Since steel casings and cement both have sufficiently low permeability to be able to work as barrier materials, an important factor is to be able to determine whether the combination of these materials will be able to provide acceptable sealability. Recently, a strong research focus has been shifted towards investigations on the bonding between the cement and adjacent medium, such as the surrounding formation rock and casing. However, despite the extensive amount of research, a standardized testing protocol remains absent. Without a standardized testing protocol, all test setups, even though based on the same concept, will have differences in e.g. dimensions, thus making it difficult to directly compare results. This is a major drawback for the innovation in the industry, especially in terms of development and qualification of new & alternative materials.
Why do we have wells?
Wells have for centuries been vital for human societies. The first wells were used to gain access to underground water sources and were relatively shallow. These wells were dug by hand and the walls were typically reinforced using stone or wood to avoid the wall collapsing and caving in. As technology developed and became more sophisticated, wells could be drilled, rather than dug by hand, enabling utilization of underground resources such as petroleum. In the modern era, wells can be drilled deep into the underground, reaching reservoirs with extreme pressures and temperatures and without any support and reinforcement the wellbore wall will collapse. It is also important to protect the wellbore wall from erosion during extraction of the fluids from the reservoir. Thus, the materials to be placed downhole will have strict requirements in order for the well to be functional at these conditions.
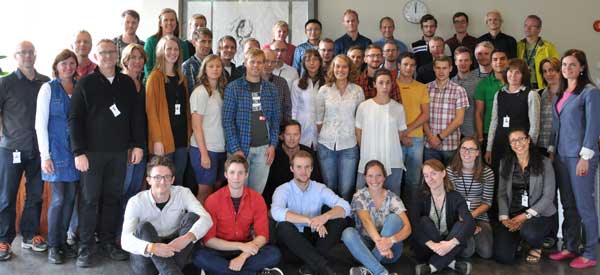
How is the modern well designed?
To operate a well safely and efficiently, steel casings are placed in the wellbore and cement is pumped in the annulus between the casing and the wellbore wall. With this configuration, the fluids from the reservoir are flowing inside a metal casing, which exhibits low levels of erosion while the cement and casing protects the wellbore wall. Another important role of cement and casing is to isolate any sources of mobile fluids above the target reservoir. It is vital to prevent flow between fluid bearing zones to prevent uncontrolled fluid flow or migration. Well integrity is a term used to describe the operations to contain fluids, and it includes technical, operational and organizational solutions for handling the risk of uncontrolled release of fluids. The first documented use of neat cement in relation to petroleum drilling operations dates from 1903. The use of cement would later evolve, and as an example the American Petroleum Institute would develop industry standards for testing cement to further improve the quality of petroleum wells.
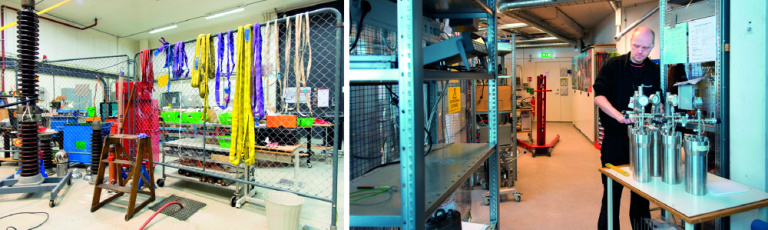
What is cement and what properties are important for cement?
Cement is a binder, which hardens when mixed with water. As the water and cement is mixed, it becomes a relatively thick flowing slurry which is pumpable, and thus placeable in the wellbore, until the chemical reactions render the cement slurry into solid material. An advantage with cement is the versatility, and one can easily tune the properties of the cement by using additives to the mixture. Some additives are used to slow down the hardening process, others can alter the flow properties of the cement to being able to pump the cement a longer distance. Similarly, one can enhance the strength of the cement, make it able to withstand higher temperatures and pressure, corrosive resistant to deal with the harsh conditions downhole.
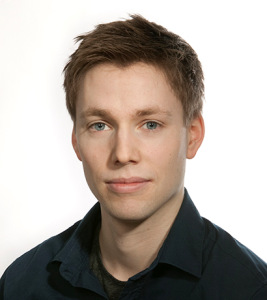
What is currently done in the R&D community to standardize new methods?
The assessment of existing standards, where additions and changes are incorporated, is continuously performed with technological development and industrial needs. As an example of a potential new standard, the establishment of a standard for testing the effect of CO2 exposure on cement properties under downhole conditions is currently in progress under the umbrella of the International Association of Oil& Gas Producers. The motivation for the establishment of this standard is the future implementation of Carbon Capture Utilization and Storage (CCUS).
SINTEF has a strong track record on both research related to well integrity and investigation of materials for Plug and abandonment (P&A). In the Subsurface Well Integrity Plugging and abandonment (SWIPA) center, established in 2020, many of the relevant parameters are being directly investigated. The R&D partners in the center are SINTEF, NORCE, IFE, NTNU and UiS, with financial contributions from AkerBP, Equinor and Wintershall DEA and the RCN. Both UiS and SINTEF have comparable setups enabling to investigate the sealability of cementitious materials to casing. The basic concept of hydraulic sealability tests is to apply a pressure differential across a cement plug and measure the fluid flow rate passing through the specimen.
What cement properties are typically tested?
The downhole conditions in deep wells dictate that both cement and steel casing should have sufficient mechanical strength to withstand the tectonic forces acting on the wellbore. It is also important that the cement is pumpable sufficiently long to be placed in its intended location several hundreds of meters underground. Some examples of standard test procedures for cement slurries are density, rheology, thickening time and early strength development. Examples of standardized testing for solid/hardened cement are mechanical strength and rate of flow through the cement (i.e.permeability). However, these tests are all performed on bulk materials. But the cement should also be able to seal against fluid flow along its interfaces.
Which testing parameters are important to consider for cement sealability testing?
Within this basic concept there are many potential differences that could have an effect/influence on the test results. One example is the apparatus assembly and design, this also includes elements such as the size and geometry of the cell. Another important example are the pressure and temperature conditions to which the testing will be performed. A third possible element is the testing protocol itself. This element includes cement curing time and conditions, whether the pressure differential would be done by increasing or decreasing the pressure on one of the cement plug sides.
What could be the way ahead?
Furthermore, as the field progresses, the emergence of novel barrier materials with diverse chemistries, such as geopolymers, unconsolidated slurries, and metal alloys, necessitates rigorous testing, verification, and qualification. Additionally, the industry is moving into new territories/applications, such as unconvetnional hydrocarbons resources, geothermal energy or CCUS, the need for a further development of testing methods for these materials become apparent. A specific standard for the experimental testing of sealability of cement-casing could facilitate an acceleration of these new applications.
Read the published article “Raising the Bar: Why an Industrial Standard for Testing Hydraulic Sealability of Well Abandonment Materials in Laboratory is Essential for Well Integrity”
Comments
No comments yet. Be the first to comment!