CO2 capture from cement production is possible, there are several possible capture technologies, different technologies can be suitable for different cement plants, but only amines are currently mature enough for full-scale projects.
This is a very brief summary of the 2nd ECRA/CEMCAP Workshop that was recently arranged within the H2020 project CEMCAP by project partner ECRA in Düsseldorf. The workshop gathered over 80 participants from research and industry.
- All presentations and posters from the workshop are now available on the CEMCAP website.
Poster session and welcoming address
The event begun in the evening of November 6 with a gathering combining a dinner and poster session. On the posters achievements and conclusions so far in the CEMCAP project were presented, and there was also a poster about the ECRA CCS project and from the ECRA Chair at University of Mons.
November 7th, the full-day workshop begun with a welcoming address from Martin Schneider of ECRA.
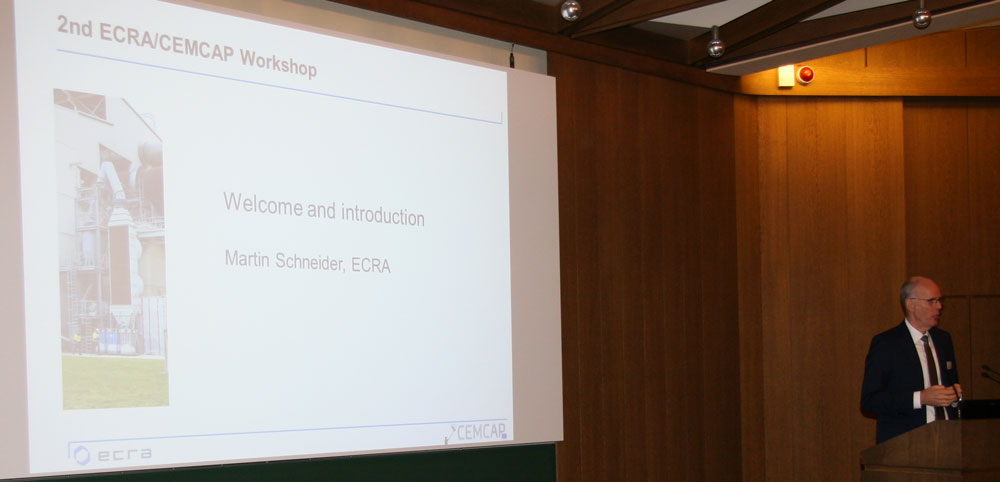
CCS nessecary to curbe industrial CO2 emissions
Thereafter Carlos Abanades from CSIC set the scene for CEMCAP with his presentation on the necessity to apply CO2 capture and storage (CCS) to curb industrial CO2 emissions in order to mitigate climate change. Carlos also in a simple manner clarified why CO2 capture and use (CCU) cannot suffice as a climate change mitigation measure in a future that needs to go CO2-negative.
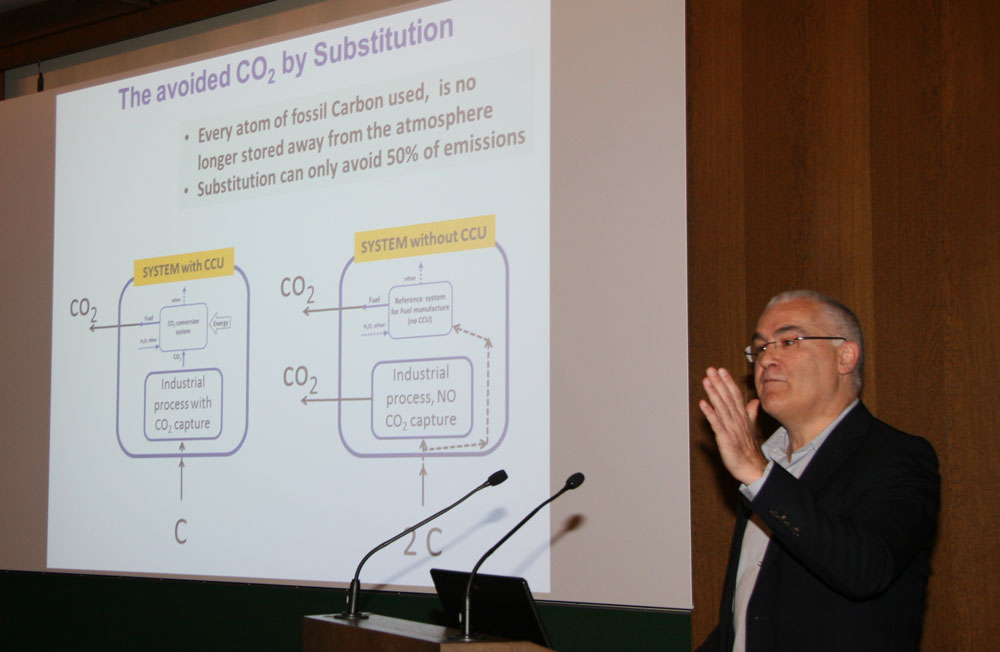
The CEMCAP project
The presentations of CO2 capture technologies started with an introduction to the CEMCAP project by Coordinator Kristin Jordal, after which Robert Mathai of IKN gave a clear and detailed presentation of the challenges, learnings and achievements with the on-site testing of the oxyfuel clinker cooler prototype at the HeidelbergCement plant in Hannover.
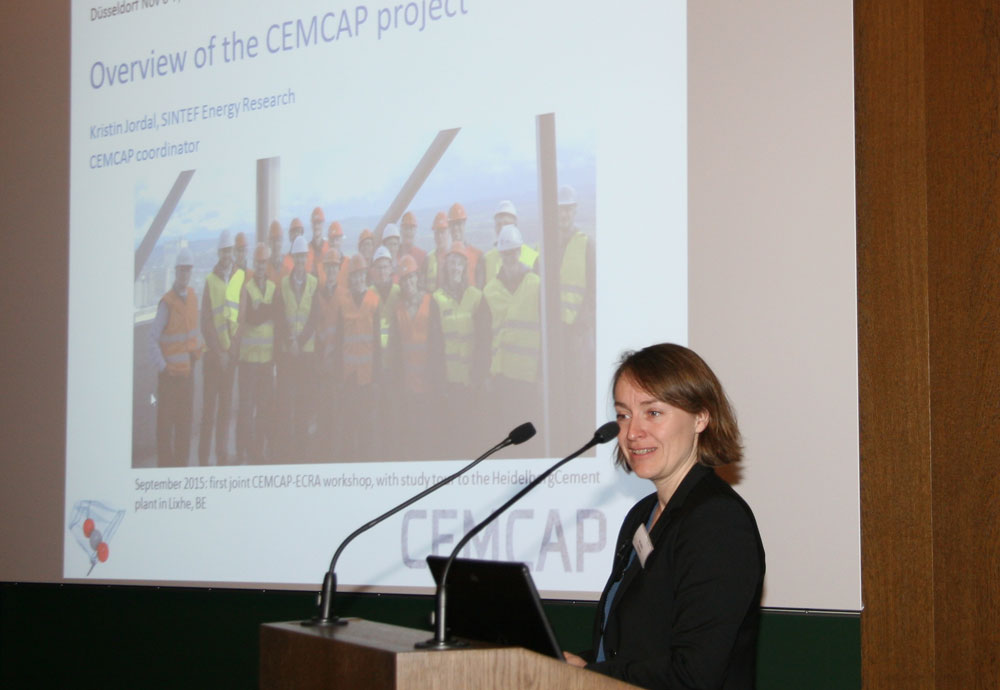
The presentation was followed by a world premiere of the film that has been made in CEMCAP to document the clinker cooler tests. The film will be made available through YouTube very soon.
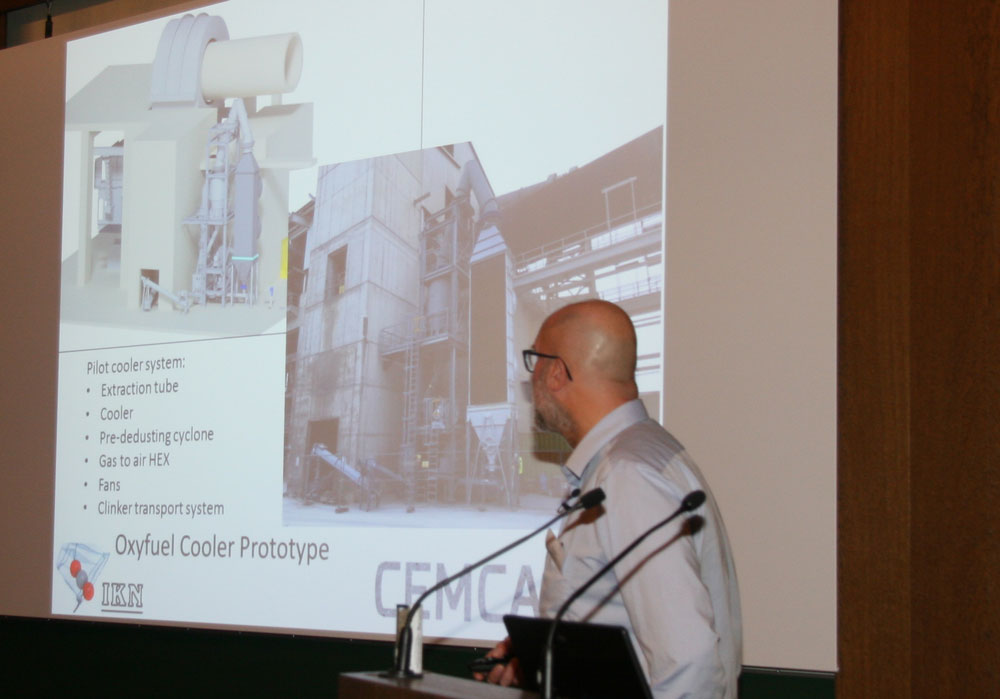
Oxyfuel CO2 capture in cement plants
Jost Lemke of ThyssenKrupp Industrial Solutions presented the perspective of a technology supplier on oxyfuel CO2 capture in cement plants. As he summarized it, oxyfuel technology for cement kilns is feasible, but everything will need some adjustments.
For instance, tests in CEMCAP of a scaled down standard oxyfuel cement kiln burner have revealed that existing burner designs can be used, with a slight increase in oxygen concentration compared to air, whereas the kiln CO2 recirculation loop and process control need more attention.
Finalised experimental work
Calcium looping is one of the post combustion capture technologies in CEMCAP where the experimental work has recently been finalised, showing no showstoppers for the calcium looping technology for the cement application.
Further, it has been concluded that the entrained-flow (EF) calcium looping technology is more promising than the more mature tail-end circulating fluidised (CFB) calcium looping technology – it is more energy efficient, but requires tighter integration with the plant. The EF technology will be further developed in the CEMCAP “spin-off” Horizon 2020 project CLEANKER.
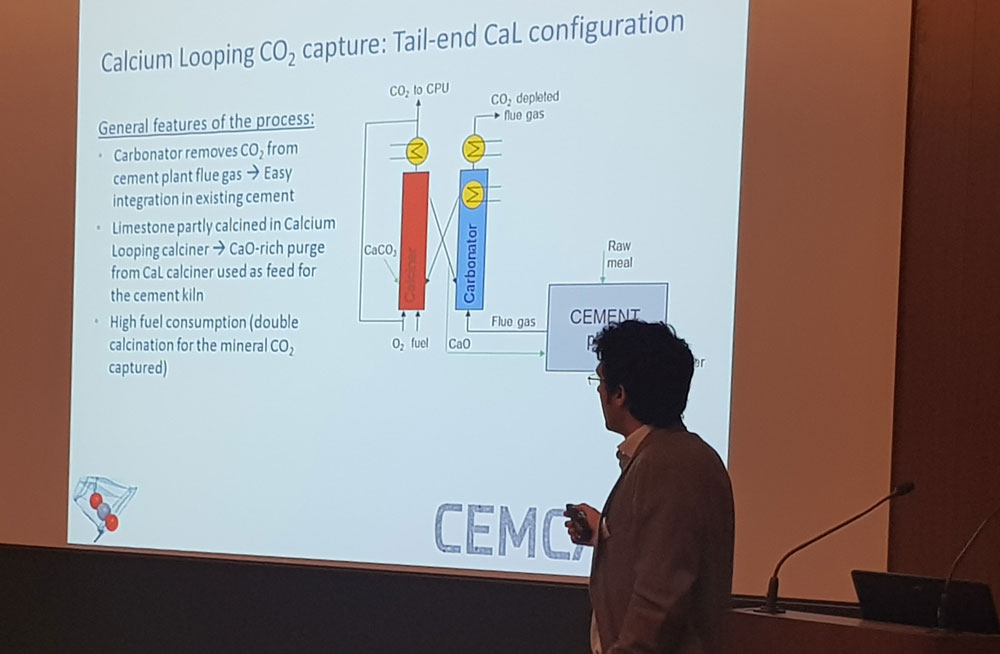
On-shore CO2 storage pilot
After lunch Axel Liebscher from GFZ Potsdam presented the successful results from the completed on-shore CO2 storage pilot in Ketzin, Germany. In brief, it has been proven that geological CO2 storage works. Many different monitoring techniques have been applied at the Ketzin test site, all confirming that there is no sign of leakage of the stored CO2.
Membrane-Assisted CO2 liquefaction
David Berstad from SINTEF presented Membrane-Assisted CO2 liquefaction (MAL), a hybrid post-combustion capture process concept where membranes are used in a first step to enrich the CO2 from the cement plant exhaust. Thereafter, the CO2 is at “near oxyfuel” conditions and ready to be compressed and liquefied, whereby it reaches very high purity (99+ %) and is ready either for being loaded directly onto a ship, or pumped to reach the conditions required for pipeline transport .
Technology and market options
CO2 capture and Use (CCU) is sometimes presented as a way of doing business out of captured CO2. Juliana Monteiro from TNO presented the work done in CEMCAP on screening different technology options, and also quantifying what the market may be for different CO2-derived products, what the energy consumption is, and a quantification of requirements on wind power as renewable energy source.
In brief, there may be some niche markets, such as for polyols that could provide an uptake of a small share of the CO2 produced by a cement plant. In this case, a combination of CCU and CCS can lower the overall costs. Further, methane production from captured CO2 may sometimes appear attractive, but this option requires large amounts of renewable power for production of hydrogen needed in the process, and is only relevant in special cases.
CEMCAP and CLEANKER are not the only H 2020 projects on CO2 capture from cement. Mark Sceats from the mineral processing company Calix presented the externally-fired calciner technology that will be tested on site in H 2020 project LEILAC at the Heidelberg Cement plant in Lixhe, BE. Commissioning of the LEILAC pilot plant will begin towards the end of 2018, and a successful project will eventually provide a means to capture concentrated CO2 from lime and cement industry calciners.
Norwegian full-scale CCS project
Last but not least during the workshop Per Brevik from Norcem presented the Norcem vision to be CO2 neutral by 2030, and their participation in the Norwegian full-scale CCS project led by Gassnova. In this project, CO2 captured from 1-3 industrials sites in south-eastern Norway will be liquefied and transported by ship to a CO2 hub in western Norway. From this hub, there will be pipeline transport of CO2 to an off-shore storage site (Smeaheia). Norcem is one out of three candidates for industrial capture sites. They have chosen their preferred capture technology, which is an amine technology from Aker Solutions.
On-shore CO2 storeage is possible
The workshop was concluded with a plenary discussion on several of the topics presented during the day. Altogether, it was a workshop with interesting presentations, focusing on CO2 capture technologies, but also spreading the knowledge that on-shore CO2 storage is possible, and that one must take care and use a sufficiently large boundary when estimating the CO2 mitigation effect of products made from CO2.
The third and final ECRA/CEMCAP workshop will be arranged in Brussels in mid-October 2018. If you want to receive updates on the exact date and venue or are generally interested in CEMCAP progress, sign up to the CEMCAP newsletter by sending an e-mail to cemcap@sintef.no.
Comments
No comments yet. Be the first to comment!