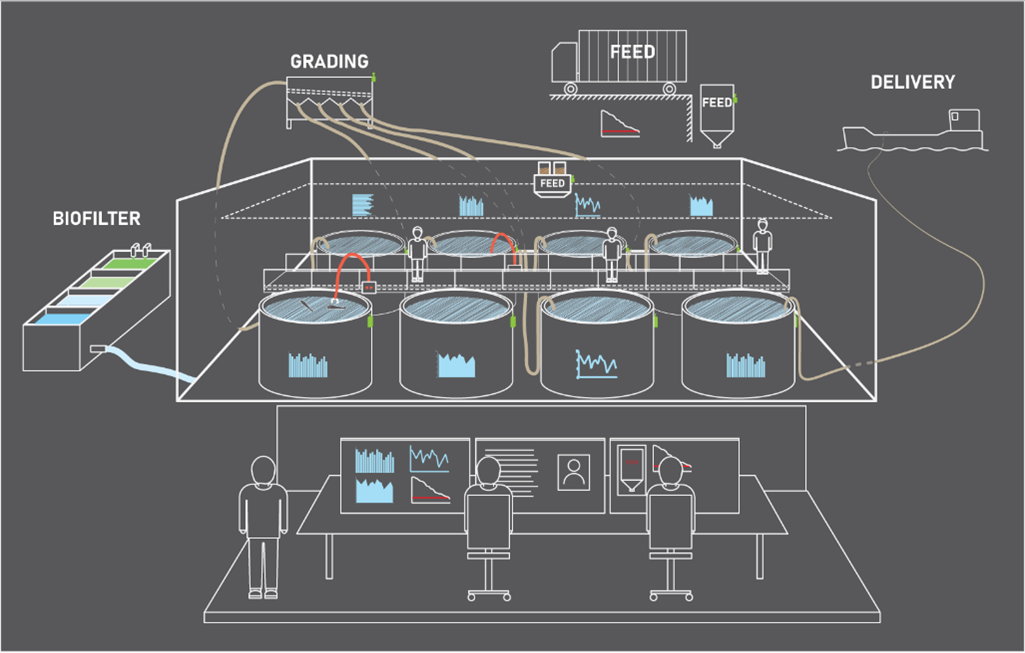
The Seatonomy method, which represents a structured framework for analyzing challenges related to automation in marine environments, has been used to analyze the application of Smolt 4.0 in greater detail and specify the design requirements. Based on these results the specifications and requirements for self-monitoring rearing tanks and autonomous tank operations were found, which can be used to realize Smolt 4.0.
An autonomous tank system should continuously monitor all aspects of production and automate sensor maintenance and calibration to reduce personnel workload and ensure high-quality data. The system should also be able to analyze trends, make predictions, and provide decision support for personnel and autonomous tank operation tools. The system should be able to visualize and present data in an intuitive manner for personnel and provide 24/7 monitoring and inspection of the full facility. An alternative solution could be to combine integrated sensors and automated laboratory stations from different providers and producers in a common system, either as a single unit deployed at single tanks or a more modular system that could be shared between rearing tanks. Autonomous tank operation systems should be able to carry out various tasks such as cleaning, feeding, and removing dead fish in a fish farm, in accordance with the production plan. The system would have the ability to switch between tasks quickly and decide on the order of operations if multiple tasks are deemed necessary at the same time. The system would require perception systems for environment interpretation and manipulation/intervention tools to carry out the tasks. For example, the feeding operation would require a device for delivering feed to the tanks, and the system should be able to detect when the fish are hungry and decide on the type and size of feed suitable for the tank population. The cleaning operation would require tools to clean the tank wall and any other surface of interest, and the dead fish removal would require a manipulator to grasp the dead fish. A possible direction to achieving this could be a self-propelled robotic tool with the ability to exchange its end effector tool to suit the given operation. This could be a cost-efficient solution that is easy to integrate into existing facilities, as well as newer facilities, and could be set up to do both cleaning and dead fish removal. In any case, the system should be able to be initialized and supervised from a central control room that also stores and uses the data and logs as historical data for decision support systems and future production planning. Safety precautions such as self-localization, collision avoidance systems, and emergency shutdown protocols must also be considered in the design of the system.
While the Smolt 4.0 concept comprises self-monitoring tanks and autonomous tank operations, it also needs to account for other practical aspects such as fish logistics and streamlining the acquisition of parts, feed, and vaccines. These are all important factors in determining production efficiency and precision, and research in optimizing logistics in the manufacturing industry could be transferable to the aquaculture industry. Improved logistics can also reduce production costs by enabling farmers to purchase parts and feed at low prices, as well as reducing the time personnel must spend on logistics tasks, allowing them to focus on more complex production-related tasks.
Vision for the next generation of Smolt production units
The land-based fish farming industry has a great potential to increase automation and efficiency by adopting Industry 4.0 principles from other industries. Advanced technological solutions and new products are needed to improve the efficiency and profitability of smolt production facilities while also reducing the need for employees to perform dirty, dull and dangerous tasks, making the industry more future-oriented, competitive, and ethically sustainable. The concept of Smolt 4.0 is proposed as a solution to achieve this. SINTEF targets to utilize the PFF concept and develop the required systems and technologies with the industry in order to realize more autonomous and digital solutions for land-based fish farming.
Comments
No comments yet. Be the first to comment!