Global annual production of red mud (bauxite residue) is about 150 million tonnes. It contains raw materials for the production of iron, silicon and aluminium, and is dumped as waste in spite of the availability of recycling technologiesbauxite residu. This is because it is cheaper to dump bauxite residue as waste and continue mining for new ores. Is this sustainable?
- Authors: Halvor Dalaker, Senior Research Scientist at SINTEF Industry, Birgit Ryningen, Research Scientist at SINTEF Industry and Casper van der Eijk, Research Manager at SINTEF Industry
What is bauxite residue?
Bauxite residue, or red sludge, appears in the news from time to time. We hear about dams in danger of bursting and disposal sites where bauxite residue is seeping into the environment. But what is bauxite residue? And why do we find such large bauxite residue settling pools scattered around the world?
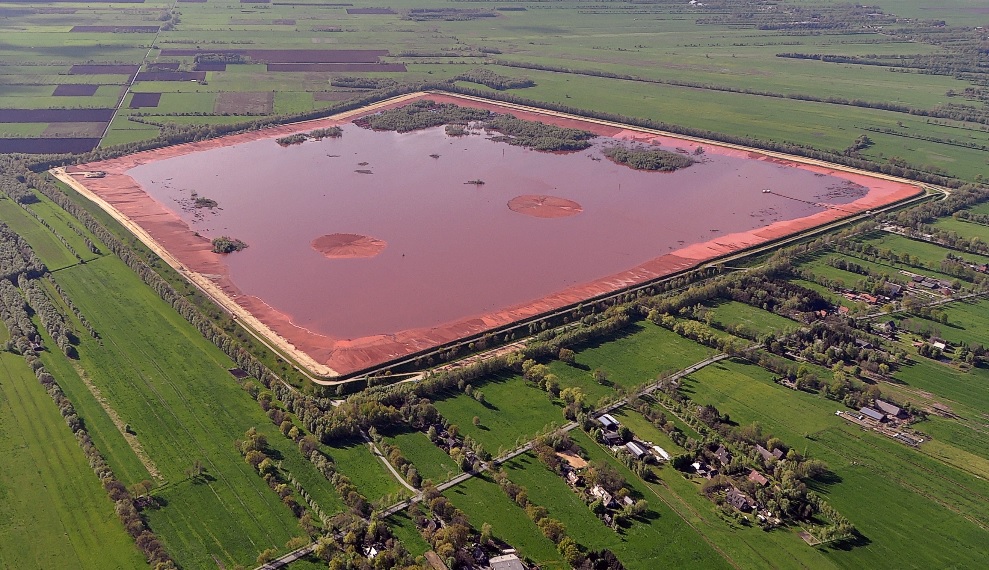
Let’s answer the first question first. Bauxite residue is a waste product produced by the aluminium industry. To answer the second question – more than twice as much bauxite residue as aluminium metal is produced during a standard production and refinement process.
In a linear economy, valuable raw materials are simply dumped
The annual production of 150 million tonnes of bauxite residue corresponds to about 20 kilos per head of the global population! Only between 1 and 2 per cent is recycled in other industries. The rest is dumped. For example, Hydro’s aluminium refinery in Brazil dumps six million tonnes of bauxite residue every year. As well as creating a major potential for local environmental problems, this is also very poor resource exploitation.
Bauxite residue contains up to 50 per cent iron oxide, and more than ten per cent of components such as aluminium oxide, silica, titanium oxide and other substances. Instead of being used as a raw material in the production of iron, silicon, aluminium, cement, building insulation or other products, it is regarded simply as waste. The raw materials for the production of all these products are instead derived from mining activities, which are associated with their own sustainability issues and local environmental damage.
This is simply a glaring example of the linear economy in which value is measured by short-term cycles of supply and demand without any regard for long-term planning for the conservation of natural resources for future generations. As long as the least expensive short-term solution is dumping, no-one can afford to consider any alternatives.
Is bauxite residue an economic or a technological problem?
Bauxite residue is strongly alkali (high pH values) because it contains high concentrations of lye (NaOH). This is why it cannot simply be discharged into the natural environment. In itself, NaOH is not so difficult to deal with and can be neutralised using substances such as hydrochloric acid (HCl) to produce clean water and table salt.
The high sodium content makes it difficult to use unprocessed bauxite residue in the steel industry as a substitute for iron ore. The European alumina producers are working together to find sustainable solutions but this is difficult because they are competing in a global market. A great deal of work is being done to identify applications for bauxite residue outside the aluminium industry. It is technically possible to use it in steel manufacture and in the building industry. However, such applications are not yet commercially viable.
However, the really big problem with bauxite residue is that there is so much of it. The enormous volumes of mud produced make the challenges and problems associated with its management, and the space it occupies, equally enormous. And while we surround ourselves with these great volumes, we are fully aware that technological solutions are available.
In other words, we are dealing primarily with a problem of economics.
Could the solution be one hundred years old – and Norwegian?
Aluminium is currently produced in more or less the same way as it was a century ago. A key intermediate phase in the process is the refining of aluminium oxide from an ore called bauxite by means of the so-called Bayer process.
Today, the Bayer process is used universally throughout the aluminium industry. However, an alternative approach is available. In the so-called Pedersen process, iron is removed as a separate by-product and does not end up in the mud. The mud loses its iron-red colour and instead appears as a “grey mud”, that for the most part consists of calcium carbonate and silica, which can be used as a raw material in cement and fertiliser manufacture.
The Pedersen process
The Pedersen process was developed by Professor Harald Pedersen in Trondheim in the 1920s and was in use at Høyanger for 40 years. However, during the 1960s, it was rendered uncompetitive by the aforementioned Bayer process that was more profitable for the processing of high-quality ore. Today, much of the best aluminium ore in the world has been exhausted, and we are in a situation in which the Pedersen process may represent the best option for the exploitation of lower-quality ores.
For all its advantages, the Pedersen process also has its drawbacks. In addition to, and because of, the fact that it was rendered uncompetitive by a more efficient process in the 1960s, it has not kept pace with industrial developments. The Bayer process has seen a century of investment in machinery, know-how and experience, leading to the optimisation of the process in terms of cost-effectiveness and product quality. The restructuring of an entire industry to accommodate a new process will cost more than willingness and know-how. It will also cost money – involving a transition in an industry that is already surviving on small profit margins and in which no-one has the money to make the first move. Major financial investment will be required to achieve zero waste from the aluminium industry.
A circular economy and a circular society
We need a new way of thinking about value! The technologies are available, but it is far from clear how they can best be implemented. If we are to succeed in transitioning to a circular economy we need new ideas, not only from technologists, but also from economists, industry executives, investors and politicians. This applies not only in the aluminium industry, but in the entire linear economy.
SINTEF is working actively with many projects related to aluminium production and bauxite residue.
We are doing our part to help produce technologies for a better society, and we are confident that we have a solution. But we can’t succeed on our own. We need help!
Comments
Dear SINTEF
As a specialist in the field of disposal of more than 90 types of industrial and municipal waste, I have accumulated vast experience, including with Red Mud. But in order to achieve the maximum environmental and economic efficiency of working with it, you need to know where its dumps are located and what industrial and municipal waste or natural materials are close to the dumps of red mud for their best use as components of new composite materials.
Over the past 22 years, I have worked extensively and very successfully with materials based on Brazilian Red Mud and am ready to transfer my vast experience to the Norwegian fields.
I am waiting for your reaction.
Sincerely
Vsevolod Mymrin
Please see my patents GB 2569767 and GB 2576266. Details on UK Patent Office site.
What minimum content of Al2O3 in Bauxite can be tackled the Pedersen process